Client:
Quantity:
Size:
Application:
By its simplest definition, dilute phase conveying is described as “low pressure, high velocity” material movement. Oppositely, dense phase conveying is characterized as “high pressure, low velocity” material movement.
If material characteristics and application parameters permit, dilute phase conveying is often preferred because it can be more energy efficient and can improve process efficiencies by conveying materials at higher rates of speed. However, many considerations must be made when designing a dilute phase pneumatic conveying process.
This article will address just a few of the many considerations that must be made before selecting valves to divert or converge dry materials in dilute phase.
Dilute vs. Dense Phase Pneumatic Conveying
Dilute phase pneumatic conveying is primarily used when processing more stable dry materials. Common examples include plastics, flour, calcium carbonate, grains, and hydrated lime powder, among others.
Alternatively, dense phase pneumatic conveying is often used to move more friable dry materials, such as pet food. By transporting such materials at low velocities, there is less risk of degradation as materials move through the convey line. In addition, dense phase pneumatic conveying is often used when handling highly abrasive materials. By moving abrasive materials at lower velocities, it reduces wear to elbows and other components in the convey line.
Particle Size of Handled Material(s)
Particle size – and particularly, fine materials – can impact the overall build of a diverter valve. When handling fine materials, a full-flanged, sealed-body build is necessary to prevent fine materials and dusts from escaping to atmosphere.
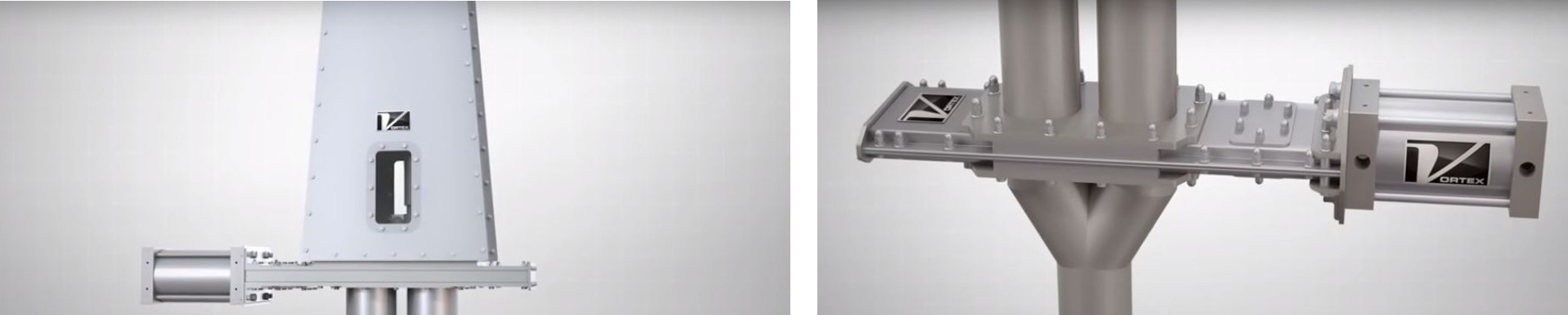
Convey Line Pressures
All Vortex diverters for pneumatic conveying are designed to handle pressures up to 15 psig | 0.1 MPa | 1 barg), depending on valve size. Because dilute phase is characterized by low pressure, this pressure rating is often sufficient for a diverter’s application. However, for higher convey line pressures – that being, those closer to the 15 psig | 0.1 MPa | 1 barg threshold – it is advised to equip the diverter with an air purge assembly:
