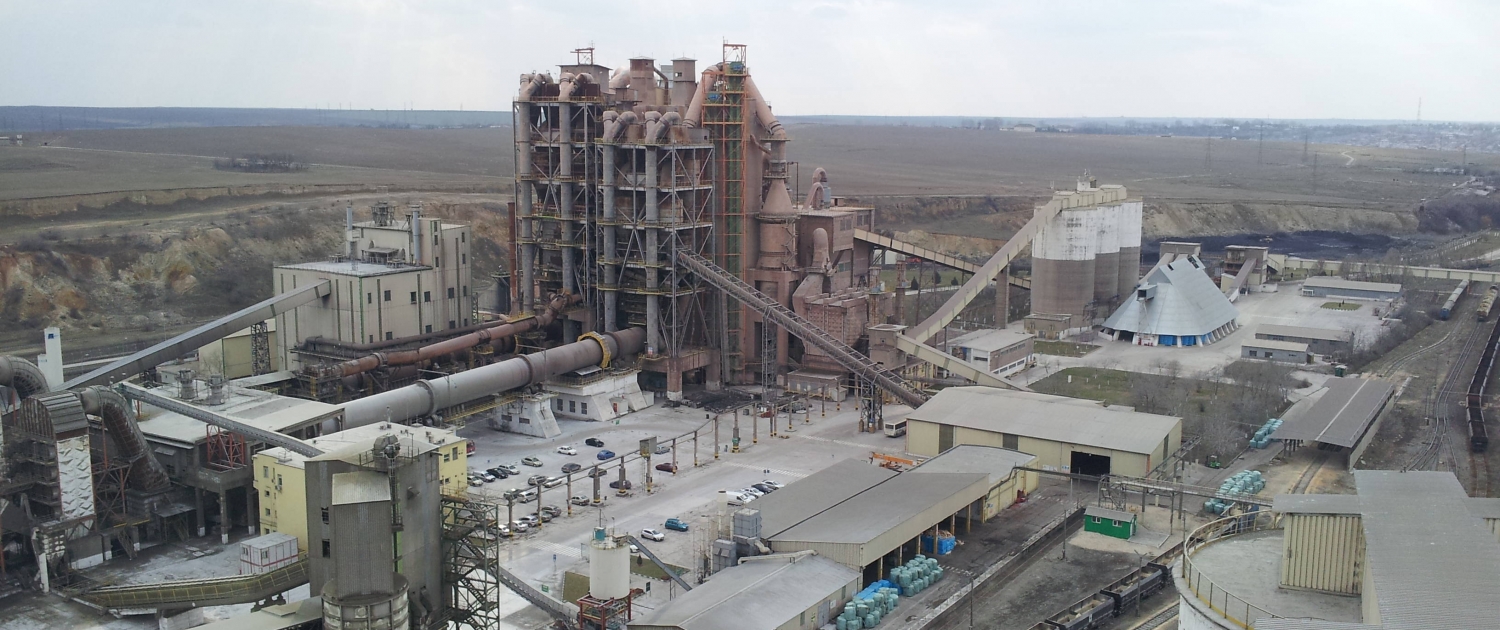
Client:
Quantity:
Size:
Application:
Many of Vortex’s innovations and new product developments have been conceived from long-standing and close working relationships with the cement, minerals and mining industries.
Common materials used in cement production include aggregates, bauxite, binding agents, clay, clinker, crushed stone, fly ash, gravel, gypsum, iron ores, limestone, sand, shale, and slag, among others. Clearly, several of these raw materials are minerals, so the two industries are dependent upon one another.
Once processed as finished product, the characteristics of cement are only moderately abrasive; but during production, the raw materials are quite harsh.
Cement, minerals and mining companies are conscious of the fact that new equipment begins to wear out immediately upon use. If less-robust valves are sourced to handle the hardness of these materials, several complications often result. Those include:
- Rapid and significant wear and abrasion to a valve’s material contact areas and other internal mechanisms;
- Worn seals;
- Material leakage through the valve and into the atmosphere; and
- Actuation issues.
Especially if the equipment is installed in high-volume and/or harsh environments, it requires almost constant maintenance and replacement. The result is downtime and lost production.
Rather than facing these recurring expenses over time, investments can be made in well-designed valves that provide durability and longevity in abrasive applications.
Slide Gates
The Vortex Titan Slide Gate is specifically designed for handling abrasive fine materials in high cycle environments, as well as for prolonged service life with minimal maintenance intervention.
