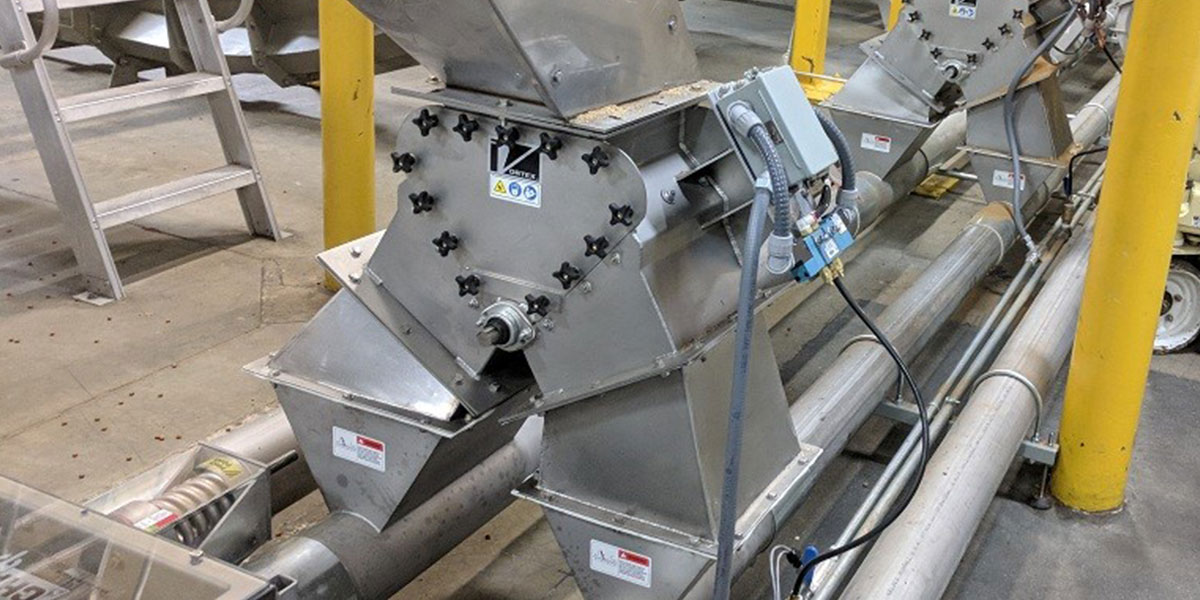
Client:
Quantity:
Size:
Application:
As published in International Petfood Magazine
When sourcing dry bulk handling equipment in the manufacturing of petfood and its ingredients, several key considerations must be taken into account. Sanitary modifications, interior accessibility, wear compensation, in-line maintenance and dust tight sealing capabilities are all factors that should be evaluated when purchasing these components.
Products commonly used in the production of pet food include slide gates, diverter valves, air locks, screw conveyors, hoppers, screeners and magnets. Manufacturers of these products continue to make strides in ensuring long service life and the ability to prevent cross contamination and spoilage.
Ingredients most used in the production of petfood are grains, meat byproducts, fish, and varying organic materials. These ingredients can be challenging to handle due to various factors including their sticky nature and concerns of cross contamination.
Cleanliness is an important factor
As the industry moves towards creating natural products with even more organic ingredients, cleanliness is an important factor. To keep the facility clean, equipment must be easily accessed for frequent cleaning.
