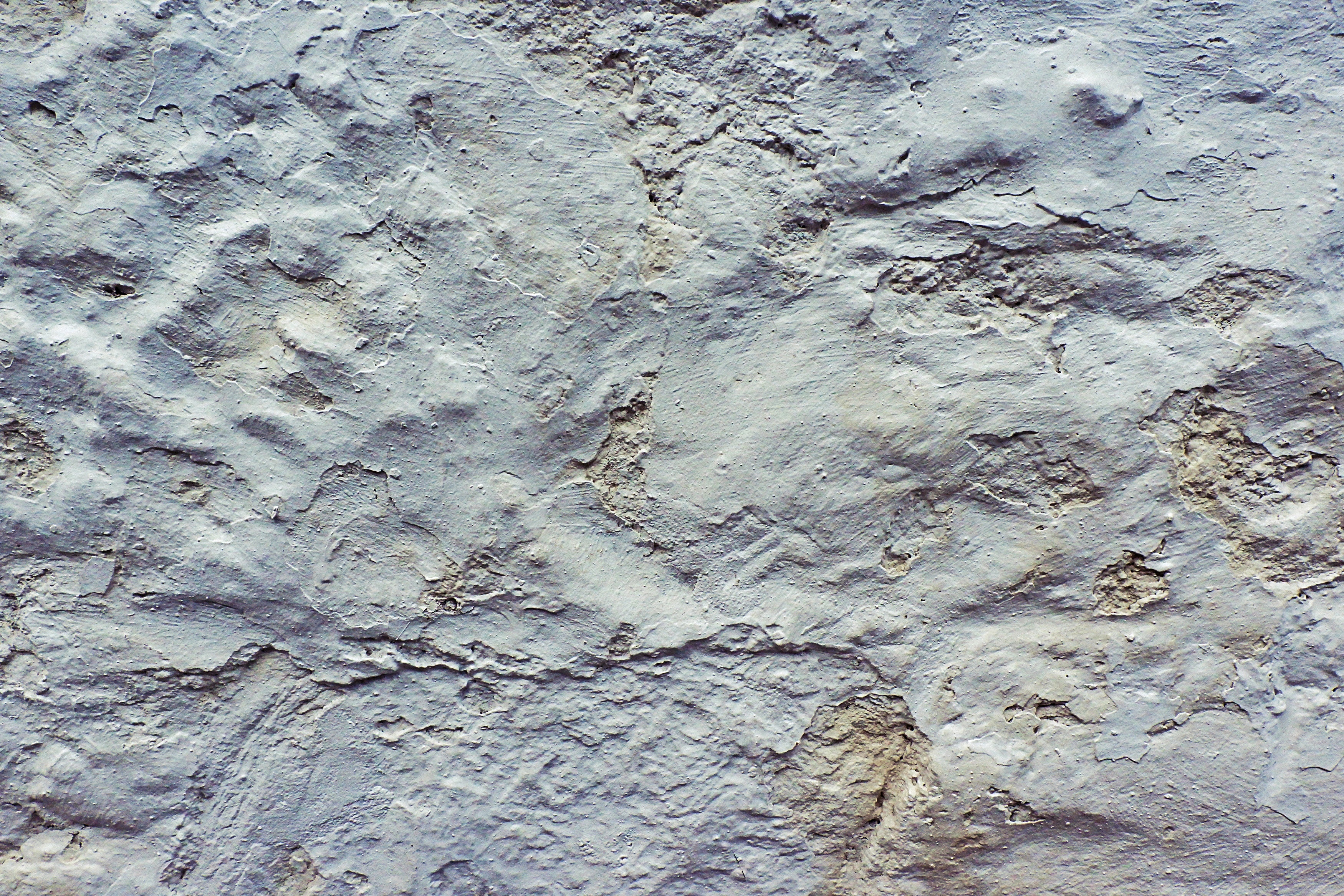
Client:
Quantity:
Size:
Application:
What it is
Limestone is a carbonate sedimentary rock made up of skeletal fragments from marine organisms. There are many types of liming materials, including calcium carbonate, calcium oxide (also known as “burnt lime” or “quick lime”), calcium hydroxide, magnesium carbonate, and magnesium oxide, to name a few. These are essential minerals utilized in many different industries.
