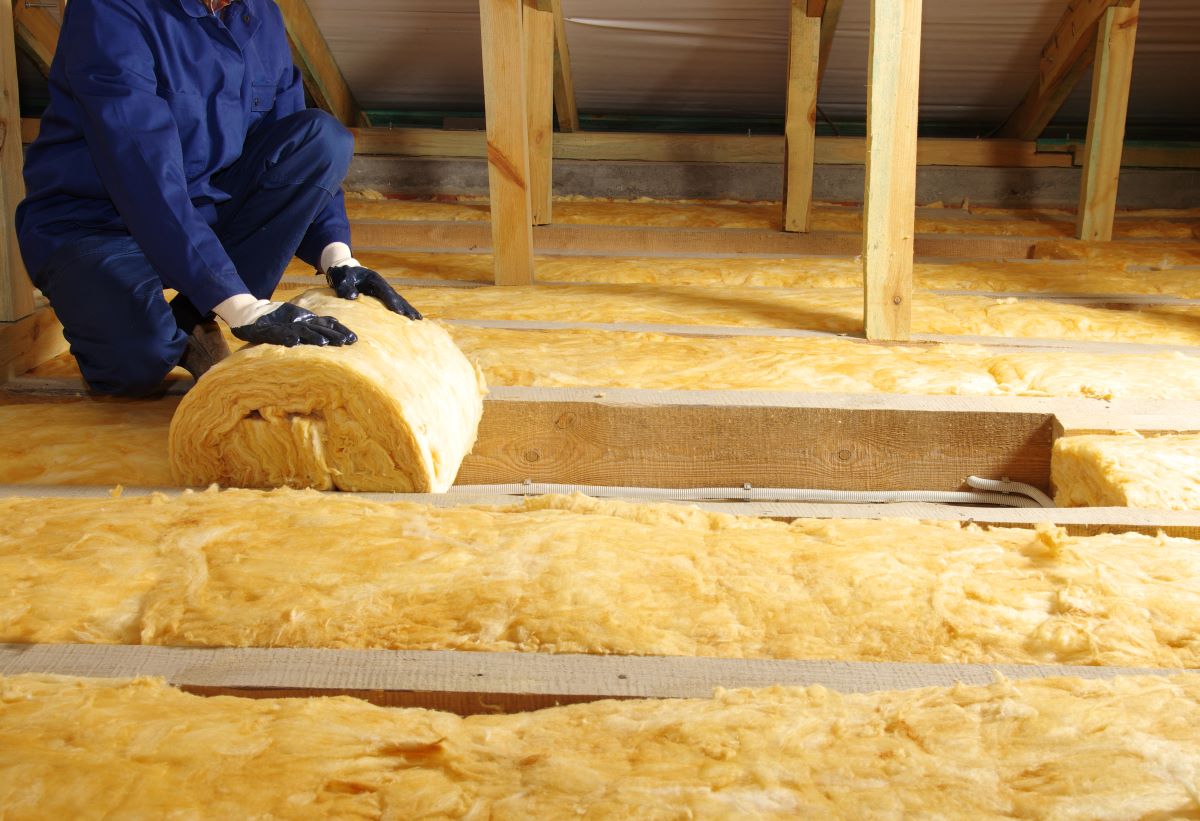
Client:
Quantity:
Size:
Application:
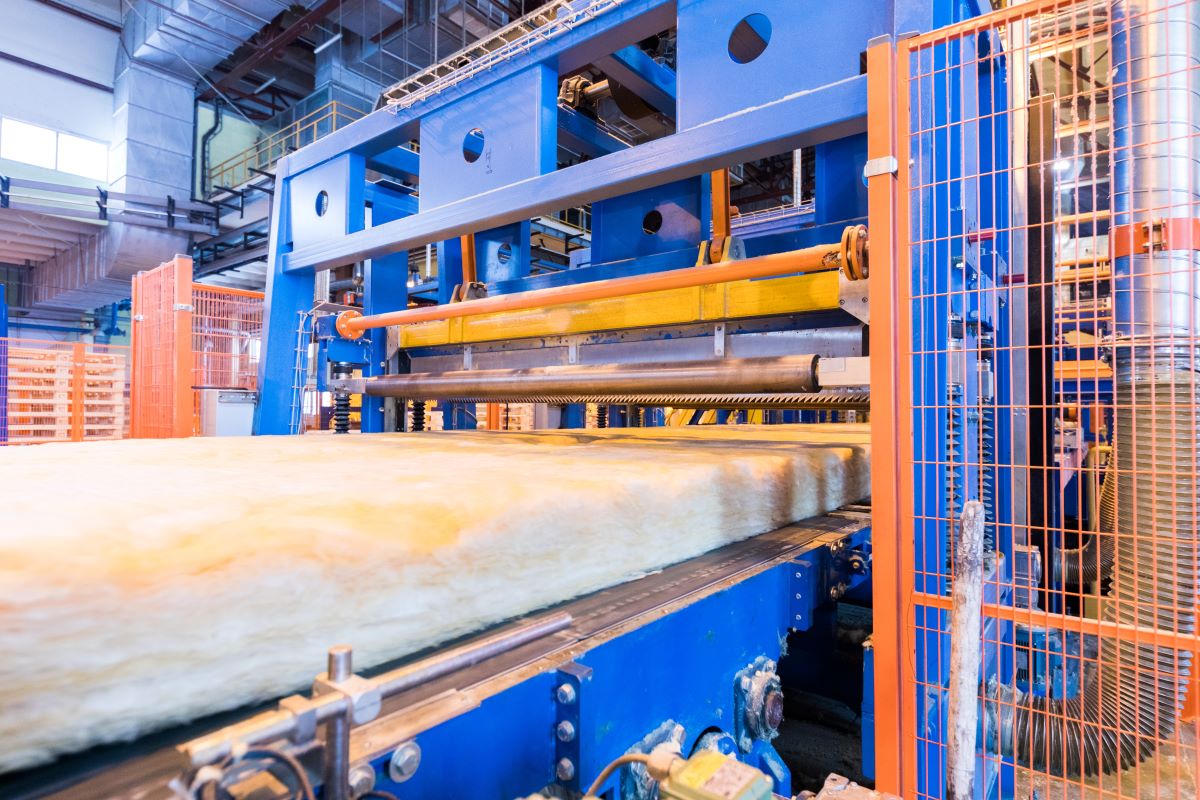
What Is Fiberglass and How Is It Made?
Fiberglass insulation, a prevalent insulation material in the construction industry, is renowned for its superior thermal performance, fire resistance, and sound absorption properties. It is primarily composed of tiny glass fibers and is designed to minimize heat transfer. The process of creating fiberglass insulation is both intricate and fascinating, reflecting a blend of science, technology, and industry expertise.
The production of fiberglass insulation begins with sand and recycled glass, often sourced from post-consumer glass products. These components are melted together in a furnace at extremely high temperatures, usually exceeding 2,700 degrees Fahrenheit. This melting process transforms the raw materials into a liquid state, allowing them to be formed into glass.
Once the glass is molten, it is extruded through tiny holes in a spinning plate, a process known as "fiberizing." As the liquid glass is forced through these openings, it is simultaneously blown with high-velocity air or steam, which cools and shapes the glass into thin strands or fibers.
After fiberizing, a binder, typically made from formaldehyde, urea, or phenol, is applied to the fibers to help them stick together. This mixture is then heated in an oven, causing the binder to cure and harden, which solidifies the fiberglass material.
The resulting product is then cut into manageable batts or rolls, or it may be further processed into loose-fill insulation. Customization options are available depending on the specific needs of a project, such as higher density for improved soundproofing or specialized facings for additional moisture control.
Throughout this manufacturing process, quality control is paramount, ensuring that the final product meets stringent industry standards for safety, durability, and performance. In addition, companies in this field are continually seeking innovative ways to improve the efficiency and sustainability of their operations, reflecting a strong commitment to both customers and the environment.