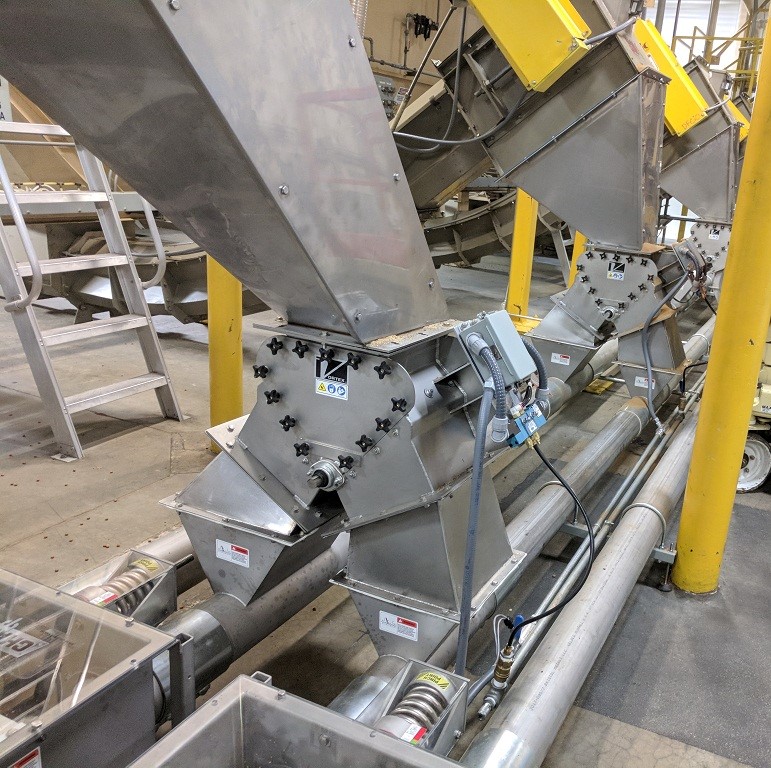
The use of stainless steel for all material contact areas and other materials deemed acceptable by global health and safety experts helps to ensure cleanliness and safety of the product.
Electropolishing of material contact areas and continuous welds are also used to ensure sanitation and safety. These processes lessen the surface rigidity of raw stainless steel. In doing so, material particles and dusts have less opportunity to collect in ridges along the steel’s surface. These methods further reduce the likelihood of in-line contamination and spoilage.
When handling kibble, one challenge pet food manufacturers face is that traditional pneumatic conveying methods can cause the kibble to turn to powder. To avoid breakage, gravity conveying is preferred.
Gravity conveying also helps prevent infestation in sanitary applications. In addition to breakage, product loss is also a concern. To combat loss of product, manufacturers have moved towards horizontal and enclosed conveying methods.
A critical component of equipment used by petfood manufacturers is the implementation of sealing technology. Dust tight gates and diverters reduce airborne fugitive dust that can create unproductive working conditions and safety hazards from dust accumulation. They also reduce housekeeping costs that can be very expensive over the course of a year. A cleaner facility runs more efficiently and provides better working conditions for employees.
Case Study: Vortex Seal Tite diverters handling pet food kibble
A global manufacturer of petfood sourced four Vortex Seal Tite Diverters to divert petfood kibble in their process from a feeder into one of two-disc conveyors. The disc conveyors are used to transport kibble into the packaging line.
The Seal Tite Diverter features a removable access door that allows inspection, maintenance and repairs to be performed without removing the diverter from service. Featuring a two-way diverting design, its body, blade and material contact areas are all constructed from 304 stainless steel, whilst this product also features removable parts.
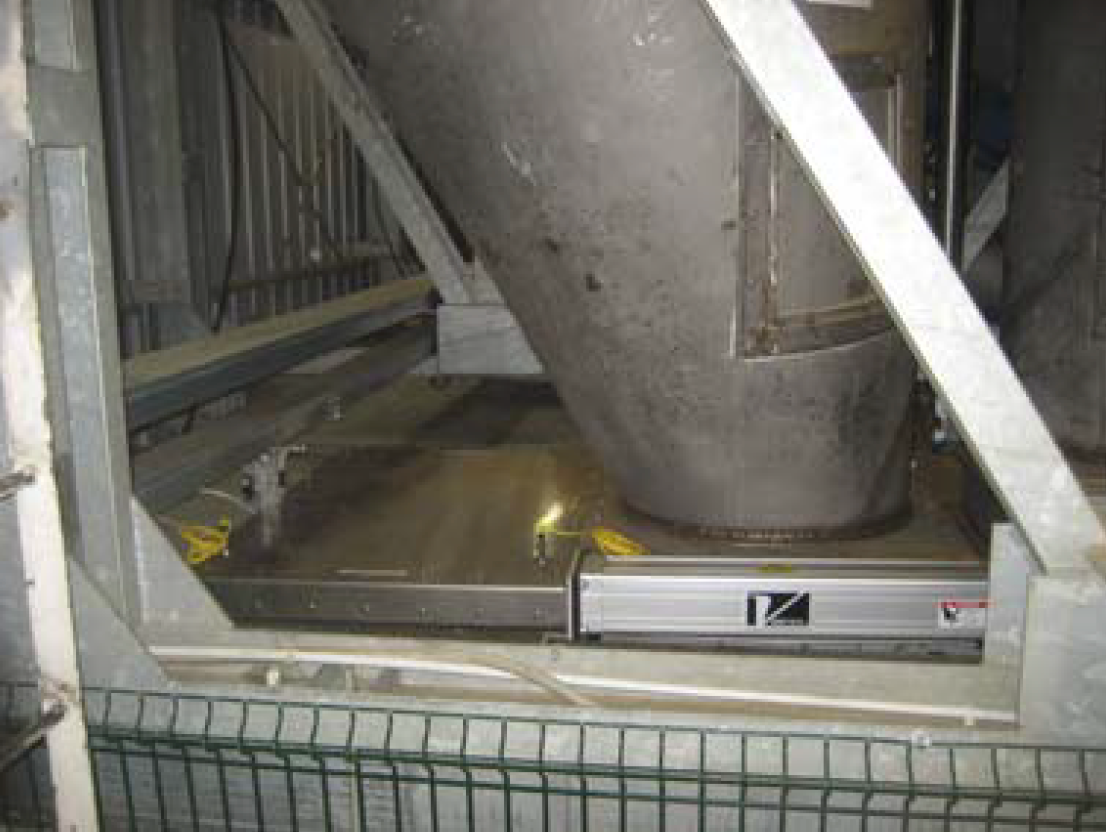
These features are beneficial for return-on-investment purposes because they allow for the replacement of worn parts, rather than full diverter replacement.
Case Study: Dual Cylinder Vortex Roller Gate handling petfood
An Italian petfood manufacturer sourced eight Vortex Dual Cylinder Roller Gates to assist in the gravity flow discharge of partially processed feed meal from a storage bin to a conveyor. The client’s main concern was to eliminate weekly maintenance downtime which often exhausted an entire day’s worth of labor.
