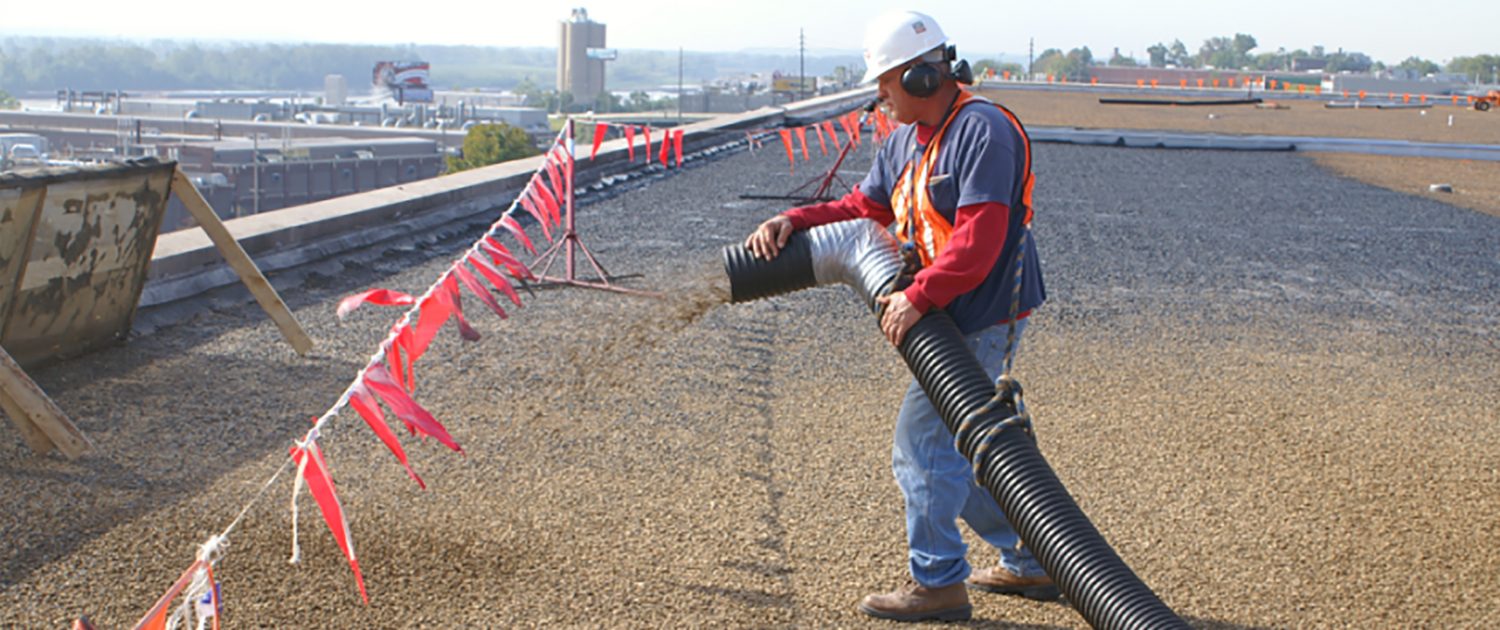
Client:
Quantity:
Size:
Application:
Placing a layer of rock ballast over the membrane of a rooftop holds the components in place, allows for future building movement, protects the membrane from potentially destructive UV sun rays and weather, and greatly extends the life of the roof. The components of a ballasted roof (insulation, thermal barrier, and waterproof membrane) are not adhered to the roof deck to reduce overall costs and installation time.
Vac-It-All is a St. Louis-based contracting company that specializes in the preparation of roof surfaces. Founded in 1979, the company has completed a wide range of projects for multi-level and industrial buildings across both North America and Europe, moving thousands of tons of rock in the process. Whether re-roofing or installing ballasted single‐ply or inverted roof membrane systems, Vac‐It‐All’s method for moving material can greatly reduce the cost of removing or placing rock ballast on the roofing surface.
Efficiently Transporting Material
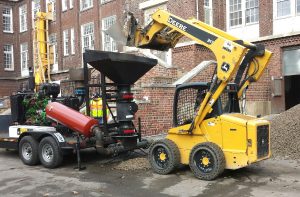
Moving large quantities of heavy rock from trucks to rooftops can be a difficult and time-consuming job. Vac-It-All uses rock ranging from 3/4″ – 1.5″ (20mm – 40mm). For many years, the company used a belt conveyor to convey rock to the roof, then distributed the rock across the roof using wheelbarrows.
To accelerate the process, Vac-It-All owner Dave Settlemoir designed a pressure pneumatic conveying system capable of conveying decking material to roofs up to 10 stories high, or 1,000 feet (305m) horizontally from the initial load point. The system is mounted on a trailer and uses a 10″ (255mm) conveying line to move material from a hopper to the rooftop, where an operator can direct the material where needed.
“When working commercial projects, customers want the roof installed quickly to avoid potential weather issues,” Settlemoir says. “They also want contractor equipment out of the way of their daily business interactions.”
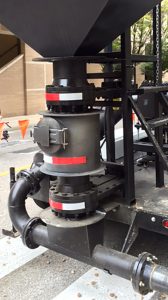
Two 10″ (255mm) Vortex TPV slide-gate valves are key to Settlemoir’s system. Vortex slide-gate valves have a center opening that is the same diameter as the material handling line and a blade that, when actuated, slides across the opening to block material flow. The TPV slide-gate valve is designed to handle abrasive, dry material, such as minerals, industrial sand and fly ash. The valves’ blades and seals are constructed from 440 C stainless steel. Both the blades and the seals can be replaced in the event of wear, increasing the life of the valves and forgoing the need to purchase an entire new replacement valve.
In Vac-It-All’s system, the TPV slide-gate valves are stacked vertically, separated by a chamber. The two valves work together to feed material into a conveying system without allowing any air pressure to escape. Both gates are initially closed. Then, the top gate opens for two seconds and uses hydraulics to allow material to fall into the chamber from a hopper above. Then, the top gate closes and the bottom gate opens for two seconds, to allow the material to enter the conveying line below. The bottom gate closes, and the process repeats as needed. The valves effectively contain the conveying line pressure within the system, and frequent batching allows for a continuous flow of material at the conveying line’s discharge.
Quickly Moving Material
During one particular job, the system allowed Vac‐It‐All to move and distribute 29 tons (26 tonnes) of rock in just over three hours. “It normally would have been an all-day process to move this much rock,” Settlemoir says. “Employing equipment that will facilitate project completion is key to our success. The supplier provided reliable components for the specialized equipment we developed, which helped improve our customer services.”