Handling the Fibers
The Vortex Roller Gate offers a comprehensive solution for managing fiberglass fibers, combining versatility, durability, self-cleaning capabilities, and customization to meet the specific needs of the fiberglass insulation industry. These benefits, coupled with the gate's commitment to safety make it an ideal choice for any company seeking to enhance its fiberglass handling processes.
The Vortex Roller Gate is expertly designed to offer numerous benefits when handling materials such as fiberglass fibers. Here are some of the key advantages:
- Versatility: The gate can handle a wide array of materials, including non-abrasive to moderately abrasive powders, pellets, granules, and dusts, making it suitable for fiberglass insulation production. It can even be modified to manage sticky and/or corrosive materials.
- Durability: Constructed from specialized metals and polymers like 6061-T6 aluminum, and 304 or 316L stainless steel, the Vortex Roller Gate ensures application-specific durability. Its hard polymer seals provide greater wear resistance and a longer service life.
- Self-Cleaning: The gate is designed to mechanically self-clean its seals with each actuation. This feature minimizes maintenance efforts and downtime, enhancing productivity in the fiberglass insulation manufacturing process.
- Protection from Contamination: With no metal-on-metal contact, the risk of galling and foreign metal fragment contamination is eliminated. This is crucial in maintaining the quality of the fiberglass fibers.
- Customization: The Roller Gate offers custom sizes and flange options to match any combination of gate stroke or width, allowing it to seamlessly integrate into existing operations.
- In-line Maintenance: Features like cam-adjustable rollers, replaceable parts, and access slots for easy bonnet seal replacement all contribute to convenient in-line maintenance, reducing downtime and ensuring continuous operation.
