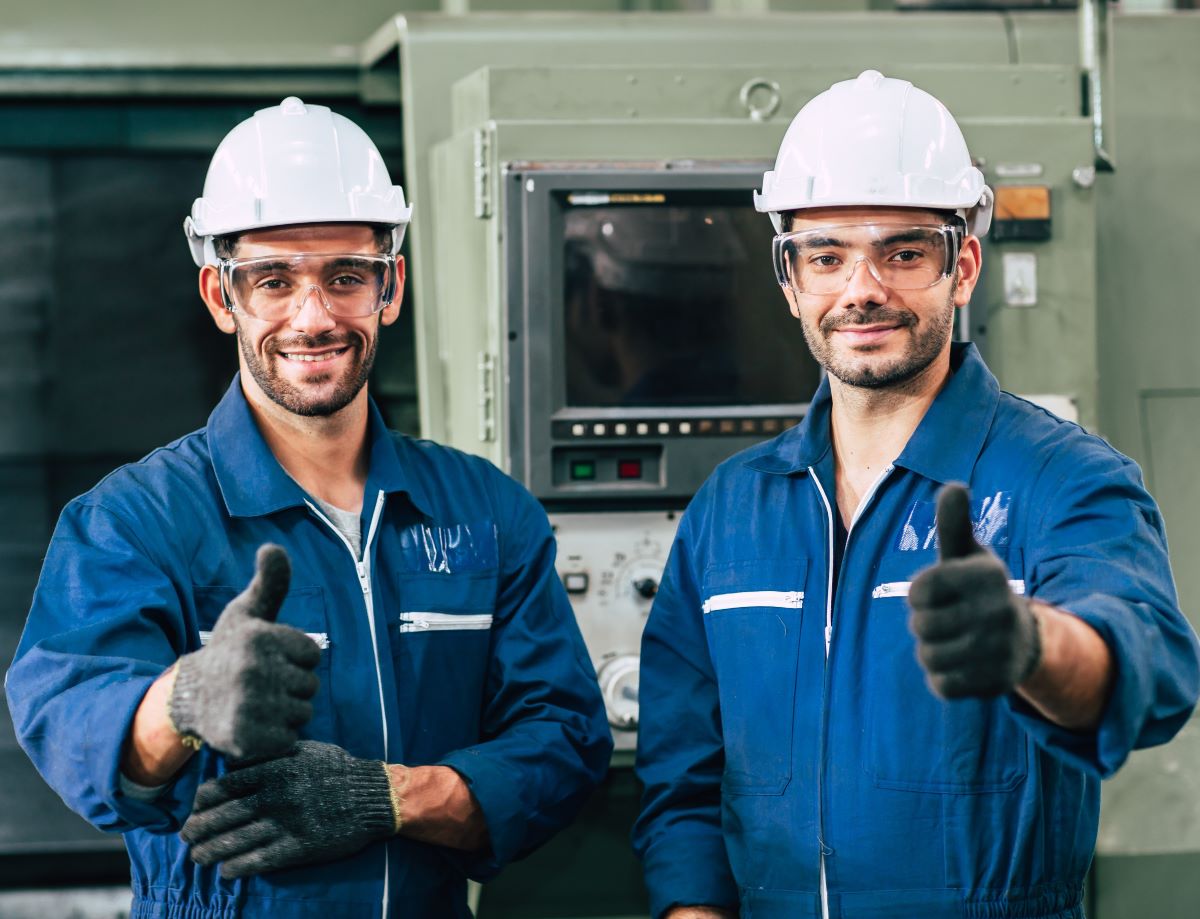
Client:
Quantity:
Size:
Application:
As published in Dry Cargo International
Dry bulk handling systems require significant maintenance, which can lead to costly downtime and create messy working conditions. To mitigate these challenges, it's crucial to consider key principles when designing dry bulk solid handling components used in these systems. This includes addressing wear and abrasion to limit maintenance, decrease production downtime, and extend the product's service life. In this guide, we'll explore how slide gates and diverter valves can be optimized to extend their service life.
SLIDE GATES
Slide gates are utilized for controlling dry bulk materials in gravity flow and dilute or dense-phase pneumatic conveying applications. There is a range of materials that slide gates handle globally, which is why manufacturers of slide gates are tasked with developing methods to extend the service life of these valves. Fortunately, a well-manufactured slide gate can be designed to allow for in-line maintenance, reducing downtime facilities experience while making repairs.