How it’s used
Uses of limestone include:
- A conditioner to neutralize acidic soils.
- The base aggregate for road construction.
- A cement and mortar ingredient.
- For air pollution control, a re-agent for flue gas desulfurization.
- In coal mines, a suppressant for methane explosions.
- In iron making, removes impurities from blast furnaces.
- A calcium supplement for livestock and poultry.
- A calcium source for cereals and breads.
- A filler and pigment for toothpaste, paper, plastics, paint and tiles, among other end products.
It is interesting to note that even the Pyramids in Egypt are made of limestone.
Market Overview
At 230 million metric tonnes (mmt), China produces more than 50% of the world’s lime and limestone. Following is the USA at 19 mmt, and India at 16 mmt. USA limestone production is valved at $2.3 billion USD.
Liming Materials & Vortex Global
Vortex Global designs and manufactures slide gates, diverter valves and loading solutions specifically intended and modified to handle liming materials.
Following is three such examples.
1. Limestone Rock Used in Cement Production
Portland cement is produced by burning a mixture of lime and clay, as well as a few other ingredients, to form clinker. The clinker is cooled then pulverized into fine cement.
Case Study
Customer: Cement manufacturer
Application: Using a belt conveyor, transport limestone rock from a nearby mine into two crushers.
Challenge:
The customer previously used a bucket-style diverter in this application. The bucket diverter lacked capabilities in that:
- Material could only be sent to one crusher at a time.
- Clay was conveyed with the limestone rock. When moist, the clay had a tendency to cake and build up around the bucket blade. Over time, the bucket would bind up and cause actuation difficulties.
- Because it lacked interior accessibility, the bucket diverter was difficult to maintain.
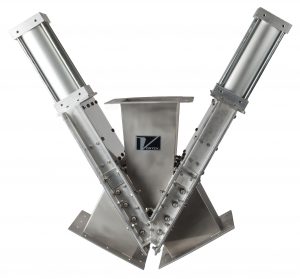
Solution:
The existing bucket-style diverter was replaced with a Vortex Gravity Vee Diverter. The Vortex Gravity Vee Diverter is made up of two independently actuated slide gates, arranged in a “V” configuration. Its primary benefit is that material flow can be directed:
- Toward both outlets simultaneously;
- Toward either outlet separately; or
- A complete shut-off of material flow through the diverter.
For this application, the Gravity Vee Diverter was modified with:
- Blades constructed from 400 Brinell Hardness Number (BHN) abrasion-resistant steel, to address the hardness of the handled material.
- The blades are beveled to close through the moist clay build-up.
- A removable access panel was added to both outlet legs. This allows for interior inspection and maintenance – such as removing hardened clay – while the diverter remains in-line.
2. Quick Lime Production
It takes approximately 1.8 tons of limestone to produce 1 ton of quick lime. Quick lime is produced by heating limestone in a kiln. The process, known as calcining, heats the limestone above 1,500° F | 815° C to liberate a carbon dioxide molecule.
Quick lime has many uses. Primary uses include:
- Neutralizing acidic oxides in steel production.
- In the production of aerated concrete blocks.
- Increasing the load carrying capacity in clay soils.
Because quick lime reacts with water to produce heat, it can also be used for food warming in self-heating cans, as well as water heating without open flames.
Case Study
Customer: Quick lime manufacturer
Application: Control the flow of quick lime from a holding bin.
Challenge:
Even though the quick lime was downstream form the hot kiln, it still contained elevated temperatures of 850 – 1,000° F | 455 – 540° C.
At these temperatures:
- Polymer seals could not be used to seal the fine material across the gate and to atmosphere.
