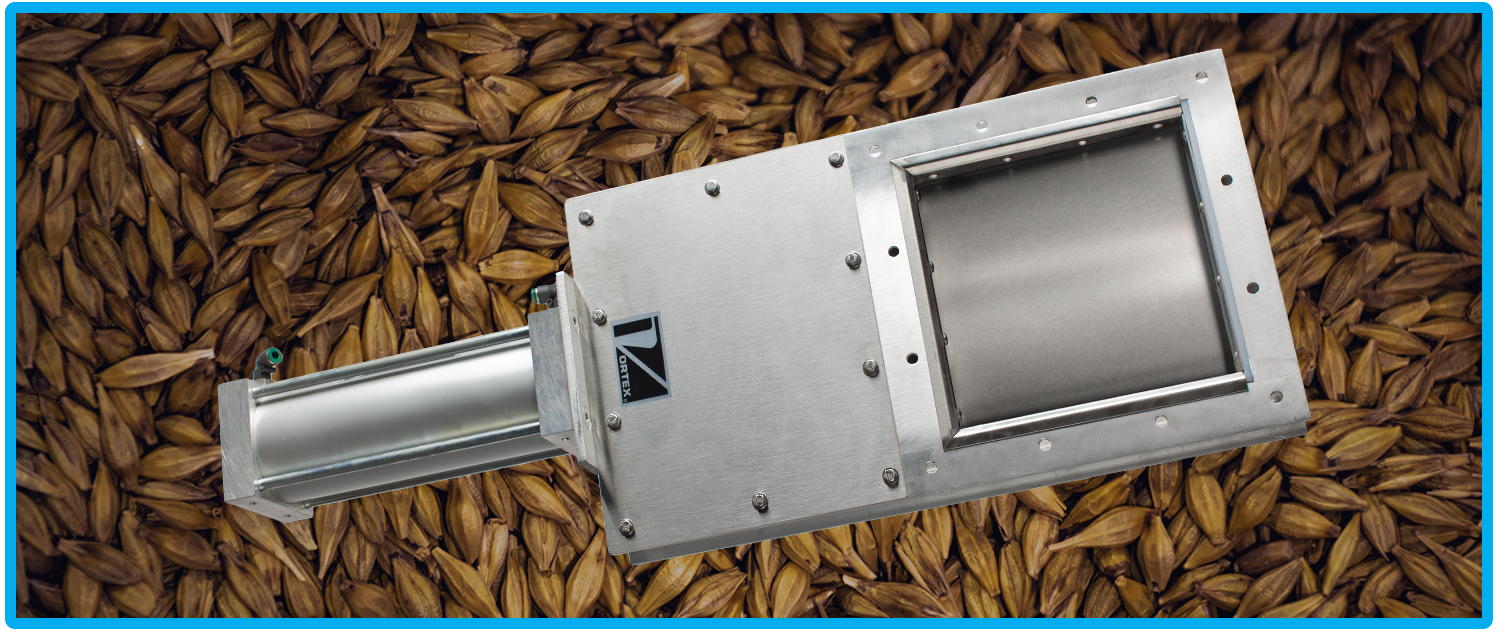
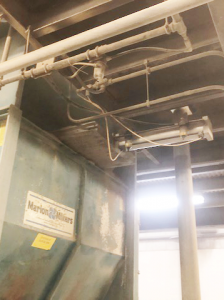
In 1996, Vortex worked with Alltech, an animal health company in Kentucky, to assist with the handling of grain at their facility.
Application:
The client’s specifications include:
- Blade & seal retainers constructed from 304 stainless steel
- Contact areas constructed from 304 stainless steel & polymer
Results:
Since their installation in 1996, these Vortex Roller Gates have required very limited maintenance other than the replacement of a set of bonnet seals on one of the gates.
“After 24 years of service, we needed to pull one of the gates as it began leaking around the seal,” said Robert Stuart, Maintenance & Facilities Manager at Alltech. “After dismantling the valve, we were awestruck on how well it looked and held up over the past 24 years as our products are abrasive and have severely worn down many other pieces of equipment over the years.”
The Vortex Roller Gate is designed with several replaceable parts, including blade, clevis, internal seals and retainers, actuator, position indication switches, and more. If a slide gate is maintained and operated as recommended, these mechanisms should be the only wear parts. In many cases, this maintenance-friendly design has allowed Vortex slide gates to remain in service for many years – and sometimes, even decades.
Features:
In addition to its prolonged service life, the Vortex Roller gate offers many benefits, including:
Wear Compensating
Bonnet seals constructed from hard polymer and “live-loaded” with compressed rubber backing. This ensures that as the polymer experiences frictional wear from many cycles over time, the rubber load seals continuously force the seal plates against the sliding blade. In doing so, the gate is able to self-maintain its dust-tight seal without frequent maintenance intervention.
Performance
On each opening stroke, the Roller Gate’s bonnet seals act as squeegees, forcing any materials remaining on the blade to fall away into the process line below, rather than migrating into the bonnet area. This prevents actuation issues associated with material build-up in the bonnet area.
In-Line Maintenance
Along the lateral aspects of the gate are two bonnet seal access doors. Both doors are removable using only simple tools. Once the doors are removed, new upper and lower bonnet seals can be driven into the port while the worn seals are simultaneously ejected out the other side.
After many actuations over time, frictional wear between the Roller Gate’s sliding blade and the gate’s hard polymer side seals may also lessen its sealing effectiveness across the blade. Rather than removing the gate from service to replace its side seals each time, the Roller Gate features cam-adjustable rollers. Using only simple tools, the rollers can be rotated upward to “lift” the blade back into position and restore the compression between the blade and side seals.