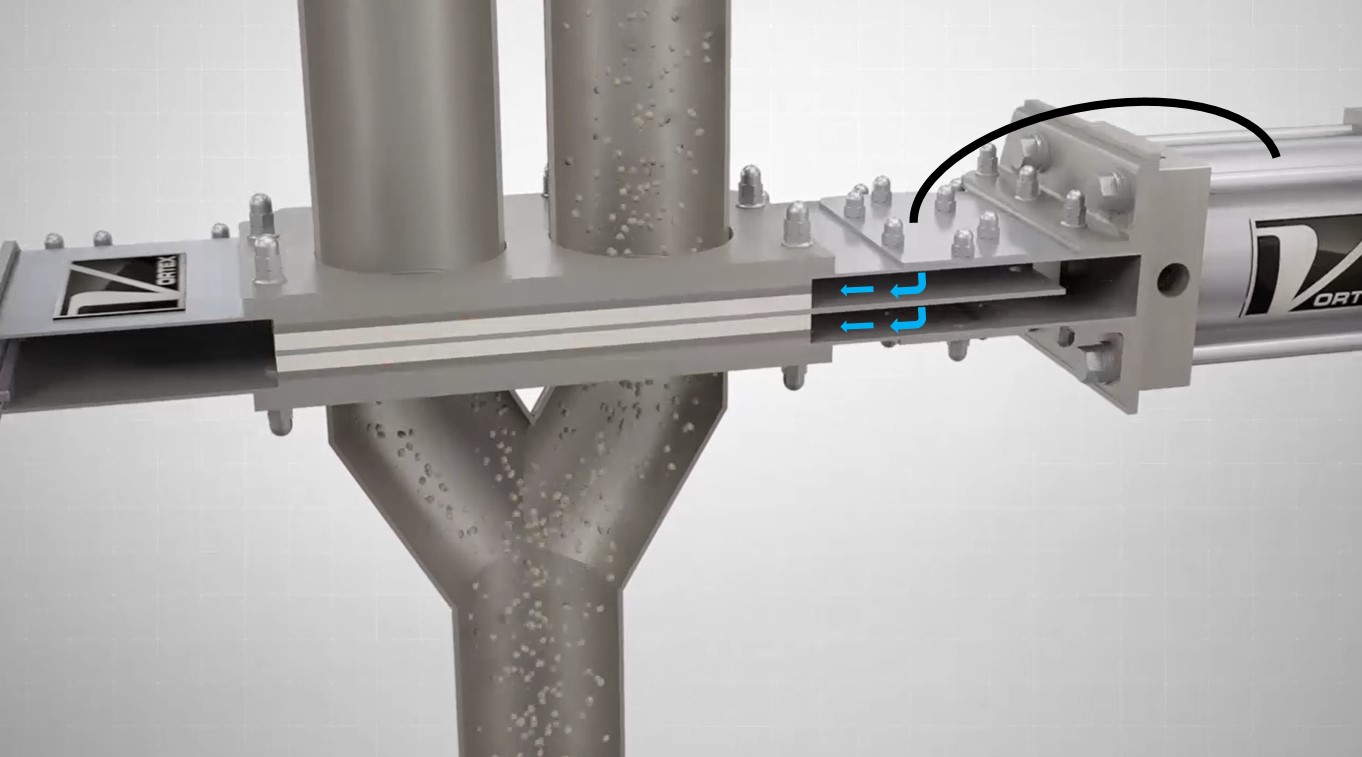
By doing so, the air purge neutralizes any differential pressure that may result from the diverter’s capabilities being challenged. This keeps materials in the flow stream, hindering them from migrating into the valve body.
If convey line pressures significantly exceed 15 psig | 0.1 MPa | 1 barg, one option may be to arrange Vortex® HDP Gates™ or Vortex® Titan Pressure Valves™ (TPV) as process gates used to divert or converge materials:
The HDP Gate is designed to handle pressures up to 75 psig | 5 barg, depending on gate size, while the TPV is designed to handle pressures up to 100 psig | 6.8 barg, also depending on gate size.
Contact us to determine which product is most suitable for use in your pneumatic conveying process.
Number of Sources & Destinations
Vortex diverters for pneumatic conveying are commonly built with one inlet and two or three outlets. Because the diverters can be oriented in either direction, this allows material flow from one source toward up to three destinations, or from three sources toward a single destination.
Need more than three sources or destinations?
If space is available, Vortex diverters for pneumatic conveying can be stacked to accommodate additional channels. This is most common with the Vortex® Wye Line Diverter™:
Vortex® Fill Pass Diverters™ can also be stacked so that multiple materials can fill into a common weigh hopper:
Replacement to Hose Manifold Stations
If a process requires many sources flow toward many destinations, the Vortex® Multi-Port Diverter™ is an ideal solution to reduce overall footprint:
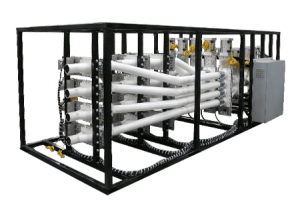
Multi-Port Diverters are often used to replace hose manifold stations and improve process efficiencies through automation.
Available Space
Some Vortex diverters, such as the Wye Line Diverter, are benefitted by having a narrow profile. This allows easy installation within most new and pre-existing systems. Other Vortex diverters, such as the Flex Tube Diverter™, are challenged by limited space installations. This is because the Flex Tube Diverter features a large housing to protect the diverter’s internal flexible hose. As hose length increases, so too does the diverter’s overall height.
