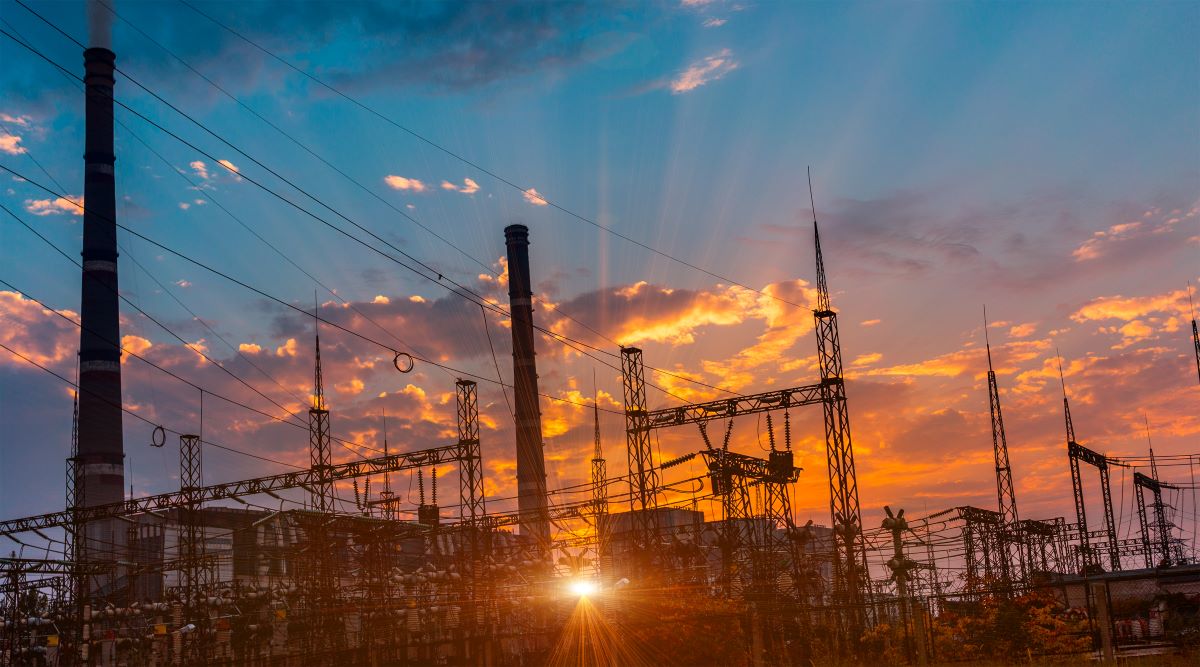
Client:
Quantity:
Size:
Application:
The Current Backbone of Power and Economy
Coal holds a significant place in Indonesia's energy sector and economy. As of 2022, coal accounted for 43% of the country's electricity generation, marking a record high. This is largely due to Indonesia's abundant coal reserves, which are estimated at nearly 39 billion tonnes.
The coal industry is an important contributor to the Indonesian economy, providing a source of foreign currency, state revenues, and employment.
Indonesia also stands as one of the world's largest producers and exporters of coal, further underscoring the industry's importance to the national economy. In fact, coal has become such a central part of Indonesia's power plans that the government expects it to continue playing a significant role in the decades to come.
However, it's worth noting that while coal remains crucial for Indonesia, the country is also gradually transitioning towards renewable energy sources. This shift is aimed at balancing the need for energy security with the pressing demands of environmental sustainability and public health.
Pivoting Chutes Made to Perform
In the coal handling process of an Indonesian power plant, the end user requires a maximum flow rate of 1800 metric tons per hour, with a bulk density of 641 kg/m3. To address the current issue of failing flap type diverters in the gravity flow system, two pivoting chute diverters have been recommended as replacements.
The Vortex Pivoting Chute Diverter is an exceptional tool for managing coal. Crafted with meticulous precision, this diverter is designed to divert heavy-duty and abrasive dry bulk solid materials, such as coal, from one source to multiple destinations. This functionality is critical in gravity-fed applications, where efficient and reliable material flow control is non-negotiable. The introduction of the pivoting chute design has not only improved the flow rate but has also proven to be a better fit for the application. Additionally, the end user has expressed appreciation for the maintenance benefits offered by the pivoting chute diverter solution. Constructed from durable carbon steel, the body of the Pivoting Chute Diverter is built to withstand the rigors of heavy-duty and abrasive materials. Its robustness is further enhanced by replaceable abrasion-resistant wetted parts, which prolong the service life of the diverter and eliminate the need for complete replacement, leading to cost savings. The unique design of the Vortex Pivoting Chute Diverter allows it to be shifted on a flowing column of materials, enhancing the handling efficiency of smaller-sized materials like coal. This ensures smooth and effective operations. In addition, the Pivoting Chute Diverter is compatible with Vortex's material flow control assemblies, offering total flow control to a single destination or split flow to two destinations, providing flexibility based on operational needs. Lastly, the wear and containment bar in the Pivoting Chute Diverter provides dual functionality. It guides materials through the desired outlet while also offering protection against wear and abrasion.
