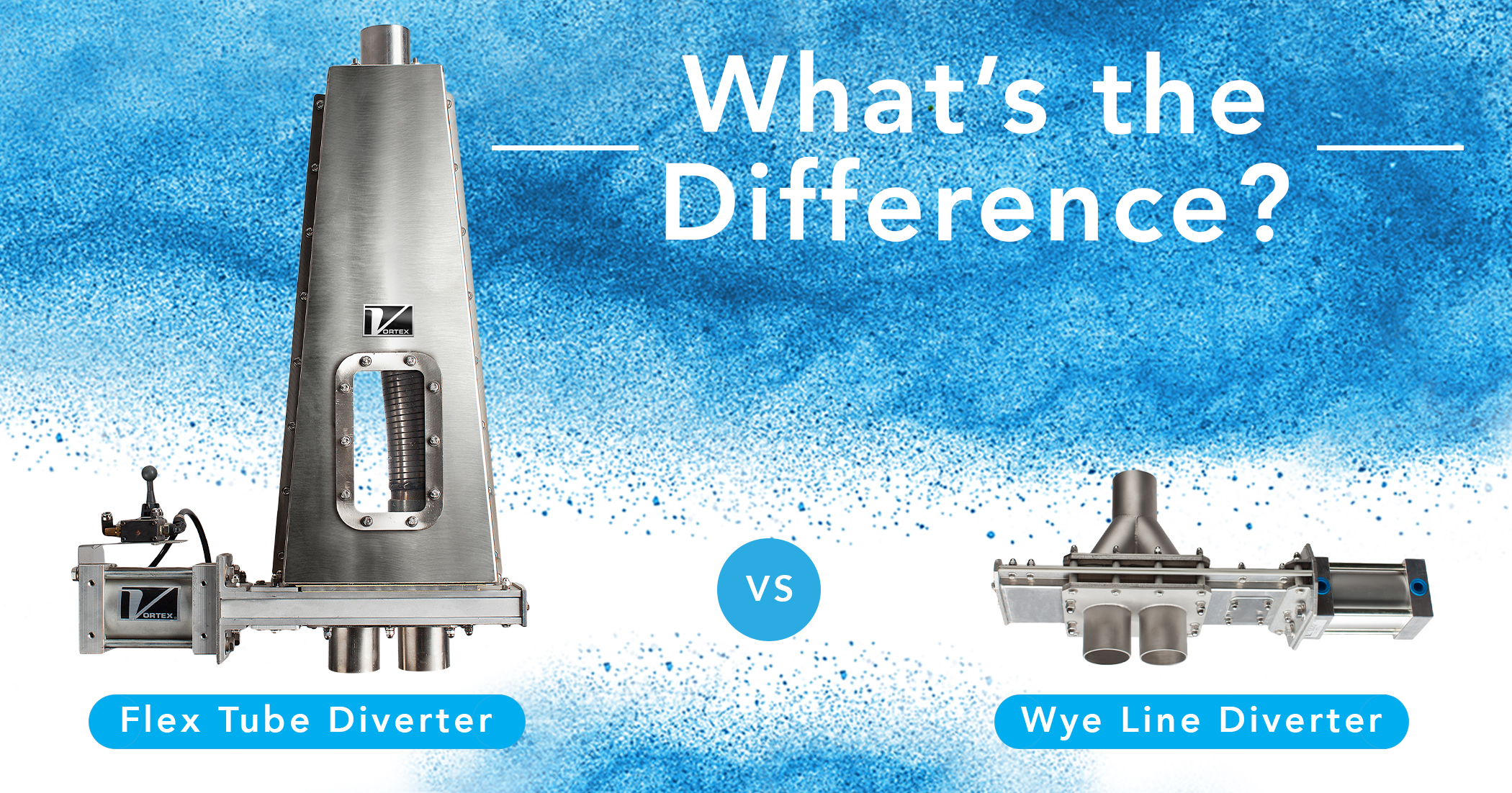
Client:
Quantity:
Size:
Application:
The Wye Line Diverter and the Flex Tube Diverter are among Vortex’s most popular diverter valves for pneumatic conveying applications. This white paper will discuss the features, benefits and other considerations for these two valve designs.
Primary Differences
There are two primary factors when considering the Wye Line Diverter and the Flex Tube Diverter. Those being:
- Concerns for material cross-contamination
- Available space/stack-up height
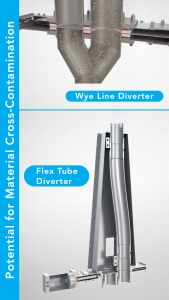
Material Cross-Contamination
Both the Wye Line Diverter and the Flex Tube Diverter are specifically designed to address material cross-contamination.
In the Wye Line Diverter, a naturally occurring high-pressure airfoil deflects errant materials away from the closed port(s) and back into the material flow stream. Because of this, very few material particles fall out of suspension upon arrival at the diverter, causing them to collect in the closed port(s). With each purge cycle, those residual materials are forced downstream through the open port. Thus, the Vortex Wye Line Diverter is designed to address material cross-contamination, but it is still possible.
