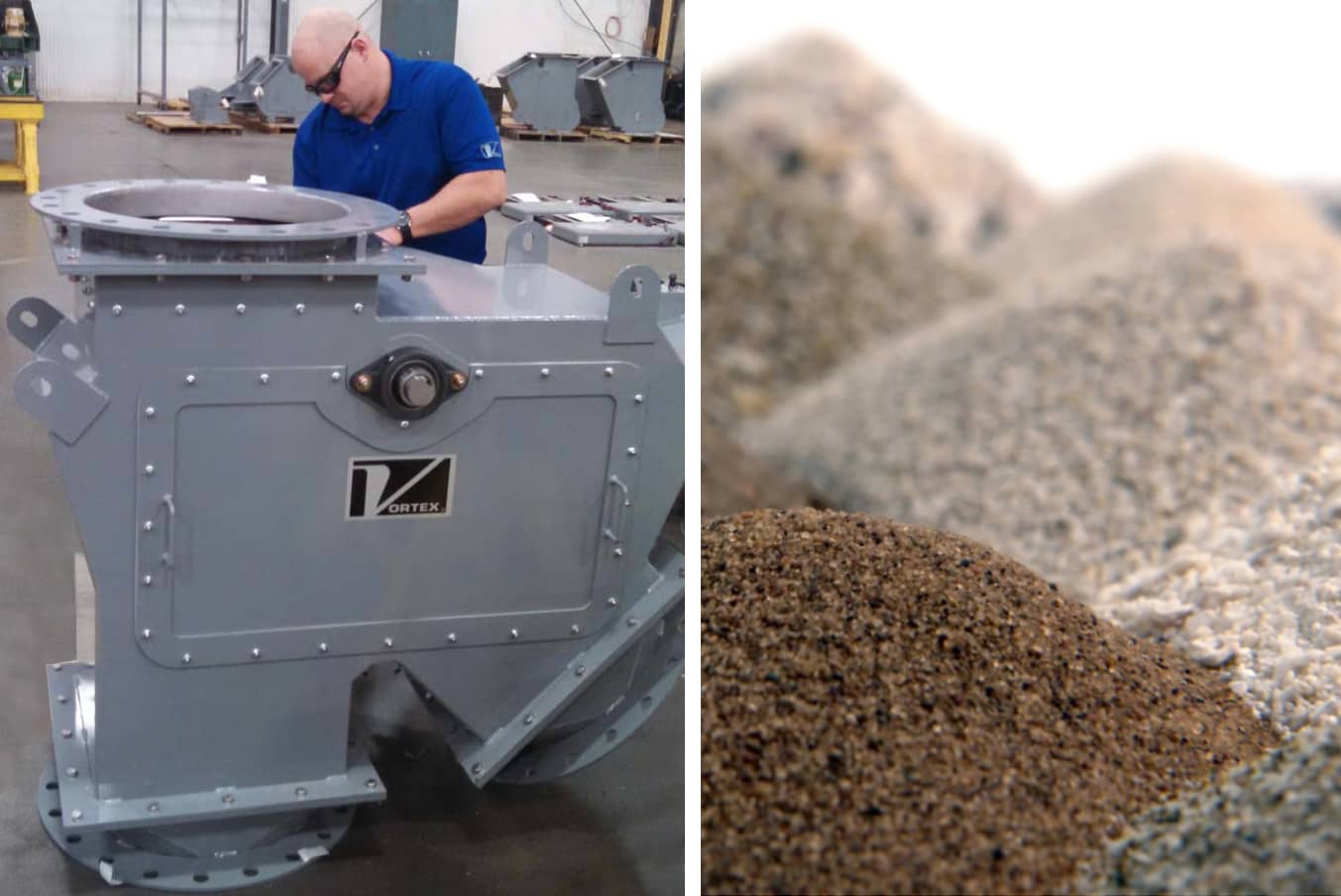
Client:
Quantity:
Size:
Application:
…a Q&A with Kevin R. Peterson, Regional Director of Business Development, Vortex
Q. We are conveying foundry sand and our diverter valves wear out too frequently. What qualities should we look for when replacing these valves?
A. A wide range of diverter valves is available for handling abrasive materials, such as sand. It is important that all of your application parameters are addressed to be sure you choose the appropriate diverter, equipped with the necessary abrasion-resistant modifications.
One philosophy is to construct the internal material contact points from abrasion-resistant (AR) materials. Examples include AR plate or ceramic. The purpose for using these more durable materials is to decelerate the wearing process.
Another approach is to incorporate dead pocket areas into the material flow stream. These dead pockets fill up with material, creating an area where material impacts on itself—protecting the valve from additional wear. Do note: dead pocket areas should only be considered for applications where material cross-contamination is not an issue.
When considering wear modifications to existing diverters, it’s important that the parts are easily accessed for future replacement. This will provide tremendous maintenance cost savings. Selecting a manufacturer with proven experience in designing and manufacturing diverters for handling abrasive material is key to ensuring favorable life-cycle equipment costs.