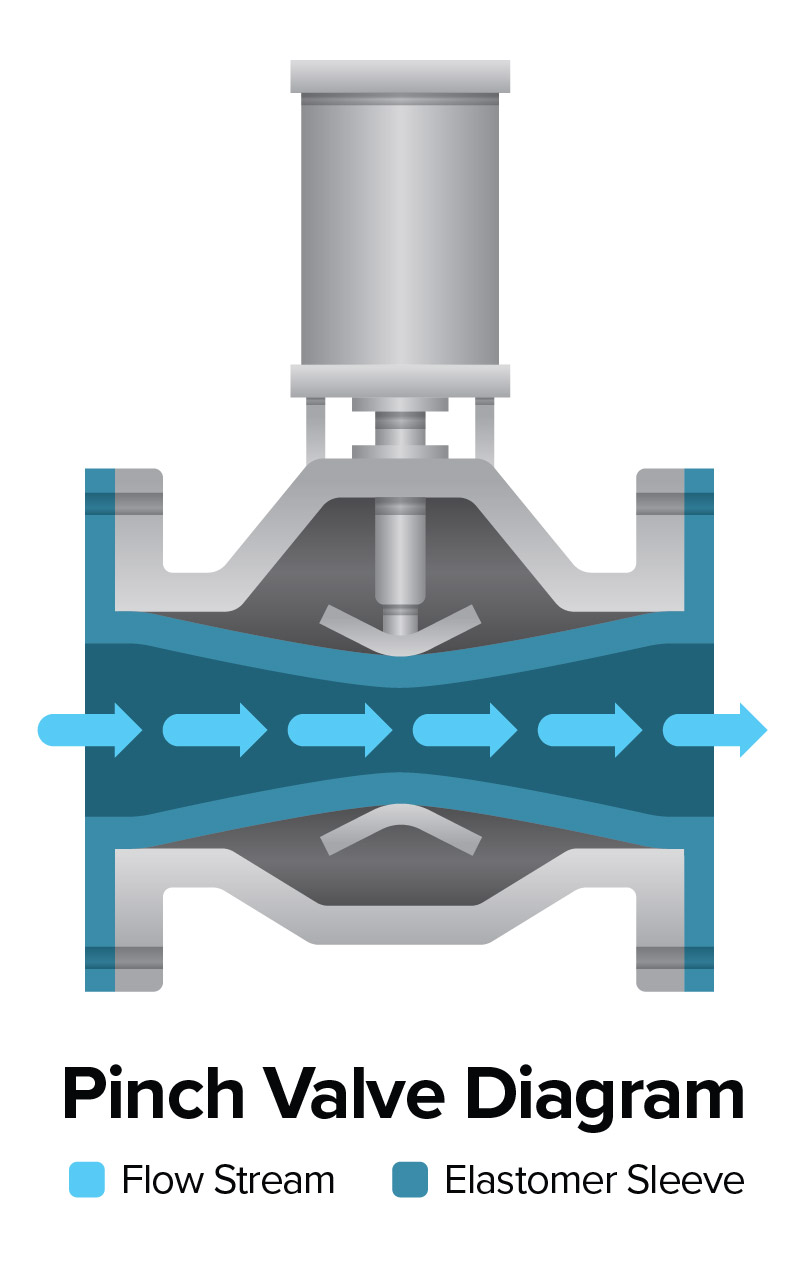
Client:
Quantity:
Size:
Application:
Q&A: Insights about Slide Gates vs. Pinch Valves
Q: What are the primary differences between pinch valves and slide gates in material handling systems?
A: Pinch valves and slide gates each serve unique functions in material handling systems. Pinch valves feature an elastomer sleeve that compresses to halt flow, making them ideal for managing media flow in low to moderate pressure applications, particularly for liquids and slurries. Conversely, slide gates utilize a sliding blade mechanism to regulate material flow, equipped with durable polymer or metal seals, making them perfect for handling dry bulk solids.
Q: How do durability and maintenance requirements compare between these two types of valves?
A: Pinch valves generally require more maintenance due to the wear and tear on their elastomer sleeves, especially in abrasive applications. These sleeves can wear out quickly, necessitating frequent replacements. Slide gates, with blades constructed from various steel alloys and a variety of seal options suited to the material they handle, usually have a longer lifespan, and require less frequent maintenance, making them more durable over time.
Q: In what scenarios would slide gates be preferred over pinch valves?
A: Slide gates excel in systems that demand precise material flow control, offering superior performance compared to pinch valves due to their advanced blade technology. Their capability to operate under vacuum conditions and tolerate a broader temperature range makes them ideal for challenging environments. In high-pressure applications, slide gates outshine pinch valves, thanks to their robust construction typically crafted from high-strength steel alloys. This durability ensures they withstand high pressures without compromising functionality, unlike pinch valves, whose elastomer sleeves are prone to deformation and failure under such conditions. The blade mechanism in slide gates not only ensures reliable sealing but also maintains structural integrity in tough environments. For applications requiring consistent and resilient performance under high pressure or vacuum, slide gates are the optimal choice.
Q: Can both pinch valves and slide gates be used in high-temperature applications?
A: While pinch valves can operate in a range of temperatures, their performance is limited by the elastomer sleeve, which may degrade in extreme heat. Slide gates, with their steel construction and hard polymer or metal seals, have a more extensive temperature range, making them more suitable for high-temperature applications.
Q: What is the impact of installation height on the choice between pinch valves and slide gates?
A: Slide gates typically require a shorter "flange to flange" installation height compared to pinch valves. This compact design can be advantageous in installations with limited stack up space, providing greater flexibility and ease of integration within the system.
Q: How do slide gates and pinch valves handle columned material?
A: Slide gates are engineered to cut through static columns of material, making them ideal for applications prone to material blockages. Conversely, pinch valves, which rely on a compression mechanism, can struggle in these situations, potentially causing flow interruptions and blockages.
Conclusion
In conclusion, slide gates present a superior alternative to pinch valves for managing dry bulk materials across diverse industrial applications. Crafted with blades made from durable steel alloys and seals from various polymers and metals, slide gates offer exceptional longevity and require less maintenance than the elastomer sleeves in pinch valves, which deteriorate quickly under abrasive conditions. Slide gates excel in precise material flow control, accommodate a wide temperature range, and operate effectively under vacuum/high pressure conditions, making them highly versatile for demanding environments. Furthermore, their compact design reduces installation height, making them ideal for intricate, space-constrained systems. By choosing slide gates, industries can achieve enhanced performance, reliability, and operational efficiency in their material handling processes.
Contact Vortex today to learn more about the right slide gate for your material handling process.