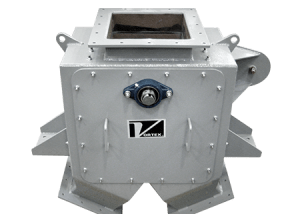
Client:
Quantity:
Size:
Application:
In 2015, Hareza Technical Sales, Inc. – a manufacturers’ representative for Vortex – was contacted by an engineering firm to discuss an upcoming process need they had. This particular OEM/engineering firm specializes in the design and construction of alloy additive systems for steel mills. The engineering firm was tasked with designing a system for a customer handling heavy bulk density alloys. In particular, they sought a Vortex diverter to incorporate into the system design.
However, the handled material’s characteristics were quite complex. This included:
- Bulk density ranging 150 – 200 pcf
- Particle size ranging 2” – 4” (51mm - 102mm)
- Extremely abrasive material
Because of the alloy’s unique properties, it is capable of wearing out a conventional diverter in no time. In response, Vortex custom-engineered a diverter built for durability and longevity in extremely abrasive dry material handling applications.
- Product: Vortex Pivoting Chute Diverter
- Quantity: 7
- Size: 18 in. | 455 mm
Specifications:
- 2-way diverting design.
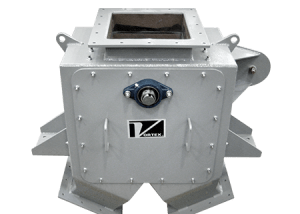
- Valve body constructed from 3/8” thickness Tri-Braze abrasion-resistant/impact-resistant steel plate.
- Wetted parts & liners constructed from ¾” thickness Tri-Braze abrasion-resistant/impact-resistant steel plate with 3/8” thickness chromium carbide overlay.
- Surface edge where the two outlet legs meet is lined with ¾” thickness chromium carbide.
- Flanges constructed from ½” thickness A36 steel.
- (Qty. 2) Outlet legs offset 30° from vertical. (Qty. 5) Outlet legs offset 45° from vertical.
- Modified to handle material temperatures up to 250° F | 121° C continuous service.
- Equipped with chute removal assist rods.
- Painted to match customer specifications.
Features:
- Removable access door for inspection and/or maintenance. Using only simple tools, the access door can be removed and the diverter’s internal parts can be accessed while the valve remains in-line. This feature significantly reduces downtime by accelerating the maintenance process.
- Wetted parts are removable through the access door to allow part maintenance and/or replacement while the diverter remains in-line. This includes the “pivoting” chute, the inlet chute, and the liners, among other parts. If maintained and operated as recommended, these should be the diverter’s only wear parts. In several cases, this has allowed a Vortex Pivoting Chute Diverter to remain in service for many years.
- Replaceable abrasion-resistant liners. For return on investment purposes, abrasion-resistant liners are essential because they ensure materials abrade upon replaceable parts, rather than abrading through the diverter body and creating need for full diverter replacement. This feature significantly prolongs a diverter’s service life.
- The Pivoting Chute Diverter features a “pivoting” straight-through channel for material flow, so that it can be used either to channel materials directly toward a single destination, or split flow toward two destinations.
Results:
Now three years later, the client is pleased with the durability of their Vortex Pivoting Chute Diverters. To date, all seven diverters continue to be in service, no spare parts have been ordered, and only preventative maintenance has been performed.
Because of Vortex’s willingness to customize these diverters in order to best suit the end user’s needs, HTS established a relationship with this OEM/engineering firm for the duration of the project. All-in-all, HTS provided more than $100,000 worth of equipment for this steel mill.