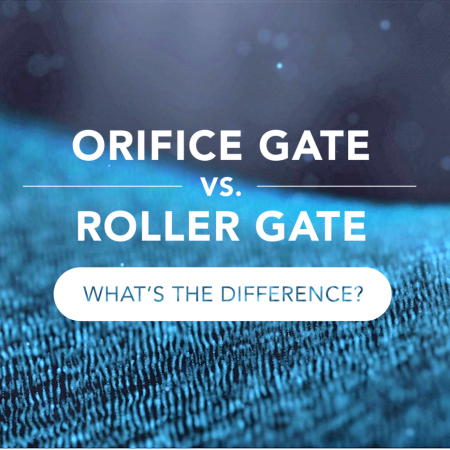
Client:
Quantity:
Size:
Application:
Since their conception decades ago, the Vortex® Orifice Gate™ and the Vortex® Roller Gate™ have been two of Vortex’s most popular solutions for handling dry bulk solid materials. By their simplest definitions, both the Orifice Gate and the Roller Gate are slide gates. However, the application benefits for each gate can be quite different.
Inlet & Outlet Shape
Gate Size
Alterations can be made to both the Orifice Gate and Roller Gate to build custom gate sizes. This can impact the blade’s travel distance, stack-up height, and many other variables of gate construction. Consult Vortex’s application team to discuss modifications that may/may not be made to accommodate your installation requirements.
Conveyance Type
The Roller Gate should only be used in gravity flow applications. If a system has pneumatic processes or differential air pressures within the system at any point, often times, a Roller Gate should not be considered as an option. However, do note that even though the Roller Gate is considered a "gravity-type" gate, it is commonly used in dust collection systems.
Depending on gate size, the Orifice Gate is designed to seal against pressures up to 15 psig (1 barg). It can be used in both positive pressure and vacuum systems (dilute or lean phase).
Contact us to discuss other gate options for higher pressure pneumatic conveying, such as the Vortex® Heavy Duty Pressure Valve™ (HDPV2) and the Vortex® Titan Pressure Valve™ (TPV).
Stack-Up Height & Ease of Integration within a System
While both gates are benefited by their narrow profiles, the Orifice Gate can be a better option in applications where head space is limited.
Both gates can be altered to match up with any shape of ductwork by fitting the inlet and/or outlet with square-to-round or round-to-square transition pieces or tube stubs. While this customization does add to a gate’s overall height, it allows the gate to be easily integrated within most new and pre-existing footprints.
Materials Handled
Because material characteristics can vary by application, it is best to consult with industry experts to determine which gate is most suitable for use in your specific application prior to making a final decision. Vortex’s technical application team has over 300 years of combined experience in dry bulk material handling to assist you.
Cost Considerations
When directly comparing standard models of the Orifice Gate and the Roller Gate, in general, the Roller Gate is considered to be a “lower cost” valve. As implied above, this consideration must only be taken into account if stack-up height is available and conveyance type is agreeable to your application.
Influencers of Cost:
Several variables can influence the modifications necessary to construct a slide gate built for purpose. Among the most common variables are:
Construction Material Options
Depending on handled material characteristics, Vortex utilizes special construction materials to build valves for their specific application. Such modifications are especially important for materials that are:
- Food grade (require no contamination & frequent wash-down)
- Abrasive
- Corrosive
For food grade applications, Vortex products are constructed using metals and polymers which are compliant with USDA and EU regulations. When handling corrosive materials, Vortex products are constructed from various grades of stainless steel to provide longevity through corrosion resistance.
Climate & Environment
The slide gate’s environment can impact what construction materials are to be used. For example, the seals used for slide gates installed indoors are different from those used to seal slide gates installed outdoors. Climate and surrounding environment can also impact the choice of actuator used to energize the valve.
Handled Material Temperatures
Materials selected for gate construction can also be influenced by the temperature of handled materials as they pass through the valve. For example, standard construction materials can be used if handled materials are at ambient temperatures. But if handled materials are heated beyond a threshold of 180°F (82°C), modifications must be made in the gate’s construction. The Orifice Gate and Roller Gate can be constructed to handle material temperatures up to 400°F (204°C). Contact us to discuss options for higher temperature material handling applications.
