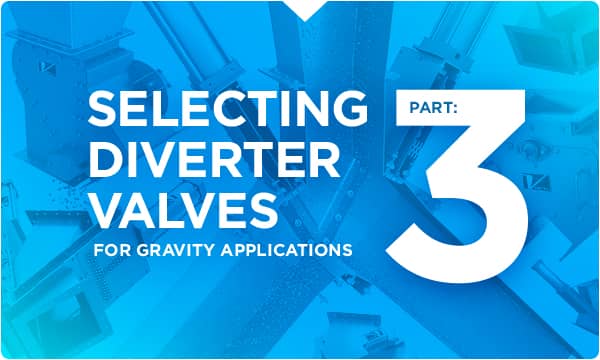
Client:
Quantity:
Size:
Application:
When you browse through Vortex’s product catalogue, you may notice a wide variety of standard and engineered diverters for gravity flow applications. This is not by accident or due to the fact that we love to design multiple products that achieve the same result! This article covers the differences between multiple diverters and address factors that impact selection, based on application.
To be clear about the term “gravity flow," Vortex defines it as an application where air pressure or vacuum is not used to assist material conveyance. The primary factor that drives the selection of a gravity diverter is the particle size and/or abrasiveness of the material handled. Another driving factor is the bore size of the valve required.
Vortex manufactures six types of diverters that are suitable for handling material in gravity flow:
- Seal Tite Diverter
- Gravity Vee Diverter
- Flex Tube Diverter
- Aggregate Diverter
- Titan Lined Diverter
- Pivoting Chute Diverter
To conclude the three part series, this article will cover the Titan Lined and Pivoting Chute Diverters.
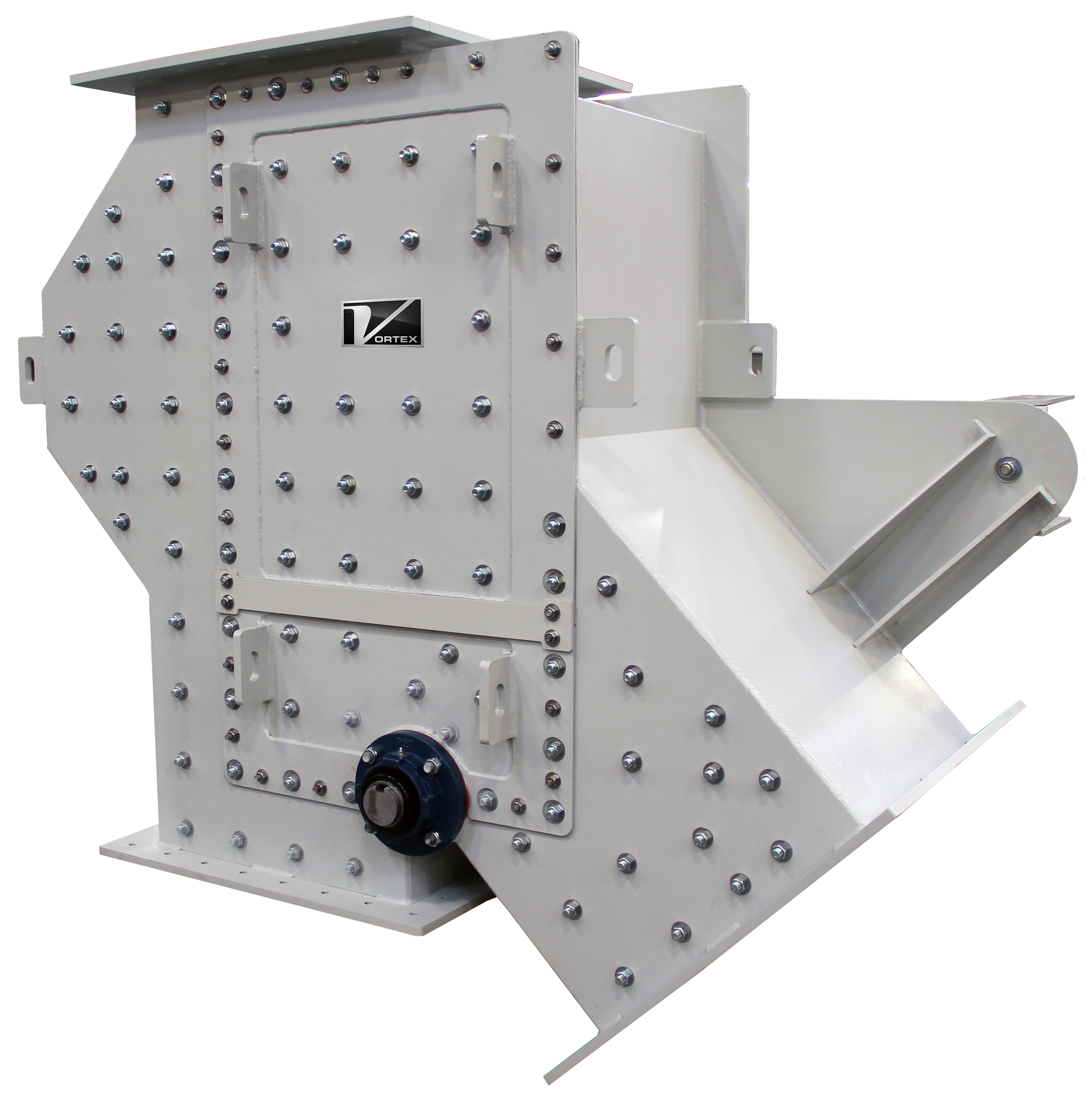
Titan Lined Diverter
The Titan Lined Diverter (TLD) was designed for use in gravity flow applications handling abrasive materials such as coal, rock or industrial sand, that require an environment sealed from dust and fine powders.
