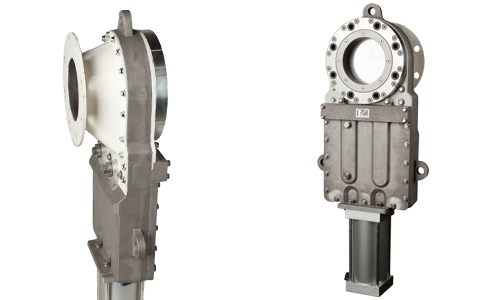
Client:
Quantity:
Size:
Application:
SALINA, KAN., USA – Vortex’s patented HDP Slide Gate has been a proven solution for a wide variety of applications for handling sticky and/or abrasive powders in systems with positive pressures up to 75 psig (5 bar). Since its original release in 2006, the HDP has been utilized for handling cullet, glass, sand, cement, borax, gum base, kaolin clay, and a wide variety of problematic dry bulk solids.
Vortex is pleased to announce the release of the HDPV2, which offers significant enhancements over the original HDP design. New features include a wider bonnet that eliminates a dead pocket where material could potentially build-up. Other design changes include a longer body frame to allow easier inspection and replacement of seals and wear parts while the gate remains in service.
New modifications also include a replaceable nylon insert on the rising clevis, which allows for easy and inexpensive maintenance. The HDPV2’s unique ramp system offers a shimming system that compensates for seal wear over time. The valve’s design incorporates an o-ring seal through the bonnet and utilizes reusable precut gaskets to eliminate material leakage to atmosphere. The air cylinder mount is cast into the frame, which reduces potential areas where leakage could occur.
The patented Vortex HDP Gate has been a proven solution for a wide variety of applications handling sticky and/or abrasive powders in positive pressure systems up to 75 psi | 5 bar. Since the HDP Gate's original release in 2006, it has been utilized for handling cullet, glass, sand, cement, borax, gum base, kaolin clay and a variety of other problematic dry bulk solid materials.
With that, Vortex is pleased to announce the release of its revised HDPV2 Gate design, which offers significant enhancements over the original HDP Gate design. New features include:
- A wider bonnet area, to eliminate a dead pocket where material could potentially build-up.
- A longer body frame, to allow easier inspection, seal replacement and/or wear part replacement while the gate remains in-line.
- A replaceable Nylon insert on the rising clevis, which allows for easy and inexpensive maintenance.
- A unique blade design which "lifts" into an end seat, to prevent leakage of air and materials past the gate or to atmosphere.
- A shimming system to compensate for seal wear over time.
- An O-ring seal and reusable, pre-cut gaskets, to eliminate material leakage to atmosphere.
- An air cylinder mount casted into the body frame, to reduce potential areas where air and material leakage could occur.