Choice of Actuator
Vortex offers many options for actuating a slide gate. For the Orifice Gate and Roller Gate, manual actuation options include:
- Hand crank
- Hand wheel
- Chain wheel
If manual actuation is preferred, the Vortex® Hand Slide Gate™ may be an additional option, depending on application.
Other actuation options include:
- Air cylinder actuator
- Electric actuator
- Hydraulic actuator
These actuator types can be complemented by accessories to provide additional benefits, such as blade position indication.
Blade Type
The Orifice Gate features a rectangular sliding blade with a machined hole that “shears” through the material flow stream. The Roller Gate has a full rectangular sliding blade that glides in and out of the material flow stream.
End Seal Design
The Roller Gate is similar to traditional slide gate designs in that it closes directly against the gate’s body, into an end seal. A deflector at the end seal prevents materials from packing into it. Oppositely, the Orifice Gate’s sliding blade actuates into a recessed area. Thus, it does not have a true end seal.
Wear-Compensating Seals
Both the Orifice Gate and Roller Gate were designed with unique wear-compensating features to maintain a positive seal over time.
The Orifice Gate’s seal plates are constructed from hard polymer and are “live-loaded” with compressed rubber backing. This ensures that as the polymer experiences frictional wear from many cycles over time, the rubber load seals continuously force the seal plates against the sliding blade. In doing so, the gate is able to self-maintain its dust-tight seal without frequent maintenance intervention.
The Roller Gate's seals, rollers and retainers are constructed from hard polymer and durable metals. A benefit of the Roller Gate's sealing design is there is no metal-on-metal contact. This is preferred in many applications to prevent metal fragment contamination.
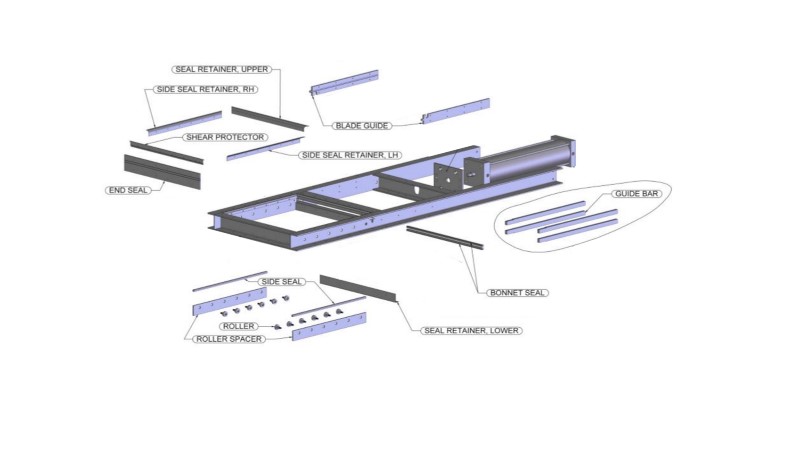
Designed to yield the same benefits as the Orifice Gate’s seal plates, the Roller Gate’s bonnet seals and side seals are also constructed from hard polymer and live-loaded using compressed rubber backing.
Roller Gate – Wear-Compensating Bonnet Seal & Side Seals
Self-Cleaning Seals
On the closing stroke, the Orifice Gate’s machined orifice is actuated beyond the inlet and into a recessed area. In that area, trace amounts of material are “trapped” between the machined orifice and that gate’s seal plates. On each opening stroke, those materials are pulled back out of the recessed area to fall away into the process line below. This design prevents material bridging or packing inside the gate’s body.
Each time the Roller Gate closes, any residual materials remaining in the gate’s side seals are cleared by the blade and forced to fall away into the process line below.
On each opening stroke, the Roller Gate’s bonnet seals act as a squeegee to wipe materials and dusts from both the top and bottom of the blade. This forces any materials remaining on the blade to fall away into the process line below, rather than migrating into the bonnet area.