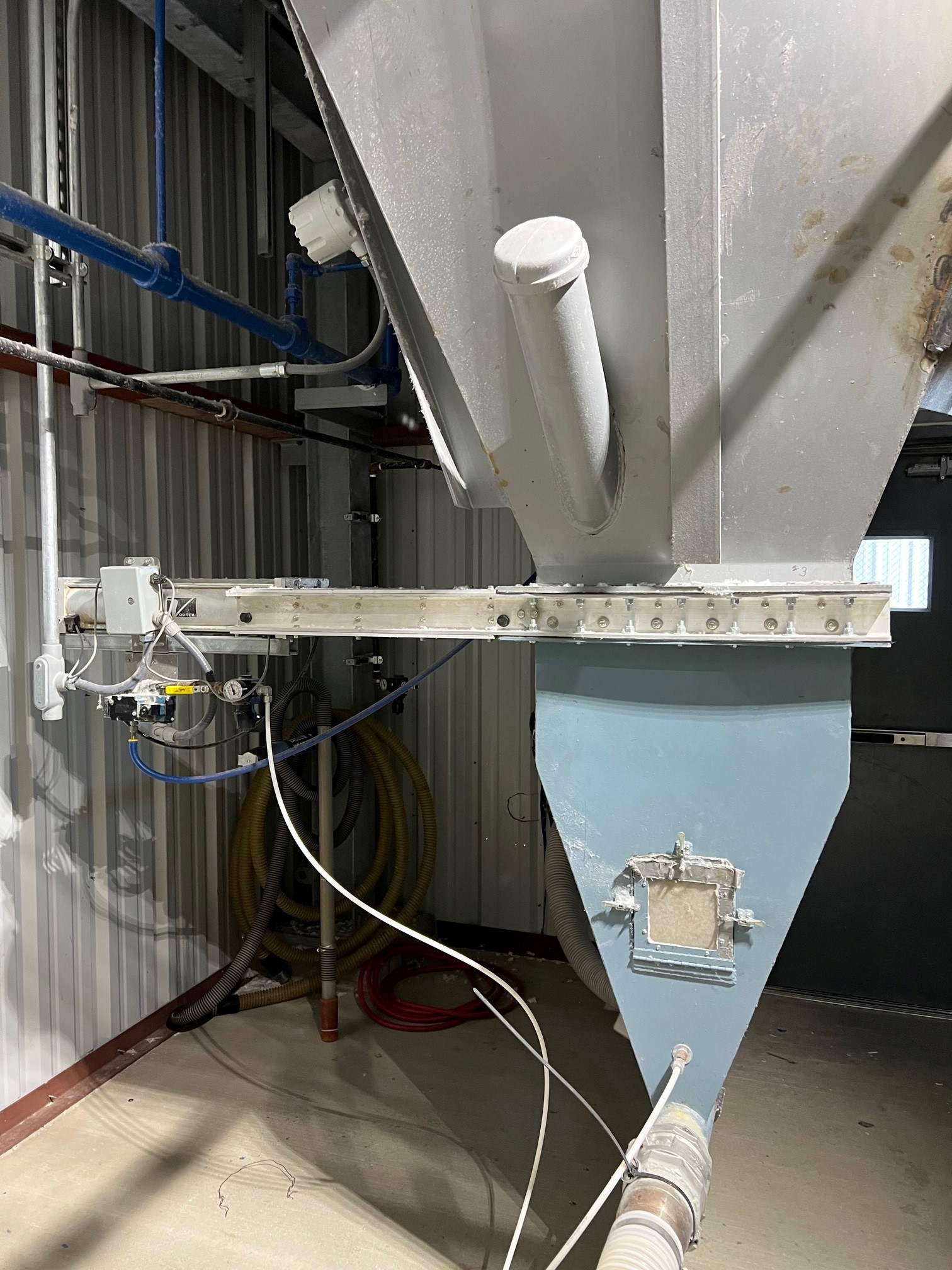
Model: SA22V1-SB
Vortex Model No. SA22V1-SB, 22" Roller Gate Valve.
- Valve body is 6061-T6 aluminum with a 304 stainless steel blade and seal retainers.
- Material contact is 304 stainless steel and polymer.
- Milled access slots in side frame allows removal and replacement of bonnet seals while the gate valve remains in service.
- Valve body is modified to accept proximity switches (plugged if indication switches are not utilized).
- Oversized double acting air cylinder actuator equipped with a magno-piston for use with magnetic reed position indication switches.
- Valve is rated for 180˚F(82˚C) maximum continuous service.
- PET side seals and upper and lower bonnet seals are live loaded and silicone rubber backed.
- Valve also includes cam-adjustable slide rollers and PET roller spacers.
- End seal and bonnet blade guides are UHMW-PE.
- (SB) - Standard bonnet covers are replaced with solid aluminum covers gasketed with SBR foam (silicone sponge when used in conjunction with HT4 modification). A 1/4" NPT purge tap is added to upper bonnet cover for use in conjunction with an air purge assembly (sold separately).