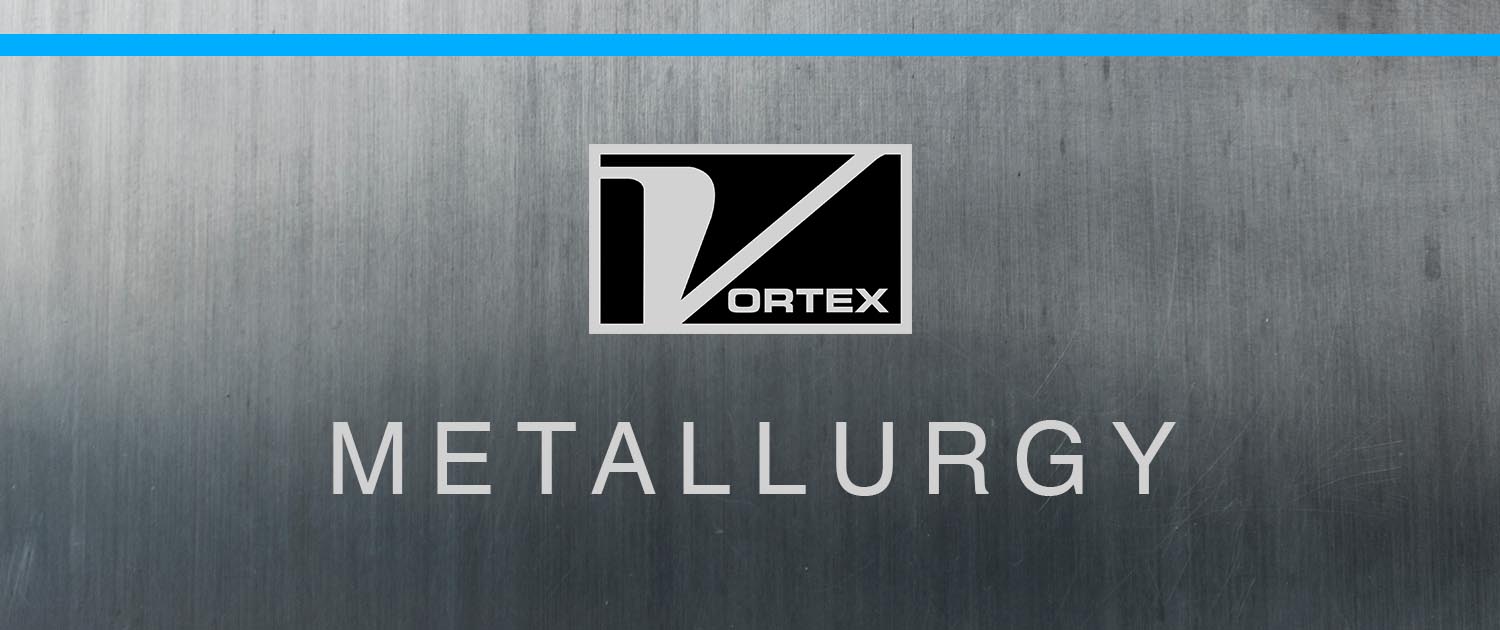
Client:
Quantity:
Size:
Application:
...a Q&A with Paul Deegan, Engineering Manager – Special Projects, Vortex
As Published in PBE-News, Powder and Bulk Engineering's Newsletter for the Dry Bulk Materials Industry
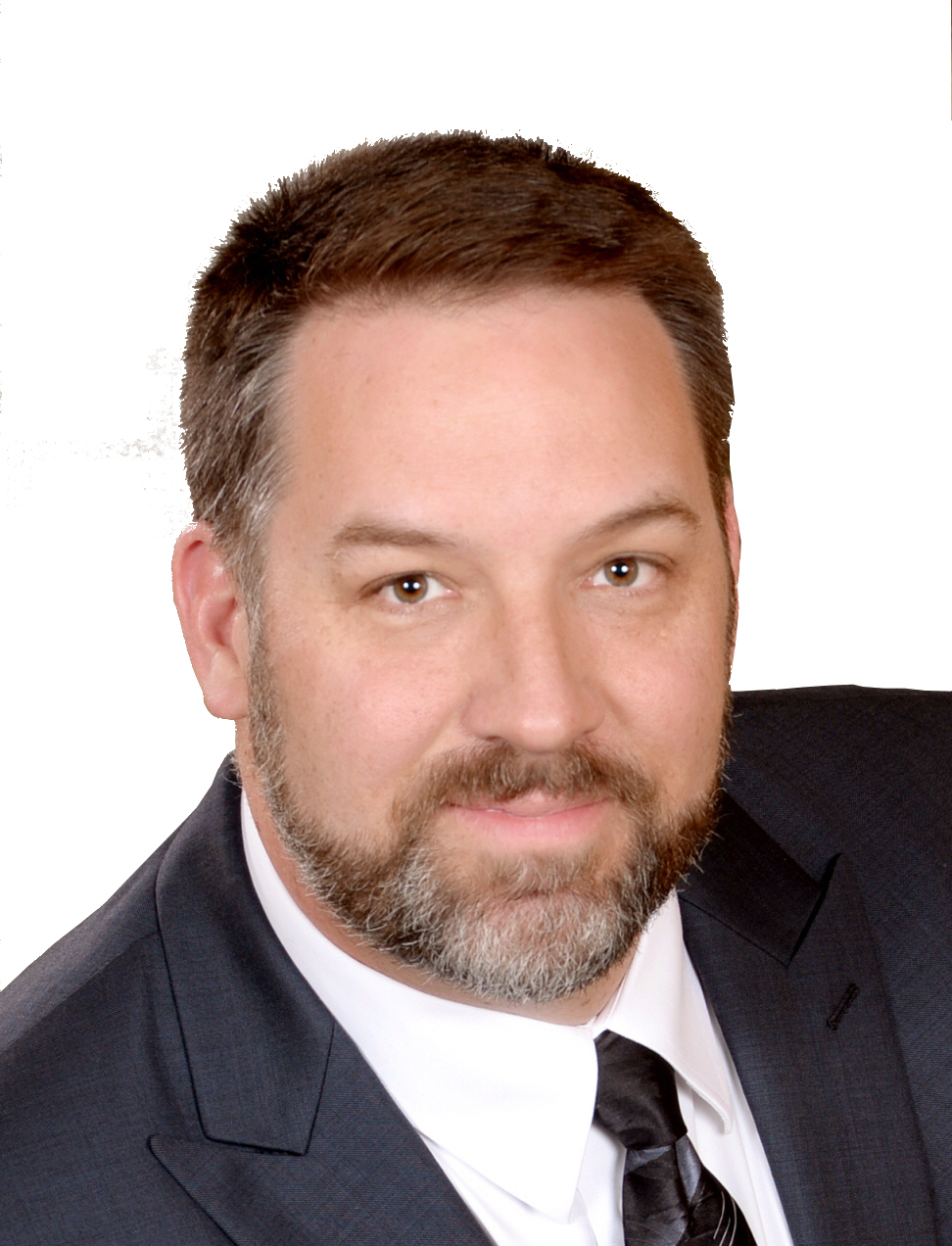
Q. Industrial equipment manufacturers offer several metal material options for equipment construction. What are the differences in usage?
A. The most common metals offered are AISI Type 304 and Type 316 stainless steel, as well as AISI 1008/1010 or ASTM A36, which is typically referred to as "carbon steel." These metals are used to construct the "wetted" parts in a piece of equipment — that is, those parts which come in contact with the conveyed material in a manufacturing process. Alternatively, the frame or structure in a piece of equipment is usually made from either aluminum or carbon steel because they offer weight advantages, cost savings, or both.