Maintenance-Friendly Features
To prolong the service life of a piece of equipment, all Vortex products are designed for ease of maintenance and are built with several replaceable mechanisms. For Vortex slide gates, replaceable parts include:
- Air cylinder actuator
- Magnetic reed switches
- Clevis
- Internal seals & shim
- Blade
...among others.
If a slide gate is maintained and operated as recommended, these mechanisms should be the only wear parts. In many cases, this maintenance-friendly design has allowed Vortex slide gates to remain in service for many years – and sometimes, even decades.
At the front of the valve, the Orifice gate features three weep holes:
If material dusts begin to escape through the weep holes, it indicates the seal plates have partially worn and the compression load has lessened, causing the seal plates to no longer be forced against the sliding blade as they should be. In this instance, maintenance must be performed to restore the gate’s dust-tight seal.
To do so, maintenance technicians can utilize the Orifice Gate’s shimming system. Unlike traditional slide gates, which require additional replacement parts be kept on-hand for maintenance, the Orifice Gate calls for removal of shim to perform seal maintenance. By simply loosening the nuts along the lateral aspects of the gate, shim(s) can be removed and the nuts re-tightened to restore the compression load between the blade and seal plates. This process can be performed while the gate remains in-line, and can be repeated many times until most of the shim is removed and the seal plates have worn significantly, at which point the seal plates and shim must be replaced.
The Roller Gate features a perforated bonnet cover at the back of the valve to indicate dusting and seal wear:
If material dusts become present in the gate’s bonnet, this is an indication that the gate’s bonnet seal has lost its compression load and must be replaced.
Along the lateral aspect of the gate are two bonnet seal access doors that are removable using only simple tools. Once the doors are removed, new upper and lower bonnet seals can be driven into the port while the worn seals are simultaneously ejected out the other side.
After many actuations over time, frictional wear between the Roller Gate’s sliding blade and the gate’s hard polymer side seals may also lessen its sealing effectiveness across the blade. Rather than removing the gate from service to replace its side seals each time, the Roller Gate features CAM-adjustable rollers. Using only simple tools, the rollers can be rotated upward to “lift” the blade back into position and restore the compression between the blade and side seals.
Like the Orifice Gate, these maintenance processes can be performed while the Roller Gate remains in-line.
How Should the Gate be Installed: Vertically or Horizontally?
Although the Roller Gate can be installed vertically or horizontally, most likely, it will be installed horizontally because of its application in gravity flow processes.
More often, the Orifice Gate will be installed either vertically or horizontally, depending on application. For instance, if plastic materials are being pneumatically conveyed from one side of a building to another, the convey line will likely run horizontally, in which case the Orifice Gate would be mounted vertically. Alternatively, if the Orifice Gate is being used in a gravity flow application or in an application where materials are being conveyed upward by pressure or vacuum, it will be mounted horizontally.