- Vortex Model No.PCEC1000-2CS-45-E21555
- 1000MM 2-way Pivoting Chute Diverter.
- Valve body (non-wetted) is constructed of carbon steel.
- Inlet chute and internal pivoting chute (both replaceable parts) constructed of abrasion resistant steel (minimum 400 BHN).
- Outlet chutes and the bottom portion of the diverter (material contact areas) contain replaceable AR400 liners.
- The interior juncture of the outlet legs includes a wear-resistant, replaceable material containment bar.
- Removable access cover is provided to inspect or maintain diverter without removing it from service.
- Diverter is rated for continuous temperatures up to 400°F (204°C).
- Valve body is designed to accept proximity switches.
- Electric actuator
- Outlets are offset symmetrically from valve centerline
- Outlet legs offset 45° from vertical
- Square inlet and outlets have a drilled flat flange for bolt through connection.
- ENGINEERED SPECIFICATIONS (E21555) – LARGE PIVOTING CHUTE DESIGN. UPPER PORTION OF VALVE IS REMOVABLE TO ALLOW FOR CHUTE REPLACEMENT. CHUTE IS ¾” THICK, REPLACEABLE LINERS ARE ½” THICK. BOTH CONSTRUCTED FROM ABRASION RESISTANT STEEL 400 BHN MIN. POWERED BY A NON-HAZARDOUS AUMA SA 10.2 GS200.3 WITH AC CONTROLS, 400V/3PH/50HZ. MATCHING CUSTOMER PATTERN. LOW PROFILE LAYOUT WITH REDUCED FLOW RATE.
