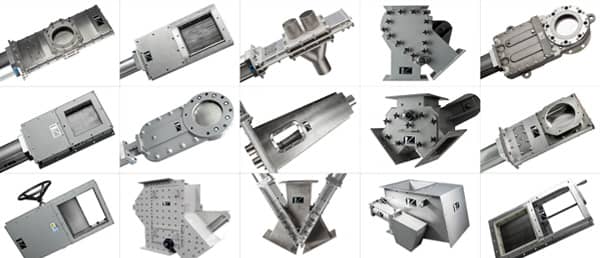
Client:
Quantity:
Size:
Application:
By Lisa Johnson
Many people think that selecting a slide gate or diverter for handling dry material should be a relatively simple process. They typically assume the only information they need is:
· Size of the opening
· Shape of the opening
· Available stack-up height
· Matching connections or hole patterns
But in reality, valve suppliers need more information to accurately select the right valve for the application. Costly mistakes can be avoided the more information about the application parameters a supplier has; like purchasing an expensive valve for a simple application, or buying an inexpensive valve that cannot handle a difficult. Valve suppliers should have the experience and knowledge to know what valves and valve modifications to apply for certain applications parameters. Make sure your supplier is asking the right questions.
So let's begin with the premise that each application for a slide gate or diverter valve has its own unique requirements. What are the factors that determine what type of valve is selected and what modifications are necessary?
Valve Selection
Installation criteria determines which valve line is appropriate. The most critical question is "what is the valve intended todo?" Is a slide gate, diverter valve, iris valve or a butterfly valve needed to best fulfill the application? After this question is answered, you can follow up with these questions.
· What is the opening or orifice size?
· Is the opening square or round?
· Will the valve be used in differential pressure or gravity application?
· Will the valve be installed indoors or outside?
· What is the temperature of the air and material conveyed?
· Does the system use dilute, phase, dense phase, vacuum, or gravity to convey material? If pressure or vacuum, how much?
· What is the size of the conveying line?
· Are the lines tube or pipe? If the lines are pipe, is it schedule 10 or 40?
· Does the valve material contact need to be carbon steel, stainless steel, or aluminum?
· Will the valve be subject to wash-downs? If so, will it be washed with hot water or a caustic liquid?
· Will there be flow aides such as aeration or vibration if the valve is mounted below a bin/silo?
· What is the sequence of operations for the system, e.g., When are the flow aids activated in relation to the cycle of the gate valve?
· If the slide gate is designed for gravity and is mounted below a bin/silo, then how is the material conveyed into the bin/silo?
Then you need to consider the material characteristics.
· What is the material to be conveyed?
· Is the material in powder, granular, or pellet form?
· What is the particle size of the material?
· What is the weight of the material per cubic foot?
· Is the material sticky, abrasive, or corrosive?
· Is there spoilage or sanitary issues with the material?
· Will different types of material be conveyed through the same line? If so, are there cross contamination concerns?
Actuator Selection
There are many types of actuators to operate the valve to open and close. Depending on system requirements and power availability, actuators can be automated or manual. Automatic actuators are available such as air cylinder, air cylinder with magnetic piston, electric actuator, explosion-proof electric actuator, and hydraulic actuator. Manual actuators available are hand wheel, hand crank, and chain wheel actuators. To define which one you'll need, you'll need to answer the following questions:
· What is the cycle frequency?
· Will the valve close on material? If so, will the material be standing or moving column?
· Is compressed air available?
· Does actuation speed matter?
· What are the cost variables for replacement and repair?
· Can I use manual actuation when the valve is only for maintenance purposes?
· Will the valve be outside in cold temperatures?
· Does it need to meet electrical classifications like Voltage, NEMA or ATEX?
Standard Modifications
Determine if the company that is manufacturing your valve offers standard modifications to suit application/material specific requirements. Some application specific factors that would need to be considered for valve modifications are:
· Duty Cycle
· Abrasive Duty
· Corrosion
· Chemical Compatibility
· Particle Size
· Friability
· Temperature
· Serviceability
· Food Specific
· Indoor/Outdoor Service
Some valve modifications that can serve these challenges in the bulk powder industry are Stainless Steel Material Contact, Water Wash Down, High Temperature Service, Cold Temperature Service, US Dairy Standard, Flexible Hose, Schedule Pipe Size, Clear Bonnet Covers, Straight Leg, Fabric Sleeve, Sealed Body, Stainless Steel Rollers, Seal Access/Removable Seals, Abrasion Resistant Blade, Clean In Place, Round & Square Transitions, 30 Degree Offset and Internal Diverter Linings, just to name a few.
