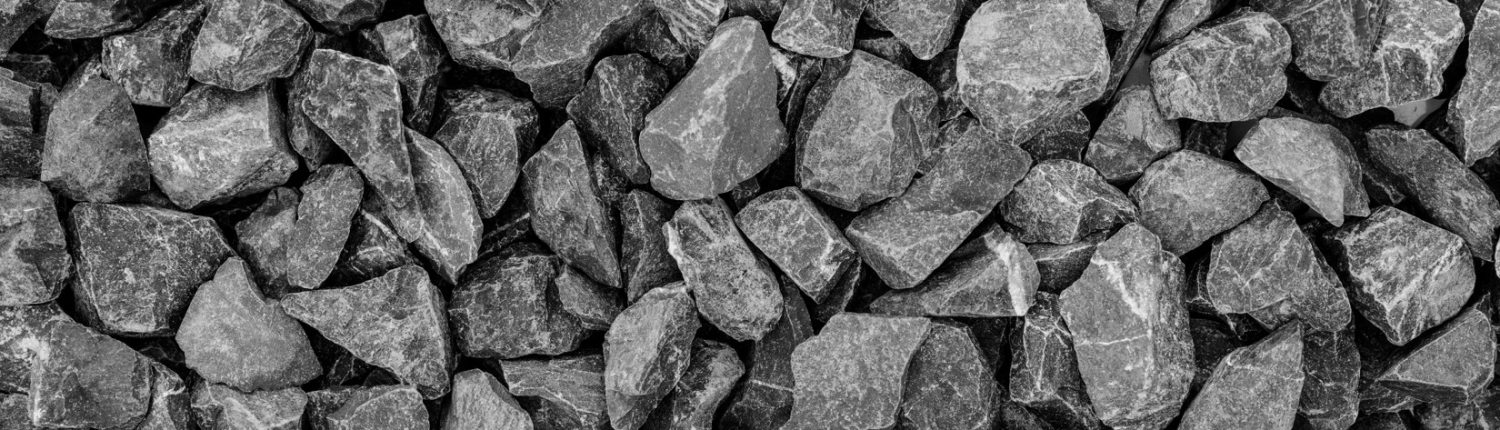
Client:
Quantity:
Size:
Application:
In 2013, an iron ore mining company consulted Vortex® to discuss a processing need. At the time, the client was using a flop gate to divert iron ore fines from a single source toward two destinations. Because of iron ore’s hardness, the flop gate was ill-designed to handle wear and abrasion caused by the handled material. This resulted in frequent need for maintenance. To solve this issue, the client sought a replacement diverter with increased durability and longer service life in particularly harsh environments.
Given the unique scope of the client’s application, Vortex recommended a special-engineered diverter valve. To accommodate the client’s request for added abrasion resistance, and to ensure proper match-up within the client’s existing footprint, many modifications in the diverter’s construction were necessary.
Features:
- Large size. This diverter has 36 x 36 in (915 x 915 mm) openings; is 7 ft 9 in (2.36 m) tall; and weighs 4,100 lbs (1,860 kgs)
- Curved, bucket-style blade. By designing the diverter with a curved, bucket-style blade, it allows iron ores to collect in the curvature and abrade upon themselves, rather than continuously abrading upon the diverter’s internal mechanisms.
- “Rock box” liners. By designing the diverter with “rock box” liners along the blade and along the bottom of the off-leg chute, it allows materials to accumulate in open areas along the blade and along the bottom of the off-leg chute. Once the openings are filled, iron ores will impact upon themselves as they pass through the valve, rather than continuously coming in contact with the diverter’s mechanical parts.
- Abrasion-resistant liners constructed from AR 400 BHN carbon steel. The purpose of abrasion-resistant liners at the diverter’s inlet is to protect a valve’s material contact areas and other wear points from continuous blast abrasion. Vortex abrasion-resistant liners are replaceable so that the diverter can be well-protected over time.
- Straight leg diverting design. With conventional “Y-type” diverters, abrasion and wear can be a concern because as materials flow through the inlet, they can make direct impact where the legs meet. With the straight leg option, a straight-through channel is created so that materials can suspend, which lessens material impact against the diverter’s internal mechanisms. Also with the straight leg design, the area where the two outlet legs meet is shielded from the direct path of material flow, which lessens wear and abrasion in that area.
- Customized removable access doors. This diverter features two side access doors on both sides of the straight-thru leg & one removable access door on top of the off-leg. Both side access doors are designed to the exact shape of the bucket blade so that it can be removed, if necessary. As a standard, all Vortex gravity diverters are designed with one removable access door at the front of the valve. By designing a diverter with removable access doors, it allows internal inspection and/or maintenance to be performed without removing the diverter from service.
- Lifting lugs. Because of the diverter’s large size, lifting lugs allow the valve to be safely and easily installed by lifting it into place using large machinery.
- Two double-acting air cylinder actuators. This provides the required force for the bucket blade to actuate properly when handling heavy materials.
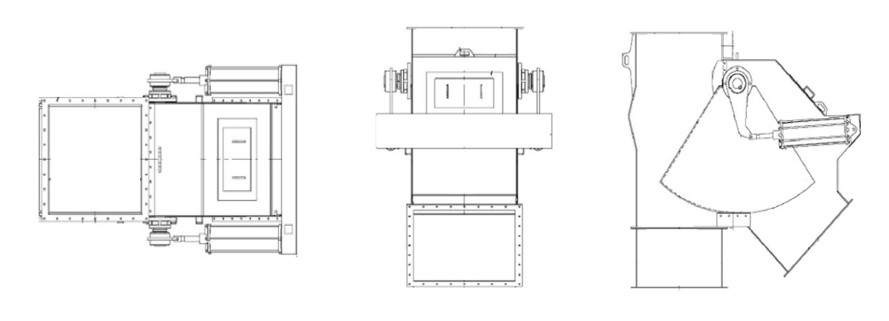