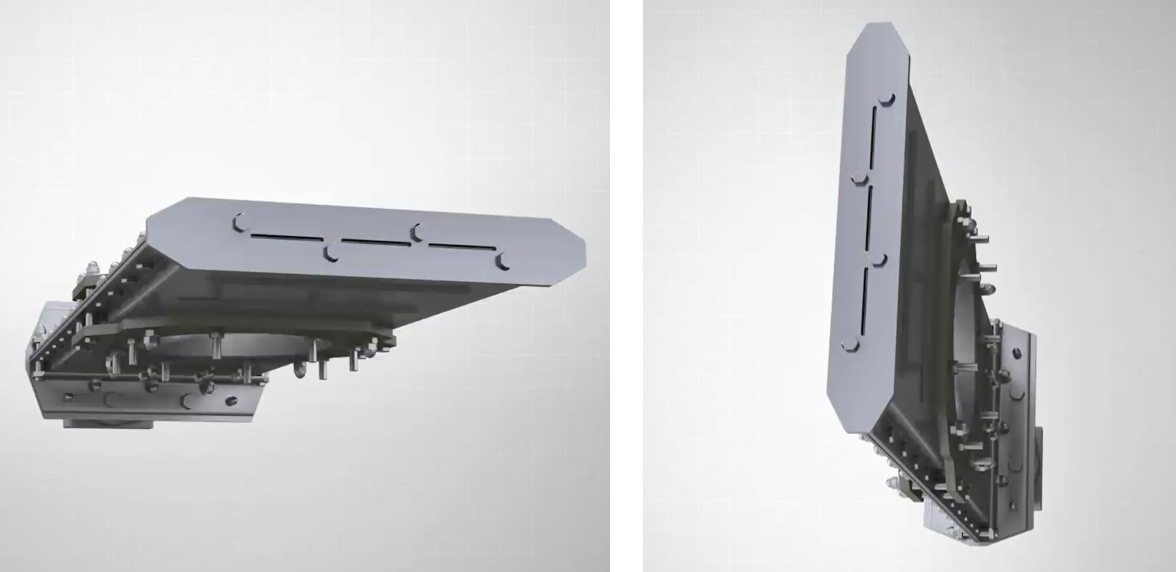
Special Service Inlet
By design, a Special Service Inlet acts as a funnel to direct material flow through the center of the gate. Keep in mind, a Special Service Inlet should only be used if a gate is installed horizontally, and should not be used in pneumatic conveying applications.
The primary purpose of a Special Service Inlet is to provide a better seal by creating a void between materials, the blade, and the gate’s seals. A Special Service Inlet creates a slight "dead pocket" that allows materials remaining at the leading edge of the blade to fall away into the process line below prior to the blade entering its end seal. This hinders materials from packing in the gate’s end seal.
For the Roller Gate, a Special Service Inlet also protects the gate’s rollers from blast abrasion as materials flow through the valve.
Employee Safety
The Orifice Gate and Roller Gate confine materials within the process line to prevent material leakage and dusting to atmosphere. Especially for explosive or otherwise hazardous dry materials, this design benefits occupational safety and health initiatives by ensuring a safe and clean working environment. By preventing material leakage to atmosphere, manufacturing facilities can also be assured they are not a hazard to nearby schools, neighborhoods, waterways and ecosystems.
Both gates are designed with no pinch points or exposed moving parts, allowing for safe employee operations.
Both the Orifice Gate and Roller Gate can be rated to ATEX Zone 20 internal and Zone 21 external, making them suitable for use in almost any explosive or potentially hazardous environment.
Other Considerations:
Ability to Handle Sticky Materials
When handling potentially sticky materials, complications can arise if proper slide gate designs are not sourced for purpose. With frequent actuations, frictional heat is created between the sliding blade and its seals. When sticky materials are subjected to frictional heat, they can react and become adhesive in nature. This can cause significant blade actuation issues and almost constant need for maintenance.
Ability to Seal Pressures Below
Though Orifice Gates are successful in sealing against differential pressures, in applications where pressures are originating near the gate’s outlet, an Orifice Gate may not be the most suitable solution. The most common example of such an application is when slide gates are applied with airlocks in pneumatic conveying applications.
Material Flow Control
As a standard, the Orifice Gate and Roller Gate are designed to actuate into a full open and full close position. If an application requires metering of material, both the Orifice Gate and the Roller Gate can be equipped with one of Vortex’s many material flow control assemblies.
Which Gate Should I Choose?
While the Orifice Gate and Roller Gate are both excellent options for handling most powdered, pelletized or granular dry materials, it is critical to first consult with your valve manufacturer prior to making a decision. With so many variables to consider – and countless more left unmentioned – it is of utmost importance to seek advice and gather knowledge from industry experts to ensure your selection is truly the best solution for its application.
With more than 300 years of combined experience in the dry bulk solids industry, clients can be assured Vortex application engineers will listen to your needs and rely on in-depth knowledge of dry solids to develop the right solution for even the most demanding applications.
For more information on the Orifice Gate or Roller Gate, or to discuss your material handling needs, please contact us.
Enjoy these features but handling abrasive, heavy-duty materials? Check out the Vortex® Titan Slide Gate™ (TSG).