Wear-Compensating Seals
Bonnet seals are important to hindering material migration into the bonnet area. Otherwise, gate actuation issues, as well as dusting into the atmosphere, can occur. Especially in cement production, the high silica concentrations pose many occupational health hazards.
The Titan Slide Gate features wear-compensating bonnet seals constructed from hard polymer and compressed rubber backing. As the polymer experiences frictional wear from many actuations over time, the compressed rubber load seals continuously force the polymer seal against the sliding blade. This ensures a consistent seal with infrequent maintenance intervention, even as the hard polymer seals experience wear over time.
In-Line Maintenance
After many cycles over time, the bonnet seals will lose their compression load and, therefore, must be replaced. The Titan Slide Gate is designed so that the bonnet seals can be easily replaced while the gate remains in-line. Using simple tools, the slot covers can be removed and new bonnet seals can be driven into the milled access slots, as the worn bonnet seals are simultaneously ejected out the other side of the gate.
Abrasion-Resistant Liners
The Titan Slide Gate is also equipped with replaceable abrasion-resistant liners at the gate's inlet. The purpose of abrasion-resistant liners is to protect the gate's inlet, blade rollers and side seals from wear caused by the material flow stream. For added durability, the gate's rollers are constructed from hardened steel.
Handling Larger Sized Materials?
The Vortex Aggregate Gate is specifically designed for handling larger sized, abrasive dry materials.
Pneumatically Conveying Materials?
Both the Titan Slide Gate and Aggregate Gate are exclusively for use in gravity flow applications. Depending on application, both the Vortex HDPV2 Gate and the Vortex Titan Pressure Valve have proven success in cement, minerals and mining pneumatic conveying applications. Contact us to discuss options.
Diverter Valves