Valve Location & Orientation
Designate where the valve is to be installed and the orientation of the valve. The position of a slide gate or diverter valve in a system helps determine which accessories may be required for your application. For example, if a slide gate is to be mounted below a surge hopper, positioning controls may be required to meter material into the weigh hopper.
Accessory Selection
There are four distinct areas to address when specifying accessories for valve.
1. Motion controls - Intermediate positioning is available via a variety of methods depending on specific installation criteria.
· VPO/VPC - relay control with manual adjustability
· AVP - PLC control with manual adjustability
· IVP - Infinitely Variable Position Control via 4-20mAsignal
2. Feedback - For added valve control, manufacturers can provide customers with push-button control panels to suit your valve control needs. Manufacturers can also utilize state-of-the-art valve/sensor manifold technology with a variety of PLC interfaces on multi-port diverter assemblies.
3. Safety Devices - A vented ball valve should always be installed in front of the air control valve in order to bring the slide gate or diverter valve to zero mechanical state before servicing. This style of ball valve bleeds off any residual downstream pressure contained in the air lines supplying the air cylinder. The ball valve should always be installed within easy arm's reach of the air control.
4. Fabricated Accessories - Fabricated transitions provide flexibility for customers with existing equipment. Transitions can address custom flange-to-flange dimensions. They may also be fabricated to contain flanges that match special bolt patterns, tube stubs, sock beads, or blind flanges that allow in-the-field hole placement and installation.
Features Selection
There are a number of different features available when selecting a slide gate or diverter valve. Each manufacturer will have their own standard products.
Adjustable Rollers- Externally greased hardened steel adjustable rollers are used to keep the blade dust tight.
Abrasion Resistant Liners - Abrasion resistant liners positioned at the inlet of the gate address potential wear issues that may exist from either the volume or the abrasiveness of the material being handled. The liners are replaceable when needed.
Abrasion Resistant Blade -The gate's blade can also manufactured of abrasion resistant steel. The combination of the abrasion resistant blade and liners are important in providing a gate that offers longevity and an exceptional life-cycle cost.
Displacement End Pocket - A displacement pocket displaces the material at the leading edge of the blade as the blade closes. Rather than the blade jamming and packing this material into an end seal, the blade stops part way into the pocket. Material falls away from the blade and re-enters the material flow stream area. This feature can increase the valve's service-life and reduce downtime costs related to maintaining and replacing end seals.
Bonnet Purge - The optional bonnet purge is utilized to keep material out of the body of the valve and in the material stream.
Replaceable Seals - Seals reduce interior valve dusting and can be replaced while the valve is inline.
Wear Compensating Seals - Pressure loaded, polymer bonnet seals offer a dual purpose. They act as a wiper for material that may be on the blade as the blade retracts. They also seal material from entering the bonnet area of the gate. The "live load" on the back of the seal strip continues to apply pressure to the seal even as it wears. At a certain wear point, seals may be accessed and replaced from the outside of the gate, while the gate remains inline.
Wear Reducing Material Deflectors- Material deflectors are placed around the inlet of the valve and protect it from the material flow stream. By deflecting material away from the hardened steel rollers and blade seals, this feature significantly reduces wear and downtime keeping the valve in service longer.
Available Sizes- Valve standard sizes will be dependent on the valve and the manufacturer. Contact your manufacturer for available sizes.
Return Pan - A return pan can be added to seal fine material internally or to atmosphere. With this feature, material that enters the bonnet of the valve is returned to the material flow stream, thus reducing material leakage to atmosphere.
Wear Resistant Bucket Design - A wear resistant bucket constructed from durable abrasion resistant steel and an optional ceramic liner can be added to reduce potential wear to the bucket. For even more durability, the additional of an optional honeycomb liner allows material to abrade on itself instead of the bucket.
Optional Configurations - Available in straight leg and wye line configurations.
A lot of questions come in to play to select the right valve for your application. But, if you are prepared with the information for your manufacturer, you can be confident that you have purchased the solution to your needs. If your manufacturer doesn't ask specific detailed questions, you might end up paying too much for a simple valve that doesn't meet your requirements, and you'll end up wasting factory time and money to modify the valve for your application.