The most effective way of limiting maintenance requirements involves implementing strategies and features to limit wear. Bonnet seals are crucial to preventing material migration into the bonnet area. Otherwise, gate actuation issues and dusting into the atmosphere can occur. In applications where abrasive materials are handled, wear-compensating bonnet seals can be constructed from hard polymer and compressed rubber backing. As the polymer experiences frictional wear from multiple actuations over time, the compressed rubber load seals continuously force the polymer seal against the sliding blade. This ensures a consistent seal with limited maintenance intervention, even as the hard polymer seals wear over time.
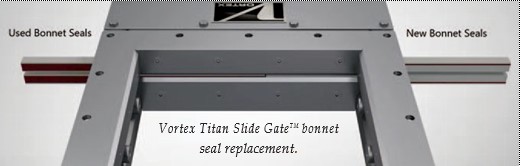
Removable access panels are key to in-line inspection and maintenance. The Vortex® Titan Slide Gate™, for example, is designed so that the bonnet seals can be replaced easily when the gate remains in-line. Simple tools can be used to remove the slot covers, and new bonnet seals can be driven into the milled access slots. The worn bonnet seals are simultaneously ejected out the other side of the gate. The Vortex® Titan Slide Gate™ is equipped with replaceable abrasion-resistant liners at the gate inlet to protect the gate's inlet, blade, rollers, and side seals from abrasive wear caused by the material flow stream. For added durability, the gate's rollers are made of hardened steel, and they are cam-adjustable for in-line maintenance.
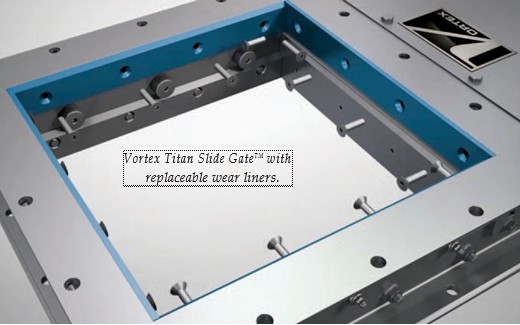
DIVERTER VALVES
Diverter valves are typically used for converging two or more lines of cement mixing material into one. They can also be used for separating one line of material into several. When designing diverters that frequently handle heavy-duty materials it is crucial to address the materials abrasive nature. By addressing these concerns when sourcing a diverter, downtime and maintenance can be minimized.
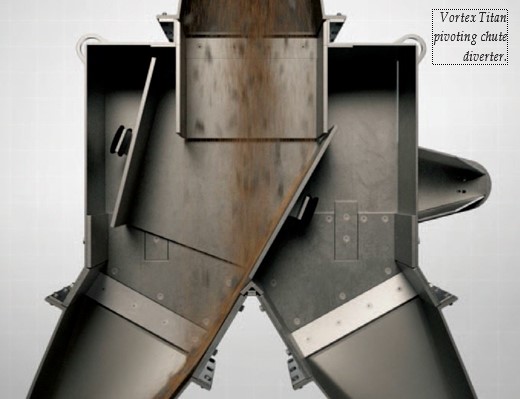
Many bucket diverters and flap diverters have thin elastomer seals adhered to the blade's perimeter. These seals are continually exposed to the material flow stream. Unfortunately, since most diverter designs do not offer necessary protection for internal seals, they erode or tear away in service, rendering them ineffective. To extend service life, Vortex® Titan Lined Diverter™ seals are constructed from a full sheet of thick rubber or kryptane, sandwiched between the diverter blade and a metal plate. Titan Lined Diverter™ are designed so that the leading edge of the blade enters a recessed area to protect the seals from the material flow stream. This will ensure that the diverter provides a positive seal across the opposite leg(s), preventing material leakage, cross-contamination, and dusting past the blade into the opposite leg(s).
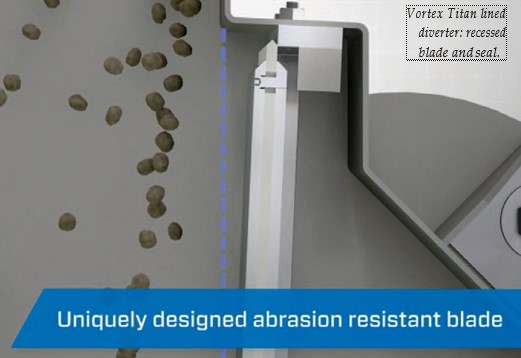
Equipping diverters with replaceable abrasion-resistant liners can also address concerns of handling abrasive materials. The purpose of these liners is to protect the diverters material contact areas and other internal mechanisms from wear caused by the material flow stream. The liners may be constructed of metal materials like 400 Brinell Hardness Number (BHN) abrasion-resistant steel and chromium carbide or even polymers depending on the application needs. Abrasion-resistant liners are critical for return-on-investment purposes because they ensure that heavy-duty materials do not abrade irreplaceable parts, resulting in full diverter replacement.