Vortex offers several diverters specifically designed for durability and prolonged service life in abrasive applications.
Blade Seals
Most flap diverters and bucket diverters are designed with thin elastomer seals adhered to the perimeter of the blade. These seals are constantly exposed to the material flow stream. Because most diverter designs do not provide the necessary protection for the internal seals, they often erode or tear away in service, deeming them ineffective.
Instead, the Vortex Aggregate Diverter is designed with a bucket seal constructed from a full sheet of thick rubber, sandwiched between the bucket blade and a metal plate. Depending on application, the Vortex Titan Lined Diverter is designed with a blade seal constructed from a full sheet of thick Kryptane, sandwiched between the flapper blade.
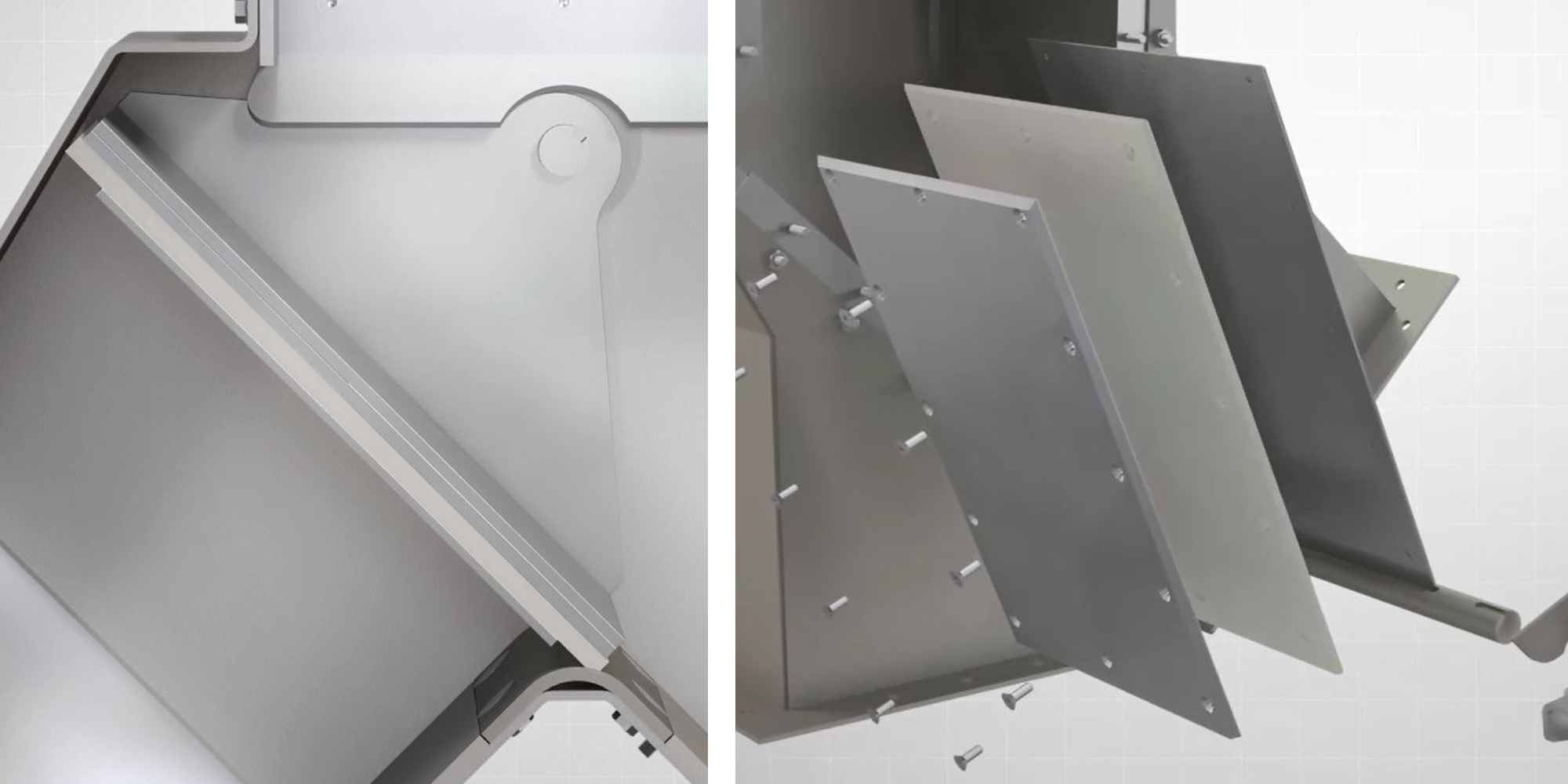
Recessed Blade
Both diverters are designed so that the leading edge of the blade enters into a recessed area, in order to protect the seals from the material flow stream. Because of these considerations, both diverters provide a positive seal across the opposite leg(s). This prevents material leakage, cross-contamination and dusting past the blade, into the opposite leg(s).
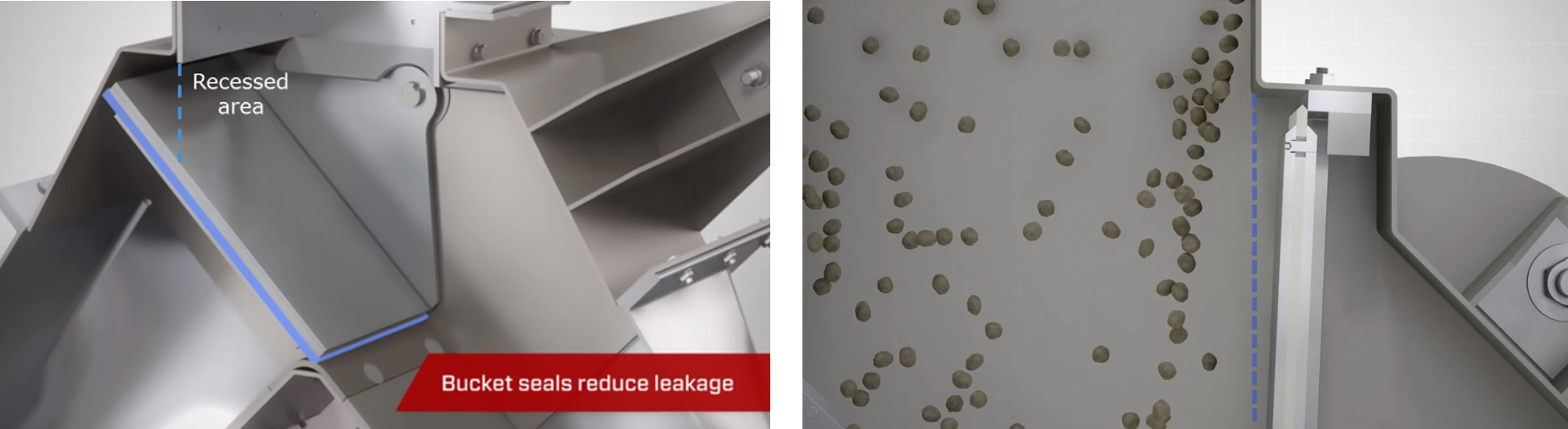
Abrasion-Resistant Liners
The Vortex Aggregate Diverter, Pivoting Chute Diverter and Titan Lined Diverter are also equipped with replaceable abrasion-resistant liners throughout. The purpose of abrasion-resistant liners is to protect the diverter's material contact areas and other internal mechanisms from wear caused by the material flow stream. Liners can be constructed from durable metal materials, including 400 Brinell Hardness Number (BHN) abrasion-resistant steel and chromium carbide. For return on investment purposes, abrasion-resistant liners are critical because they are the difference between heavy-duty materials abrading upon replaceable parts, or full diverter replacement because materials have abraded holes through the body of the valve.