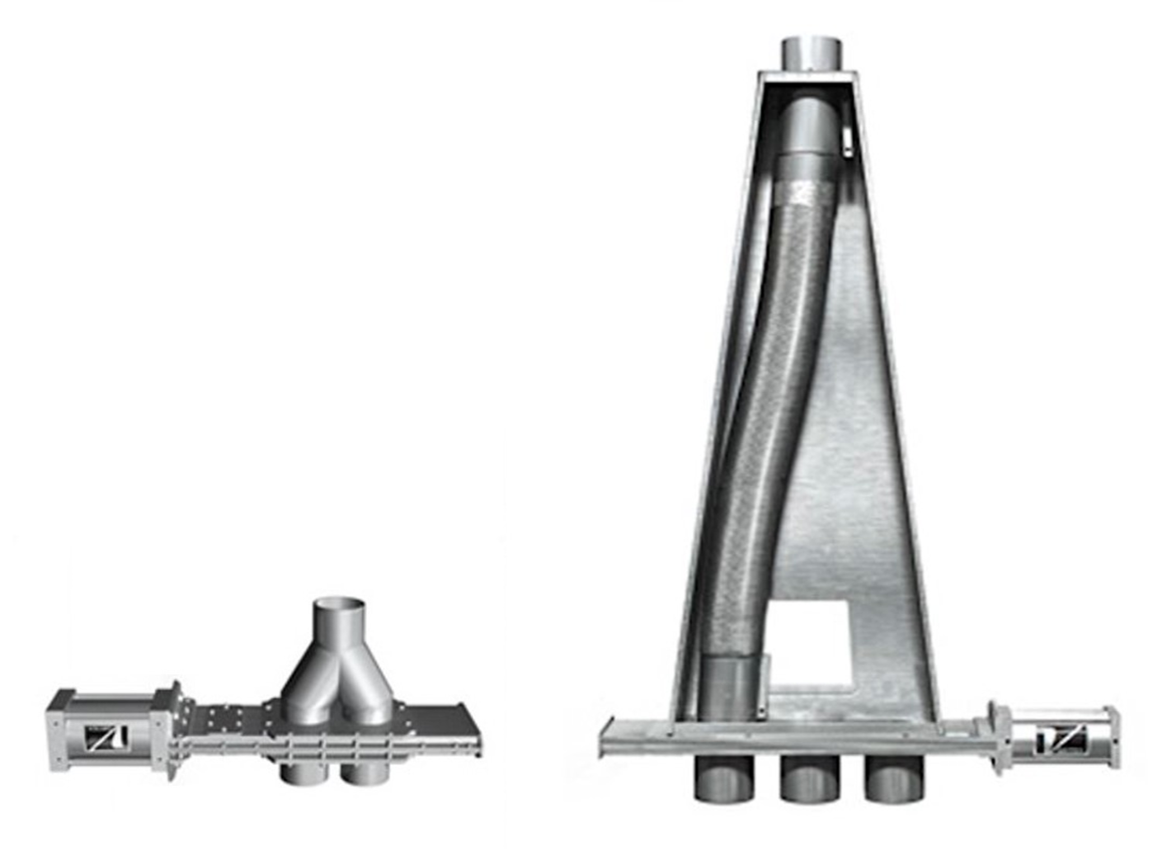
Considerations for Materials of Construction
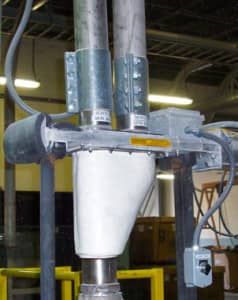
Depending on material type, characteristics can range from non-abrasive to extremely abrasive. This concept is further challenged when handling dry materials in dilute phase, as similar materials can react very differently depending on system setup. For this reason, maintenance engineers are primarily concerned with valve longevity and maintenance frequency. The best way to prevent these concerns is to construct a valve from high-quality, durable materials.
Vortex utilizes several materials of construction to best equip a valve for success in its specific application. Especially in harsh pneumatic conveying environments, Vortex offers many techniques for preventing wear and abrasion.
Considerations to be made regarding materials of construction include:
- Need for abrasion- or corrosion-resistance, and how this impacts selected metal type & other modifications. Vortex offers several grades of aluminum, 304 and 316L stainless steel, and carbon steel, among others. For added abrasion-resistance, the Vortex Wye Line Diverter can be wrapped with ceramic backing (right). Contact us to discuss other modifications.
- Whether the diverter will be installed outdoors or in a wash-down environment, and how this impacts selected polymer type. The purpose being that when exposed to moisture, nylon has a tendency to swell. If swelling is significant, this can put undue stress on the valve’s blade and cause actuation issues. Alternatively, PET polymer does not swell, which eliminates this concern.
- Required ratings & certifications – such as FDA, CE, ATEX, etc.
- Handled material temperatures. As a standard, Vortex products are capable of handling material temperatures up to 180°F (82°C). Modifications are available to handle material temperatures up to 400°F (204°C). For especially high-temperature applications, Vortex TPVs may be installed as process gates used to divert or converge. Because the TPV has no polymer seals, it is capable of handling material temperatures up to 660° F (350° C).
- Convey line size. Some Vortex diverters for pneumatic conveying can be built with larger bores than others. Contact us to discuss options or modifications that can be made to accommodate size requirements in your process.
Which Diverter Should I Choose?
While each diverter discussed above is an excellent option to pneumatically convey dry materials in dilute phase, it is critical to first consult with industry experts prior to making a valving decision. With so many variables to consider – and countless others left unmentioned – it is of utmost importance to first gather expert knowledge, to ensure your selection is truly the best solution for its application.
With more than 300 years of combined experience in the dry bulk solids industry, clients can be assured Vortex application engineers will listen to your needs and rely on in-depth knowledge of dry solids to develop the right solution for even the most demanding applications.
For more information on Vortex diverters for pneumatic conveying, or to discuss your material handling needs, please contact us.