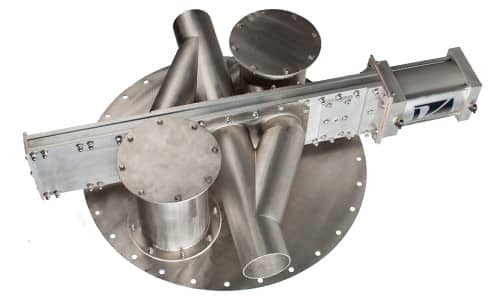
Client:
Quantity:
Size:
Application:
Transport flour via a closed-loop pneumatic conveying system. The client is conveying flour from a mill storage silo through a blending facility, where ingredients were added into 12 storage bins. At the three packing stations, four storage bins feed each packer to dispense flour mixture into bags ranging from 30-50 lb | 15-20 kg each. The goal was to speed production to between 80,000- 100,000 lb/hr | 36,285-45,360 kg/hr, and to improve sanitation within the facility. The top filter on each individual storage bin was a source of potential infestation.
Features:
- Each valve is equipped with an Air Purge Assembly to prevent fine materials from migrating into the gate's bonnet area.
Results:
Company project engineers were familiar with Vortex valves. This facility had previously installed Wye Line Diverters at its rail load-out station and was pleased with the service they provided.
The client likes the Fill Pass Diverter's many design benefits. Those include a positive seal of materials and dusts, reduced fill times, and self-cleaning valve mechanics.
Through the new closed-loop system, sanitation inspections could be done at the system’s common filter receiver, rather than at each individual filter.