Rock Box Liners
Alternatively, a Vortex Aggregate Diverter can be equipped with rock box liners – also known as honeycomb liners – along its bucket blade and outlet chutes. The rock box design allows abrasive, dry materials to accumulate in gridded areas so that as materials flow through the diverter, particles abrade upon themselves, rather than abrading upon the diverter's material contact areas.
Do note that this option is exclusive to the Aggregate Diverter and should only be considered if cross-contamination is not a concern.
Dead Pocket Inlet
The Vortex Aggregate Diverter, Titan Lined Diverter and the Pivoting Chute Diverter can all be equipped with a dead pocket inlet. As materials pass through the diverter's inlet, trace amounts accumulate in the dead pocket. The dead pocket ensures that as materials continue to flow through the diverter, particles abrade upon themselves as they pass through the inlet, rather than abrading upon the inlet itself.
Do note that this option should only be considered if cross-contamination is not a concern.
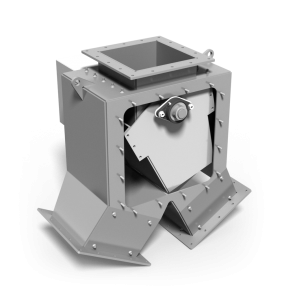
Pivoting Chute
A disadvantage to both flap diverters and bucket diverters is that a slide gate is recommended above the diverter, in order to shut off flow prior to shifting the blade. With this pain-point in mind, Vortex designed the Pivoting Chute Diverter to improve processing speeds and prolong service life.
The Vortex Pivoting Chute Diverter features an independent, internal chute that "pivots" between outlet legs. Unlike flap diverters and bucket diverters, the Pivoting Chute Diverter can be shifted fully toward a single outlet, or shifted partially to split flow toward two destinations simultaneously. As the chute pivots, changes in the material flow pattern are subtle – which decelerates the rate of wear to the chute itself.
In-Line Maintenance
Many diverters are not designed to be maintained while in-line. Instead, the entire diverter must be removed from service, which results in significant downtime and expensive diverter rebuild or replacement. The Vortex Aggregate Diverter, Pivoting Chute Diverter and Titan Lined Diverter are all designed with a removable access panel, which allows interior inspection and/or maintenance to be performed while the valve remains in-line.
The Vortex Aggregate Diverter, Pivoting Chute Diverter and Titan Lined Diverter are also designed with wetted parts that can be removed and replaced through the removable access panel. This accelerates the maintenance process and prolongs a diverter's service life.
"Y"-Type vs. Straight-Through Diverting
A diverter is afforded additional wear resistance if it is designed with a straight-through ("K-Style") leg instead of "Y"-type ("A-Style") legs. The straight-through diverting option is often used in applications where material is being routed toward a primary destination, while only occasionally shifting to the "off leg."
In abrasive applications, K-style diverting is recommended because it allows a straight-through channel for material flow. It also makes it so that the outlet legs do not meet in the direct path of travel as materials flow through the inlet. For both of these reasons, straight-through diverting can lessen the degree of wear to a diverter's material contact areas.