The TLD channels the flow of material away from the leading edge of the flapper vane. This feature is critical to maintain seal integrity and inhibit material leakage across the closed legs of the valve. Traditional flapper diverters have a tendency to leak past the vane shaft and trap material underneath which may cause actuation problems. The TLD includes a shaft seal to eliminate this problem. To extend the life of the diverter, the TLD features abrasion resistant liners that can be replaced when needed prolonging the life of the diverter. The TLD also comes standard with removable access panels for inspection, cleaning and maintenance.
Standard sizes of the Titan Lined Diverter range from 400mm | 16 in to 900mm | 36 in.
Pivoting Chute Diverter
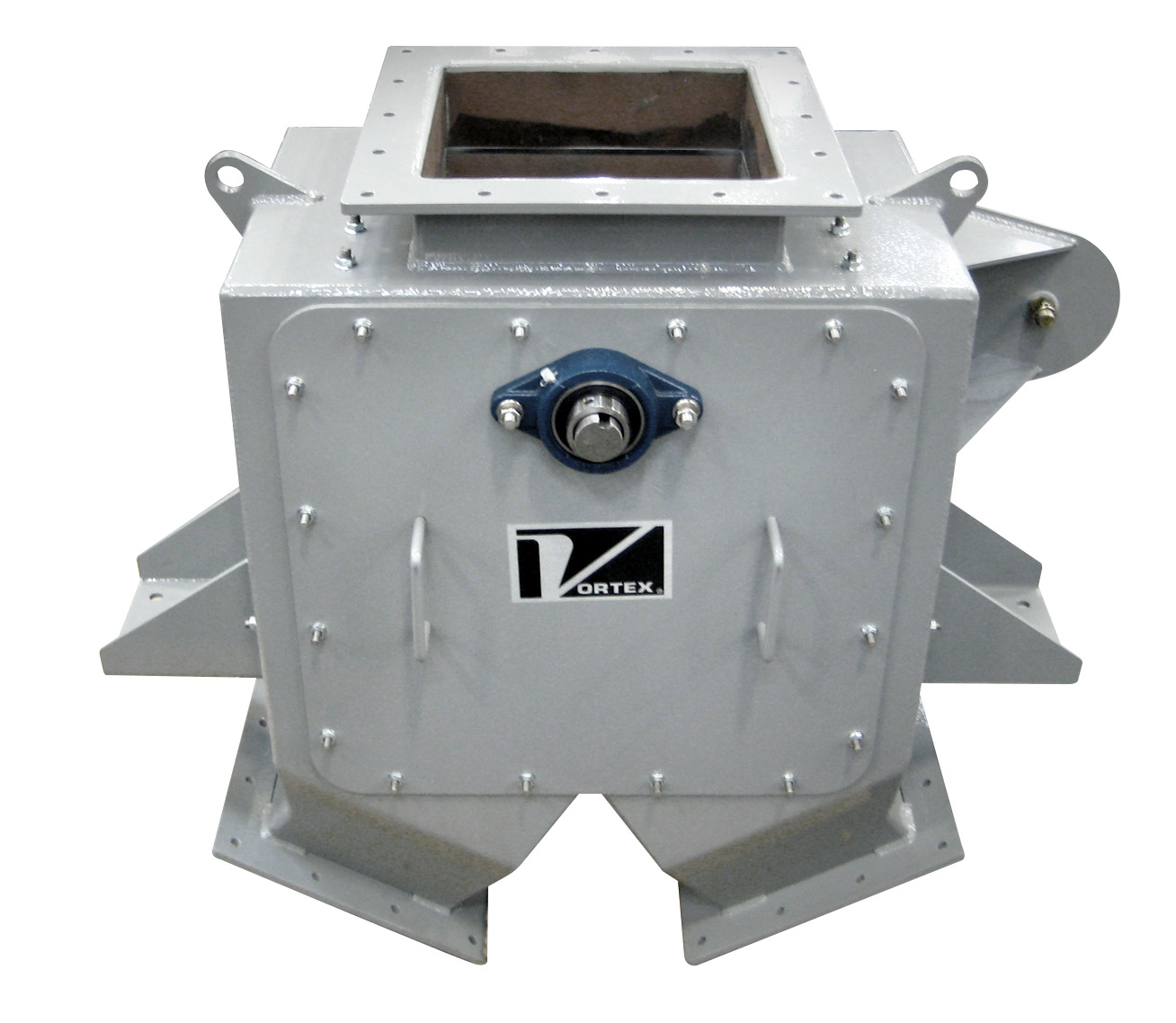
Vortex developed the Pivoting Chute Diverter for abrasive materials such as industrial sand, limestone, coal, gypsum, clinker, gravel, bauxite, whole grains, and minerals. The diverter body houses an internal chute that pivots to direct the material flow. The main advantage of the Pivoting Chute Diverter is that there are no internal seals to maintain. The chute addresses material abrasion and can be constructed of, or lined with, wear resistant materials (e.g. chromium carbide, abrasion-resistant steel, or ceramic).
Inspection, maintenance, or repairs to the diverter may be performed from the front access panel – without removing the diverter from service. This diverter is dust-tight to atmosphere, may be shifted “on-the-fly”, and is available in two-way and three-way configurations. Additionally, the chute may be positioned to split flow to both directions simultaneously.
Standard sizes of the Pivoting Chute Diverter range from 1500 mm | 6 in to 600 mm | 24 in. Very fine, fluidizable material may migrate to the off leg. For fine, abrasive material, consider the Titan Lined Diverter.