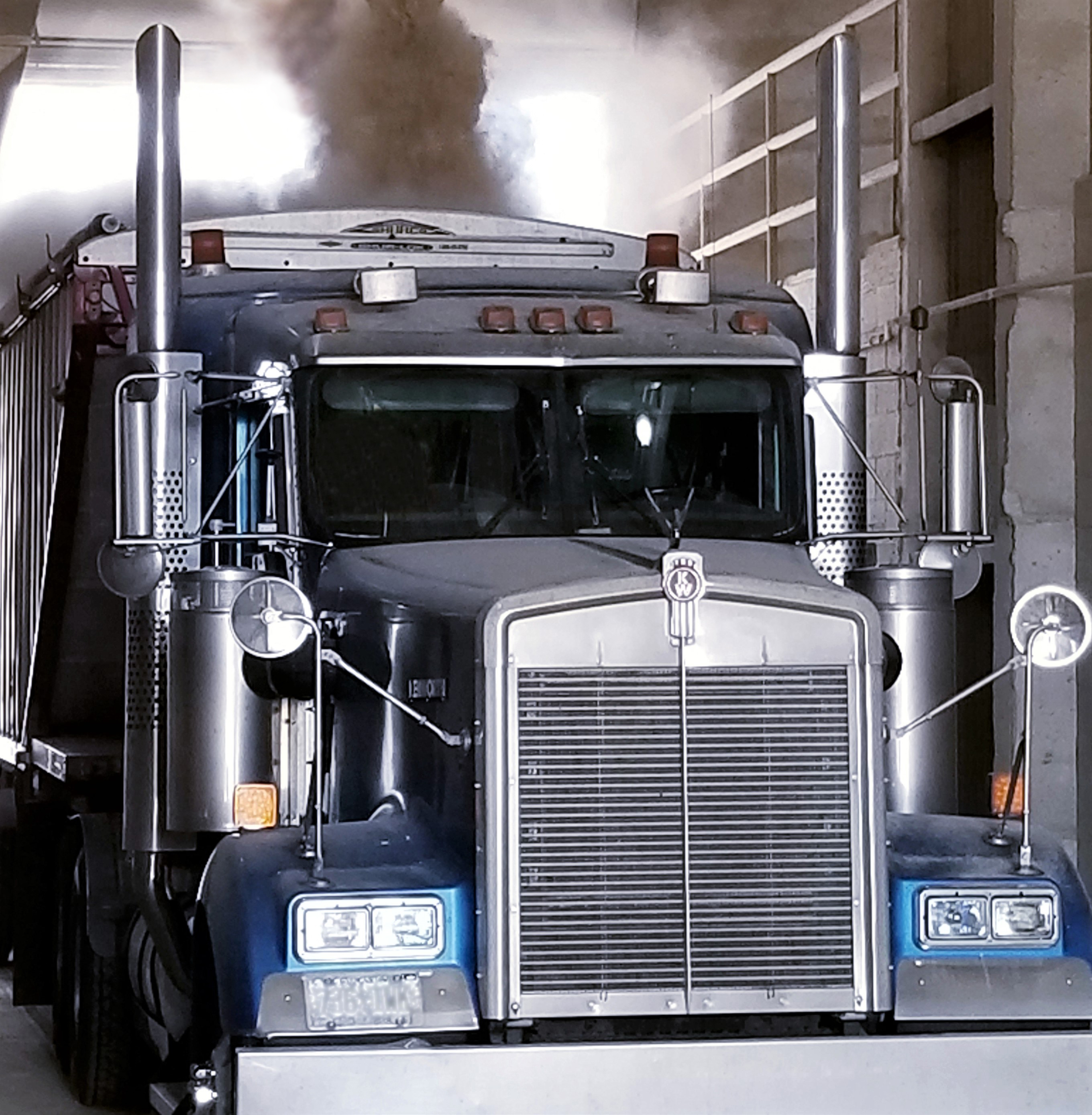
Client:
Quantity:
Size:
Application:
Instead of routing dust to a collector, a better alternative is routing dust into a filter unit.
As featured in Rock Products
by Kevin R. Peterson
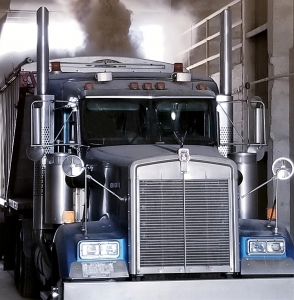
The loading of dry bulk material can create hazards.
The loading of dry bulk materials into trucks and rail cars for transport is known to create dust. As many of these airborne particles are potentially hazardous, they are regulated by different federal agencies.
