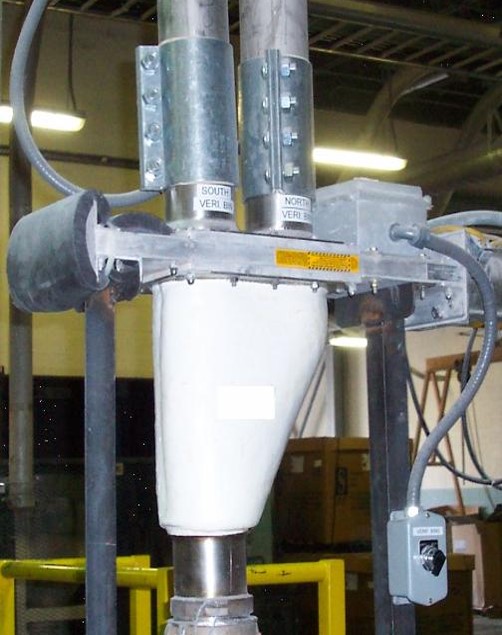
Client:
Quantity:
Size:
Application:
Challenge:
Provide a diverter capable of withstanding the abrasiveness of fiberglass-filled pellets.
Features:
- Ceramic backing.
- Straight-leg diverting design.
- Actuator position modification.
Result:
This US-based division of an international company manufactures an extremely abrasive grade of polymer pellet. As such, the company’s UK-based sister facility advised that they source new material transfer components capable of withstanding the product’s abrasive characteristics.
The company compounds virgin polymer, powders, colorings, UV inhibitors, and chopped fiberglass to create a polymer pellet which contains up to 50 percent fiberglass. These compounded pellets are sold to molders that manufacture plastic parts used by the automotive industry.
Installed in October 2003, three significant modifications were made to the Vortex Wye Line Diverter for use in this particular application:
- The valve inlet was ceramic-backed to offer additional abrasion resistance.
- The customer requested a straight-leg diverting design.
- The customer specified the valve’s straight leg be opposite the air cylinder (as pictured). In standard installations, the straight leg would be adjacent to the air cylinder.
Today, this facility’s ceramic-backed Vortex Wye Line Diverter handles 5,000 pounds/hour, 24 hours/day, 6 days/week. The valve has been successful in this high-actuation application, which has led to additional installations of Vortex slide gates and diverters in this facility.