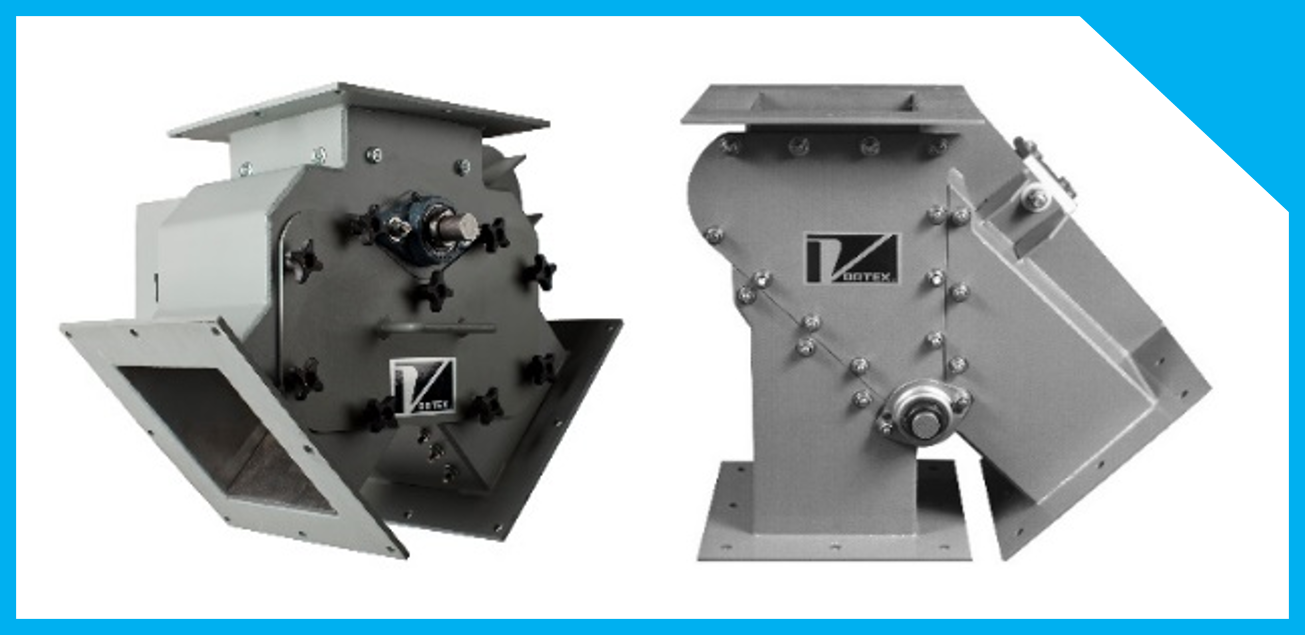
Steep Outlet Angles
When diverting abrasive materials in gravity flow, wear can be minimized by using steep angles at each of the diverter’s outlet legs.
Often times, raw materials used in cement production have a high bulk density because of the material’s hardness. If a diverter has more subtle outlet angles (approximately 45° from vertical), material velocity will slow, causing materials to drag along the bottom of the diverter as they flow through.
Oppositely, if a diverter has steeper outlet angles (approximately 30° from vertical), materials are able to suspend and flow freely through the channel. This allows optimal flow rates for most materials handled in cement, minerals and mining applications, and also reduces the likelihood of materials plugging the line.
When materials are suspended, they make little contact with the diverter’s material contact areas. Thus, the diverter is subject to less wear and abrasion.
Durable Metal Materials of Construction
When handling heavy-duty materials, valves are afforded greater durability if they are constructed from abrasion-resistant metals. Those include 400 BHN abrasion-resistant steel, chromium carbide, and even other stronger metals, depending on application.
These are just some of the many techniques for preventing wear and abrasion in dry bulk solids material handling applications.
Our Partners: The Cement, Minerals & Mining Industries
As detailed above, Vortex identified a need in these industries for improved product design, in order to address common causes of equipment failure. Several of our largest and longest-standing clients are multinational companies within the cement, minerals and mining industries. Those include LafargeHolcim, Heidelberg Cement, Quikrete, Cemex, Buzzi Unicem, Vale and Rio Tinto, among others.
Staying true to our design philosophy, Vortex couples robust metal materials of construction with unique design to protect against erosive wear, impact wear, and other forms of abrasion to material contact areas.
Our design improvements include:
- Identifying key wear points and reinforcing those areas with abrasion-resistant materials;
- Replaceable parts to extend service life and reduce lifecycle costs; and
- In-line service features to reduce the time it takes to perform inspection or maintenance. Performing service while equipment remains in-line reduces downtime and other maintenance costs.
...among many others.
Vortex slide gates, diverter valves and loading solutions can be used at any stage in the production or transportation processes – from raw aggregates to the transloading facility. Whether it be small- or large-sized dry materials, Vortex offers a durable, reliable and versatile solution for each stage in the process.