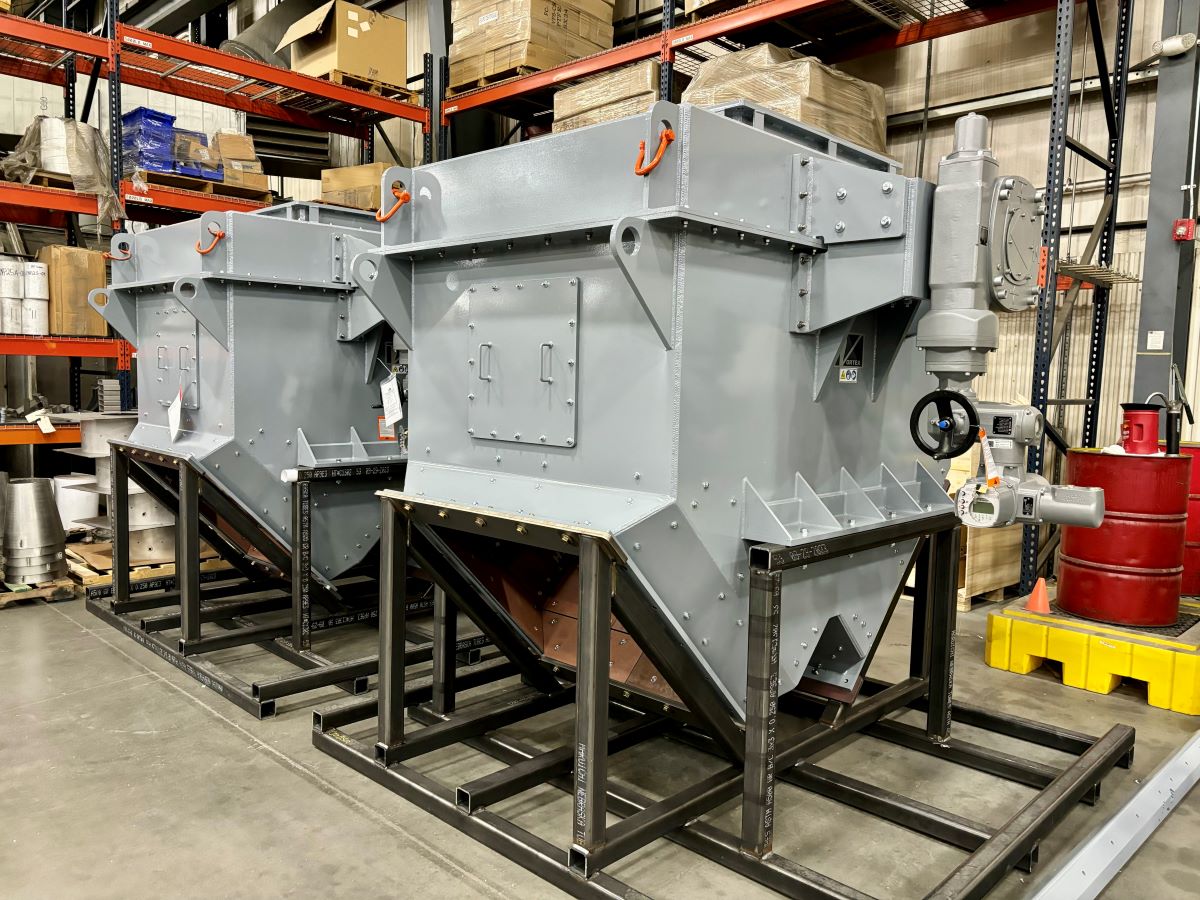
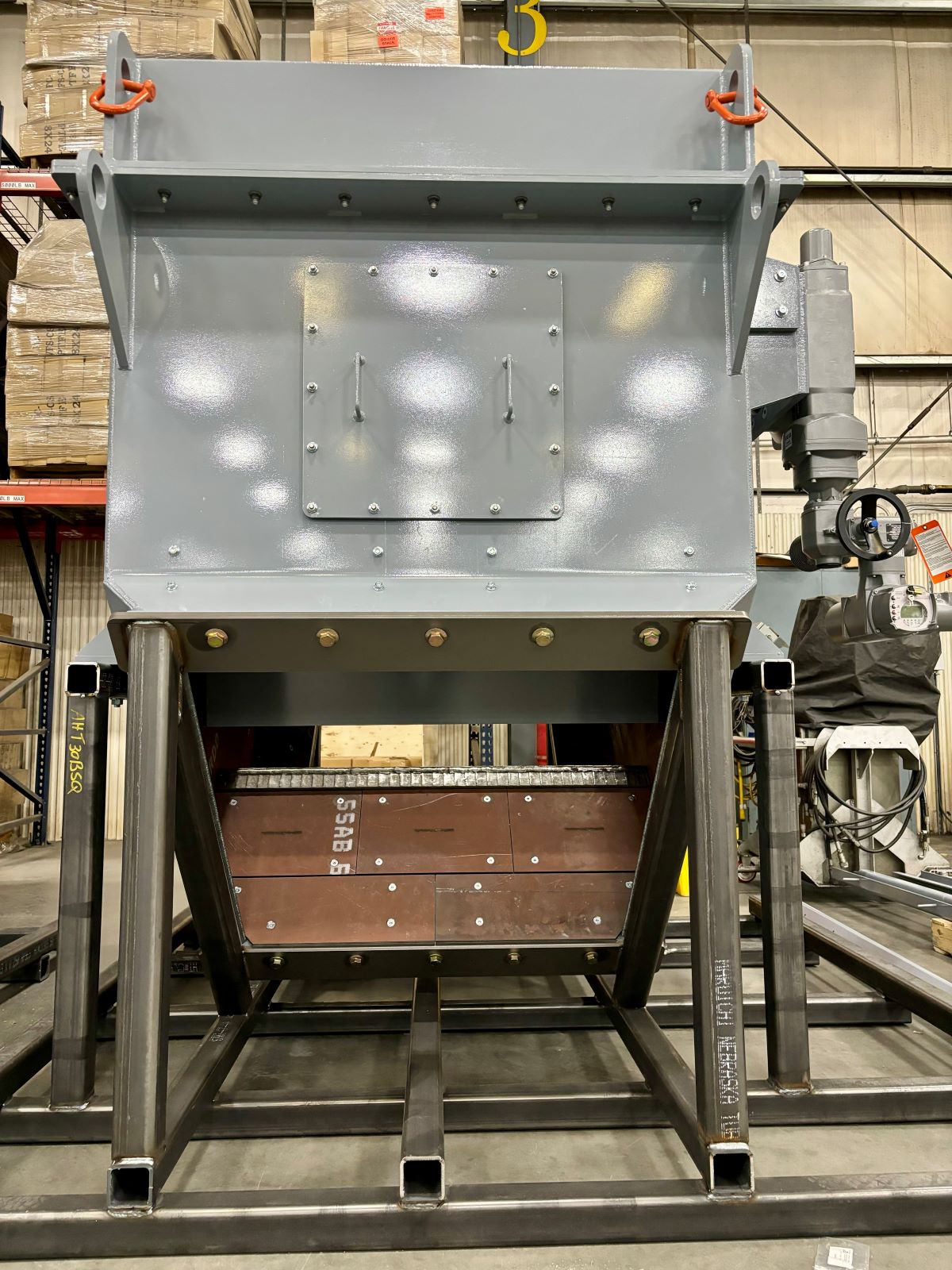
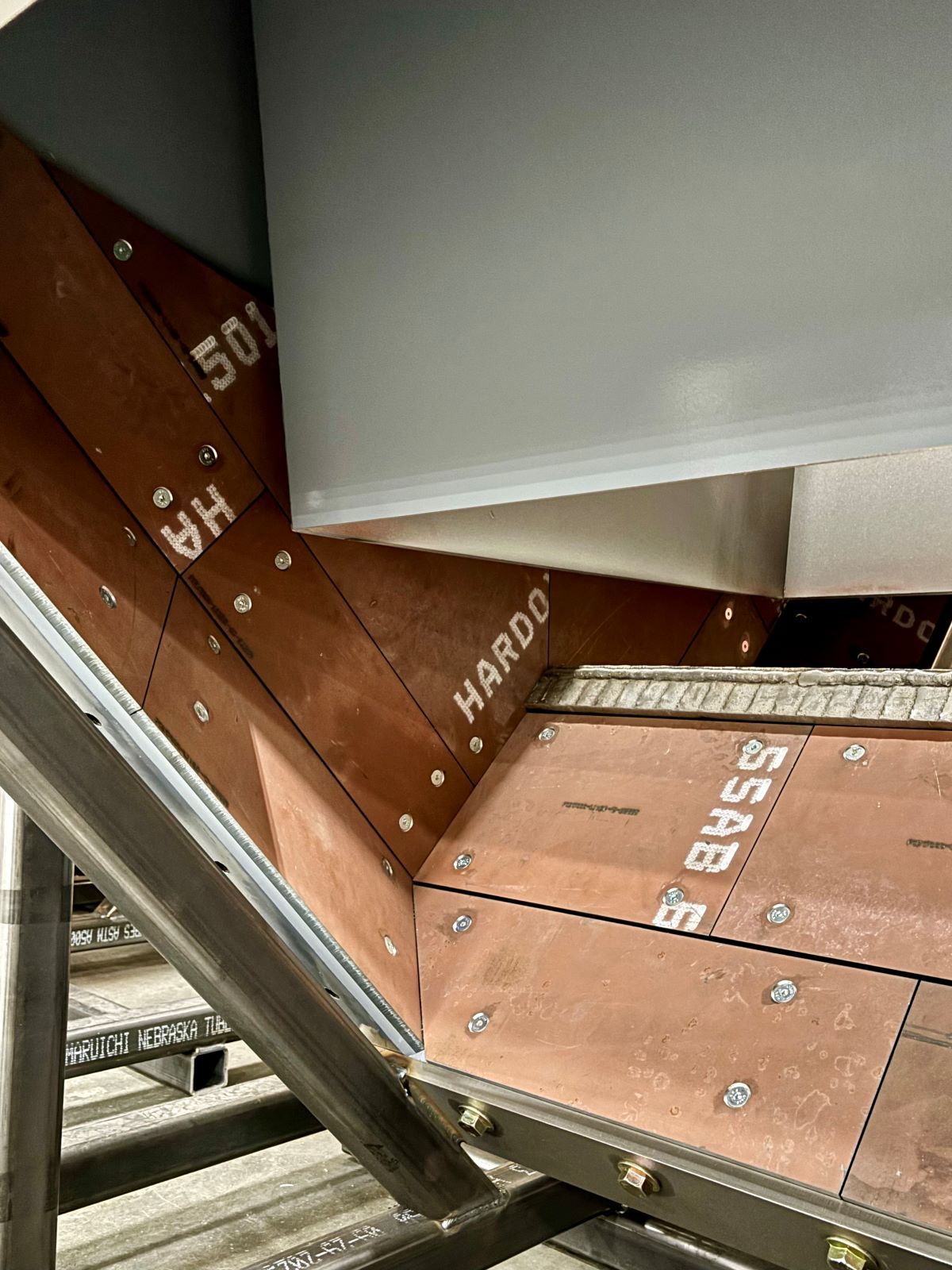
The introduction of the pivoting chute design is anticipated to improve the flow rate and to be a better fit for the application. Additionally, the end user has expressed excitement for the maintenance benefits offered by the pivoting chute diverter solution.
With the implementation of these pivoting chute diverters, this Indonesian power plant will be set to enhance coal handling efficiency and ensure a smoother operations process.