Under the Clean Air Act, the US Environmental Protection Agency (EPA) sets limits on what quantities of certain air pollutants can be in the air anywhere in the United States. Additionally, other federal agencies like the Occupational Safety and Health Administration (OSHA), the National Institute for Occupational Safety and Health (NIOSH), and the Mine Safety and Health Administration (MSHA) have established guidelines and regulations of acceptable dust emissions for specific materials.
Airborne dust creates a hazard to human health, safety, and the environment:
Health issues – Inhalable dust particles have the potential of getting trapped in the nose, mouth, and upper respiratory tract. As such, certain materials may contribute to breathing difficulties, diminished lung function, hospitalization, respiratory issues, and weakened immune systems.
Safety issues – Airborne dust that eventually settles on railings and walkways becomes a safety hazard. In the past, gloves were included as a part of Personal Protection Equipment (PPE) to protect workers from skin exposure chemicals, heat, cold, and abrasive objects. More and more companies are requiring rubber coated gloves as PPE that will allow a firmer grip when traversing dust coated stair railings to prevent slipping and falls.
Environmental issues – Dust particles have the potential of changing the nutrient balance of river basins, contributing to acid rain effects, damaging forests and agricultural crops, and depleting soil nutrients, to name a few. Additionally, businesses and neighborhoods abhor dust created from nearby sources.
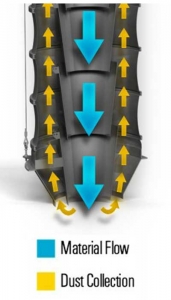
Loading of dry material into trucks and rail cars is accomplished in various ways. Typically the material is stored in a bin or silo located above the loading area. A slide gate at the bottom of the bin is opened and material flows through a tube, chute, or dust sock into the receiving container. Factors present during the loading process – including material handled, moisture content of material handled, falling distance, loading rate, environmental considerations, and type of vessel being loaded – present dust generation issues. Tubes, chutes, and socks are not designed to capture fugitive dust.
Telescoping spouts are vertically adjustable and bridge the distance between the material holding bin and the receiving container. The spout consists of a number of stackable cones surrounded by an outer sleeve or sheath. The cones direct the flow of material and address material wear. The outer sleeve provides containment for the material – protecting material from the environment as well as protecting the environment from the material.
The loading spout can be equipped with a port at the top of the spout that allows dust, created during the loading process, to be withdrawn via vacuum and routed up, through the spout (in the open area between the cones and the outer sleeve) to an external dust collector. Vortex Global, headquartered in Salina, Kansas, offers a preferred alternative to dust collectors – the Vortex Filter Unit.
The Vortex Filter Unit is installed above the telescoping spout. Instead of routing dust to a collector, the dust is routed into the Filter Unit. Here is how it works:
Initially, conveyed material passes from the bin or silo, through an independent tube, through the Vortex Filter Unit (1) and into the Vortex Telescoping Loading Spout that is mounted beneath the filter.
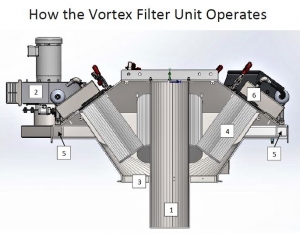
A centrifugal fan (2) creates a negative air suction that draws dust, generated during the loading process, up through an open area into the spout (between the cones and outer sleeve) and into the Filter Unit (3). Additionally, the fan exhausts clean air into the atmosphere.
A series of pleated filter cartridges (4) temporarily trap the accumulated dust.
High-pressure, compressed air is supplied to the Filter Unit through a special chamber that encompasses the unit (5). A nozzle, located inside the filter box (6), connects to the compressed air chamber. A timed, systematic blast of air is individually directed into each of the filter cartridges (4) – freeing dust from the cartridge.
The emancipated dust is suspended within the body of the Filter Unit until the loading process is finished. The vacuum is turned off and a final filter cartridge “clean out” purge is performed.
The accumulated dust is pushed down, through the spout, and into the load.
Simplified maintenance of filter cartridges has been addressed by installing clamps at the top of the hinged filter boxes. No special tools are required to replace the filter cartridges.
Keep in mind that the Filter Unit is NOT a dust collector. Instead of collecting dust that will later be disposed of, the Filter Unit allows the dust material to be captured, re-entrained into the load, and sold as product. Not only does the Filter Unit address problems created by air pollutants, it adds profitability to the loading process.
About the author
Now in his 25th year with the company, Kevin R. Peterson is the Business Development Director for Vortex Global. A board member of the Industrial Minerals Association of North America, Kevin travels extensively to meet with customers and customer prospects. He has created and shared hundreds of case studies and written numerous articles that share the successes Vortex products have experienced with industries that handle and process dry bulk material.