Q. What is the difference between Type 304 and Type 316 stainless steel?
A. There are numerous stainless steel grades available, but Type 304 and Type 316 are the most commonly used in bulk handling and many other industries. This is because both types are relatively easy to machine, bend, and weld. In addition, grades Type 304 and Type 316 offer good corrosion resistance at a reasonable cost, compared to other steel grades. The alloying elements that are primarily responsible for corrosion resistance are chromium and nickel.
- Type 304 stainless steel: 18% chromium & 8% nickel
- Type 316 stainless steel: 16% chromium & 10% nickel
Both elements are expensive and increased quantities of either element will make the steel more expensive, with nickel being more expensive than chromium. In fact, it currently costs more than five cents to produce a five cent ("nickel") coin. There are grades of Type 300 series steel that are more corrosion resistant than Type 304 or Type 316, but because they have increased amounts of chromium and/or nickel, or some other alloying element(s), they are, consequently, more expensive.
Q. What makes stainless steels "stainless?"
A. Stainless steels are "stainless" due to the addition of chromium. The reaction between chromium and oxygen creates a submicroscopic film of tightly-adherent, nonporous chromium oxide, which protects the underlying metal from contact with the environment.
Q. What chromium concentration is necessary to render a steel "stainless?"
A. In order to form the "stainless" chromium oxide layer at the steel's surface, chromium concentration must be at least 10 percent.
Q. Which stainless steel type has enhanced corrosion resistance and added strength at elevated temperatures?
A. A distinguishing factor between Type 304 and Type 316 stainless steel is that Type 316 also contains the alloying element molybdenum. Molybdenum reduces the tendency of chromium oxide layers to break down, therefore increasing the steel's corrosion resistance. Additionally, molybdenum benefits steel by increasing its strength at elevated temperatures. Adding molybdenum, however, requires the addition of more nickel as compared to Type 304. To understand why, it's important to understand the microstructure of various stainless steels.
Q. What is the microstructure of steel?
A. Imagine a cube in which the atoms are arranged at the corners of the cube, as well as in the center of each face of the cube. This microstructure is called face centered cubic (FCC) and is the structure of austenitic steel. Type 300 series stainless steels are austenitic.
Oppositely, imagine a cube in which there are atoms at each corner of the cube, but instead of an atom in each face of the cube, there is an atom in the center of the cube. This microstructure is called body centered cubic (BCC) and is the structure of ferritic steel.
During steel production, when a steel with BCC microstructure at lower temperatures is heated to high temperatures (above 1,670°F | 910°C), it will transition to FCC. As it cools, the steel will return to a BCC microstructure. However, some alloying elements will prevent the transition from FCC to BCC, while others promote it. Referring back to Type 316 stainless steel, molybdenum is an element that promotes this transition, while nickel helps prevent it. Therefore, adding molybdenum requires additional nickel to keep the steel in the austenitic phase.
Q. What differentiates L-grade stainless steel?
A. The "L" at the end of Type 300 series stainless steel grades (i.e. Type 316L) signifies "low carbon."
- Carbon contents (Type 304 & Type 316 stainless steel): ~0.08%
- Carbon contents (L-grades stainless steel): ~0.03%
Q. What is the benefit of constructing welded components from L-grade steel?
A. During welding, the carbon and chromium elements of 300 series stainless steels begin to react with one another, forming chromium carbide. Because the chromium is transformed into chromium carbide, there isn't enough chromium remaining in the steel to form the chromium oxide layer. This results in rust forming in the areas near the weld. By reducing the carbon contents in L-grade steel, the formation of chromium carbide during welding is hindered, and thus, lessens the chance for corrosion along welded joints. Accordingly, it's only necessary to specify L-grade steel for welded components.
Q. What is your advice for those currently researching industrial equipment options?
A. As one of my mentors always used to say:
"A true metallurgist responds to most metallurgy questions with, 'It depends.'"
From the explanations above, you have likely noted the difficulties in assessing metal materials of construction. Because of this, industrial equipment manufacturers must assess bulk handling applications on a case-by-case basis to ensure the equipment's success. Therefore, I strongly recommend to consult with process engineering experts before making equipment acquisition decisions.
For more information, please contact us.