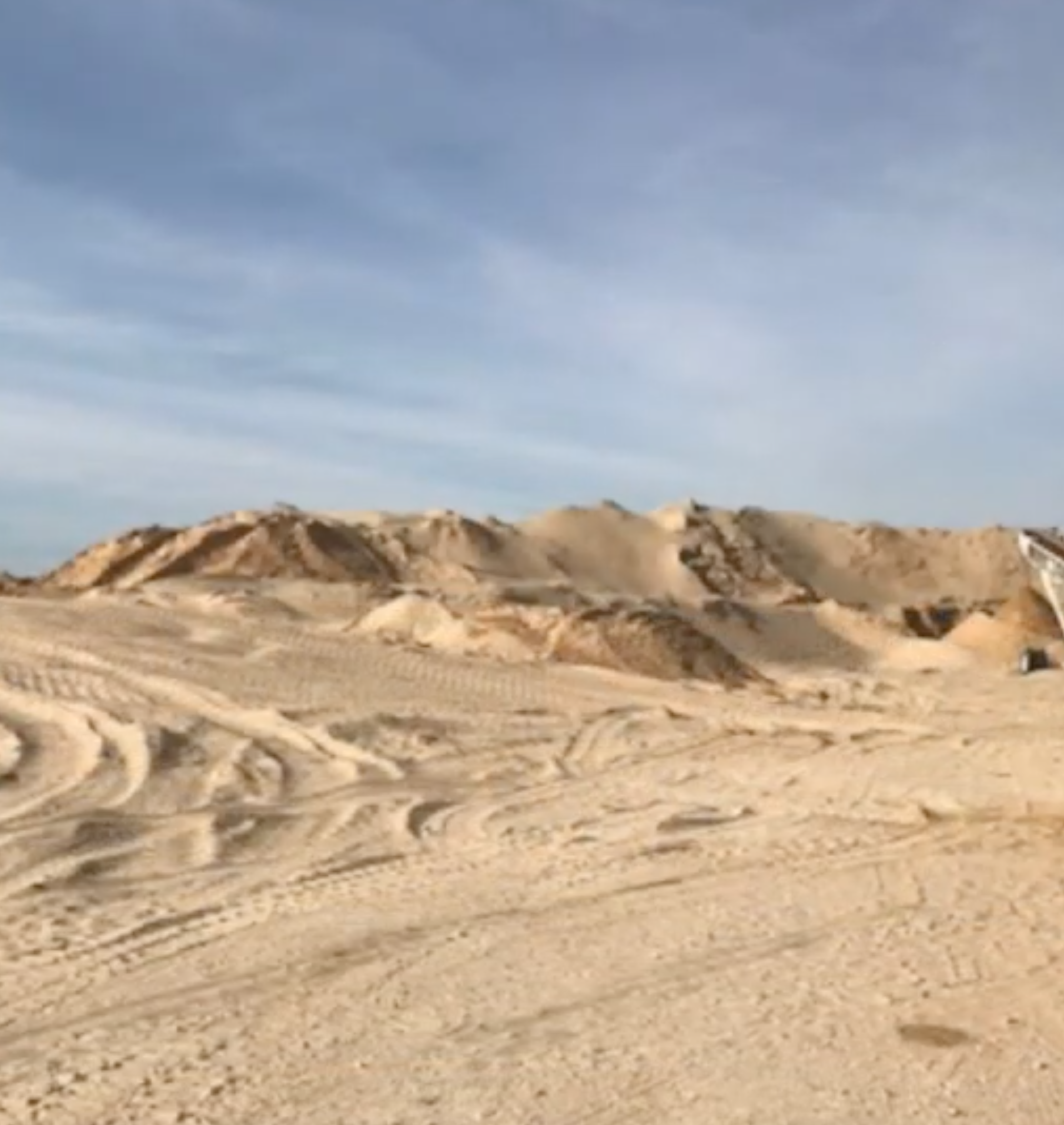
Client:
Quantity:
Size:
Application:
In 2017, Vortex completed a large project with an industrial sand manufacturer to construct a new sand processing facility. As part of this project, the client sought solutions for:
- Diverting sand into screeners, where the sand is sized and then transferred into a series of holding bins.
- Loading sand from each holding bin into enclosed trucks below.
Due to the abrasive properties of industrial sand, this client sought reliable components designed for durability and longevity. Having enjoyed the quality of Vortex components when using them in previous projects, this client opted to source 17 Pivoting Chute Diverters, 9 Titan Lined Diverters (TLDs), 5 Titan Slide Gates (TSGs), 5 Vortex Loading Spouts, and 14 Titan Maintenance Gates (TMGs).
Diverting Sand into Screeners
The Vortex Pivoting Chute Diverters (PCDs) are used to divert sand into screeners. PCDs were selected primarily for their abrasion-resistance, as well as for their accelerated processing speeds and their ability to be shifted “on the fly” when handling fine grades of sand.
Quantity: 17 Vortex Pivoting Chute Diverters
Size: 10 in | 254 mm
Specifications:
- Three-way design.
- Body & material contact areas constructed from 400 BHN abrasion-resistant steel.
- Internal chutes constructed from 400 BHN abrasion-resistant steel.
- Replaceable 400 BHN abrasion-resistant steel liners throughout the diverter’s internal body.
- Outlet legs offset 45° from center.
- Round transition pieces at the diverter’s inlet and outlet legs, constructed with ANSI flanges.
- Lifting lugs provided.
- Air cylinder equipped with a magnetic piston to accommodate magnetic reed switches for chute position indication.

Unique to Vortex diverters, the Pivoting Chute Diverter features a removable access panel that allows inspection and maintenance to be performed while the diverter remains in-line. PCDs also feature replaceable abrasion-resistant liners and removable wetted parts. For return-on-investment purposes, these features are beneficial because they allow for the replacement of worn parts, rather than full diverter replacement.
Unlike traditional flap or bucket diverters, the Vortex Pivoting Chute Diverter features an independent, internal chute that “pivots” between outlet ports. This allows the chute to be smoothly shifted without significant disruption to the material flow path, which reduces chute wear.
To improve processing speeds, the Pivoting Chute Diverter is designed so that it may be fully shifted toward a single outlet port, or partially shifted to split flow toward two destinations. Because material flow will be shared through one chute toward two destinations, flow rates toward each outlet will be diminished, in comparison to typical one-to-one flow rates. However, because two destinations may simultaneously transport materials, overall processing speeds are improved.

For this application, the client requested lifting lugs for each diverter. As pictured below, lifting lugs were machined near the top on each end of the diverter’s internal chute. Because the internal chute is quite heavy, the addition of lifting lugs allows the internal chute to be hooked up to a crane and lifted into/out of the diverter. For employee safety purposes, lifting lugs are beneficial because they avoid physical injury from manually lifting the heavy chute into place.
All in all, the Vortex Pivoting Chute Diverter is specifically designed to provide maximum protection against wear and abrasion, in order to improve life cycle costs.
Note: The Pivoting Chute Diverter is dust-tight to atmosphere. However, it does not feature any internal seals, so dusting and material migration to the opposite leg(s) is possible.
Continue reading about this project:
Part 1 | Part 2 | Part 3 | Part 4