- The blade and metal seats could expand and contract, causing issues.
- Pneumatic actuation was preferred. However, the rubber or polymer seals normally used within an air cylinder could not stand up to the high material temperatures.
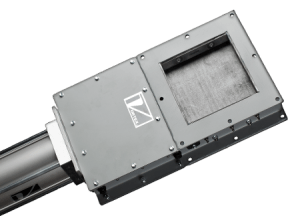
Solution:
For this application, the Vortex Titan Slide Gate was modified with:
- A sliding blade and inlet liners constructed from 400 Brinell Hardness Number (BHN) abrasion-resistant steel, to address the hardness of the handled material.
- Because the gate would be idled from time to time for system maintenance – and it would, therefore, be exposed to ambient temperatures – the metal blade, support rollers, and metal seats were designed with tolerances that allow for metal expansion and contraction.
- A high temperature-resistant painted frame.
The request for pneumatic actuation proved to be more of a challenge. For many higher temperature applications, this temperature constraint typically excludes the use of pneumatic actuators.
An air cylinder must be constructed with rubber seals to effectively contain the air pressures required to move the cylinder rod and actuate the gate. High temperature Viton seals are only rated to 400° F | 205° C. Because Vortex Global also designs and manufactures its own air cylinders, they considered this application and developed a “cylinder within a cylinder” actuator.
It works by:
- Supplying compressed plant air into the internal “working” cylinder, which actuates the piston and cylinder rod; while
- Simultaneously supplying compressed plant air into the surrounding cylinder. This creates a blanket of cooler air, which cools the air and seals within the “working” cylinder.
To date, this solution has met the customer’s requirements and has been successful in the application.
3. Pebble Lime Used in Steel Production
Pebble lime is crushed quick lime, sized between ¼ – 2 ½ in | 6 – 65 mm. It is essential to the following stages in the steelmaking process:
- Beginning the steelmaking process – Pebble lime helps remove phosphorus, silica and alumina from iron ores and scrap metals.
- Slag formation – Pebble lime accumulates waste materials produced in the steelmaking process.
- Concluding the steelmaking process – Pebble lime reduces the damaging effects of sulphur, which could otherwise make the steel fragile.
In essence, the steel industry would not exist without pebble lime.
Case Study
Customer: Steel mill
Application: Pneumatically convey ½ in | 13 mm pebble lime at 10 psig | 0.7 barg from one source toward three destinations.
Challenge: The Customer sought independent control over all three destinations. This would allow pebble lime to be conveyed toward each destination individually, or all closed for a complete shut-off of material flow through the diverter.
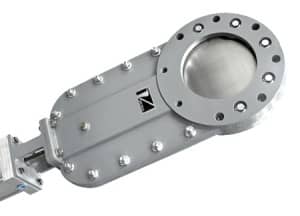
Solution:
For this application, a Vortex Mainline Diverter was designed with three Vortex Titan Pressure Valves (TPVs). The diverter was modified to the following:
- Because the customer uses schedule 80 pipe conveying lines, this diverter’s gates and inlet weldment were sized to match.
- Because of the abrasive characteristics of pebble lime, over time, even these thick steel pipes would experience significant wear. To address that wear, ceramic backing was added to the inlet weldment for this diverter. Once pebble lime wears its way through the schedule 80 steel pipe, it then has to contend with layers of hardened ceramic.
As a standard, the Vortex Titan Pressure Valve is also designed with a blade and metal seats constructed from 440 C stainless steel (60 C Rockwell hardness), to address the abrasiveness of handled materials.
Results:
Four years after this diverter began operations, the customer ordered a replacement inlet weldment to the same specifications – schedule 80 pipe with ceramic backing. They were very pleased by the extended service life the previous inlet weldment provided. To date, no maintenance has been performed on the Titan Pressure Valves.
Conclusion
Whether it is a product derived from limestone or another mineral, Vortex Global is known for their solutions which are engineered for success in the specific applications they are being sourced for.