These 750mm (30”) gates are constructed of 304 stainless steel and with blank flanges that were drilled on site to match the customer’s existing bolt pattern. Other modifications included a special service inlet and hardened steel rollers (-HS) to accommodate the abrasiveness of the material and the humidity in the environment. For position indication, the customer opted for bonnet mounted proximity switches.
Case Study: Multiport Diverters handling pet food additives
This petfood manufacturer expressed a need to redesign a process within their system to achieve a reduced footprint. The client’s main concerns were stack-up height, creating a minimal footprint with no line extensions (so that multiple additives can be handled in a common process), and inspection/maintenance features.
Each of the two multiport diverters were assembled using one two-way Seal Tite Diverter with a symmetrical (A-style) design and square outlet transition chutes constructed from carbon steel (the purpose of the transition chutes is to extend the diverter's outlet legs, to make clearance for the three-way diverters below) and two three-way Seal Tite Diverters.
Each of the diverters are 205mm (8”) and feature bodies and flapper blades constructed from carbon steel. Material contact areas are constructed from carbon steel, polymer and white Buna-N nitrile rubber.
The support frame is constructed from painted carbon steel. The frame’s purpose is to support the multi-port structure and assist installation as a cohesive unit.
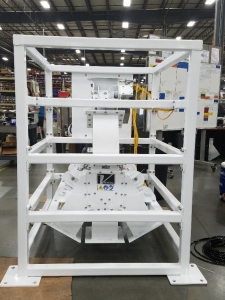
As a safeguard in case of an upset condition or if maintenance is required downstream, the client also required two Vortex Maintenance Gates, to be installed above both airlocks.
Petfood can be a messy endeavour
The manufacturing of petfood can be a messy endeavour. When properly developed systems and components are sourced, the process can be clean, quick, safe and cost effective. These improvements extend service life, prevent cross contamination and spoilage while reducing life cycle and housekeeping costs.
For more than 45 years, Vortex Global has provided quality slide gates, diverters, iris valves and loadout equipment designed specifically for handling dry bulk solids in gravity, vacuum, dilute, or dense phase applications. The company’s products can be customised for specific applications or special installations.