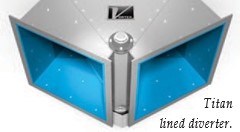
In applications where cross-contamination is not a concern, the Vortex® Aggregate Diverter™ can be utilized with rock box liners, also known as honeycomb liners, along the bucket blade and outlet chutes. The rock box design enables abrasive, dry materials to accumulate in the grid areas. As materials flow through the diverter, particles abrade upon themselves, rather than abrading upon the diverter’s material contact areas.
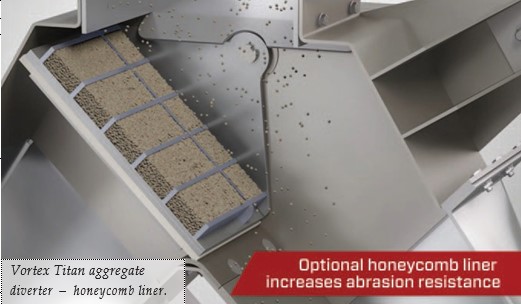
Unlike traditional diverters, the Vortex® Aggregate Diverter™, Pivoting Chute Diverter™, and Titan Lined Diverter™ feature a removable access panel design. This allows its interior inspection and/or maintenance to be performed while the valve remains in-line. These diverters are also equipped with wetted parts that can be removed and replaced through the removable access panel. This accelerates the maintenance process and prolongs a diverters service life.
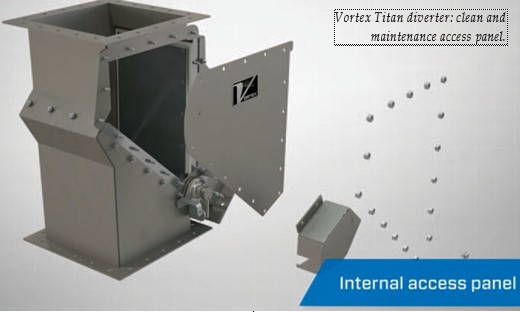
CONCLUSION
In conclusion, it's crucial to apply principles to design dry bulk solid handling components that optimize their service life, limit necessary maintenance, and decrease production downtime. Specifically, slide gates and diverter valves can be optimized using a range of features that limit wear and abrasion. Removable access panels, wear-compensating bonnet seals, and replaceable abrasion-resistant liners are key to minimizing downtime and increasing service life. The Vortex® Titan Slide Gate™, Aggregate Diverter™, Pivoting Chute Diverter™, and Titan Lined Diverter™ are all examples of dry bulk handling components that have advanced designs featuring in-line maintenance, removable access panels, and other performance-enhancing features. By embracing these principles and adopting innovative designs, facilities handling dry bulk materials can increase production time, minimize downtime, and retain the longevity of their equipment.
ABOUT VORTEX GLOBAL
Vortex Global Dry Bulk Equipment is a major manufacturer and supplier of slide gates, diverters, and other related components for handling dry bulk materials. The company has extensive experience in designing and engineering dry bulk handling equipment for various industries. Vortex Global has a strong reputation for providing high-quality solutions that are built to last and withstand the rigorous demands of the industry.
The company's focus on innovation, quality, and reliability has earned it a significant market share, with customers located around the globe. Using state-of-the-art technology and an experienced team of engineers, Vortex Global creates products that meet or exceed customers' specific needs and requirements.
Vortex Global takes pride in offering personalized attention to its customers, providing expert support and advice throughout the entire equipment lifecycle. The company's goal is to ensure customer satisfaction and loyalty by delivering superior quality products, on-time delivery, and exceptional customer service.
In addition to providing high-quality dry bulk handling equipment, Vortex Global is committed to minimizing the environ- mental impact of its products and processes. The company strives to reduce waste, conserve resources, and minimize energy consumption and greenhouse gas emissions in all aspects of its operations.
Vortex Global' s dedication to quality, innovation, and environmental responsibility has helped establish its prominent position in the dry bulk handling industry.