In the Flex Tube Diverter, a flexible hose shifts between outlet ports. The primary difference between the two diverter designs is in the Wye Line Diverter, the closed port(s) are constantly exposed to the material flow stream, whereas in the Flex Tube Diverter, the closed port(s) are completely isolated as the flexible hose creates a one-to-one inlet/outlet connection. For this reason, the Vortex Flex Tube Diverter eliminates the risk of material cross-contamination.
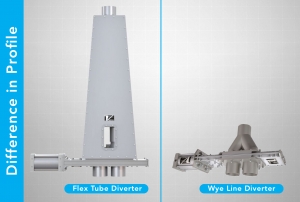
Available Space/Stack-Up Height
The Wye Line Diverter is specifically designed with a narrow profile, so that it can be easily integrated into limited space installations.
Alternatively, because the Flex Tube Diverter houses a flexible hose, its profile is 2-3 times larger. To ensure conveying efficiency, hose length and degree of bend can vary, depending on application. This can add to overall profile/stack-up height.
Other Differences
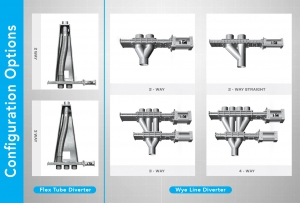
Number of Sources/Destinations
Both the Wye Line Diverter and the Flex Tube Diverter can be used to either divert or converge. The Flex Tube Diverter is limited to two- and three-way configurations, whereas the Wye Line Diverter offers two-, three- and four-way configurations. For a greater number of sources and/or destinations, both the Flex Tube Diverter and the Wye Line Diverter can be engineered as a Multi-Port Diverter, if space is available.
Conveyance Type
Both diverters can be used in vacuum or dilute phase pneumatic conveying applications up to 15 psig | 1 barg, depending on valve size.
The Flex Tube Diverter can also be used in gravity flow applications. The Wye Line Diverter is typically not recommended for use in gravity flow applications because without conveying pressure, the naturally occurring high-pressure airfoil cannot take place. As a result, materials can collect in the closed port(s) and create plugs.
What's in Common?
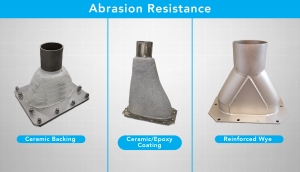
Abrasion Resistance
Both the Wye Line Diverter and the Flex Tube Diverter can be used to handle moderately abrasive dry materials. The Wye Line Diverter can be modified with an optional ceramic/epoxy coating, or ceramic backing, or a reinforced weldment to ensure its success in abrasive applications. The Flex Tube Diverter is designed to reduce wear by creating a more gentle flow as materials pass through the hose.
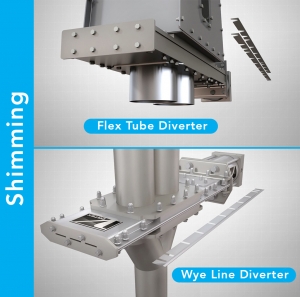
In-Line Maintenance
Both diverters are designed with in-line maintenance features. Both diverters feature pressure plate seals constructed from hard polymer and compressed rubber backing. Once the compression load is reduced, shims can be removed along the lateral aspects of the gate and the bolts retightened to restore the compression load. In the Flex Tube Diverter, the flexible hose housing can be designed with a removable access panel that allows for inspection and/or hose maintenance while the diverter remains in line.
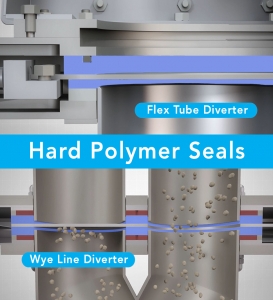
Hard Polymer Seals
To ensure product quality, both diverters are designed to minimize material shearing upon gate closure. Both are also designed without internal cavities, to prevent wedging, lodging and spoilage. The Wye Line Diverter and the Flex Tube Diverter are designed with hard polymer seals to eliminate metal-on-metal contact, which could otherwise create foreign metal contamination from galling.
Other Common Features:
Both diverters can be installed in either a vertical or horizontal orientation.
To ensure conveying efficiency, both diverters feature a sliding blade designed with a machined, full-bore orifice. This maintains convey line pressures and creates an unobstructed material flow stream. Both diverters also provide a positive seal across the closed port(s) and to atmosphere.
For improved processing speeds, both the Wye Line Diverter and the Flex Tube Diverter are capable of shifting through a flowing column of material – also known as, “shifting on the fly.”
Which Diverter Should I choose?
While the Wye Line Diverter and Flex Tube Diverter are both excellent options for handling most powdered, pelletized or granular dry materials, it is critical to first consult with your valve manufacturer prior to making a decision. With so many variables to consider – and countless more left unmentioned – it is of utmost importance to seek advice and gather knowledge from industry experts to ensure your selection is truly the best solution for its application.
With more than 300 years of combined experience in the dry bulk solids industry, clients can be assured Vortex application engineers will listen to your needs and rely on in-depth knowledge of dry solids to develop the right solution for even the most demanding applications.
For more information on the Wye Line Diverter or Flex Tube Diverter, or to discuss your material handling needs, please contact us.