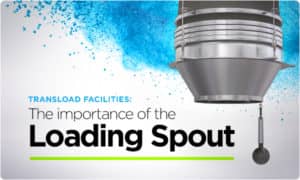
Client:
Quantity:
Size:
Application:
Originally published in World Cement
Transloading, the process of utilising different shipping methods to transport and deliver material, makes incredible sense in the cement industry. In the case of cement manufacturers, transloading offers distinct advantages.
When shipping material longer distances, manufacturers are able to reduce freight costs by utilising less expensive rail freight to deliver material to further away destinations and then utilise 3 for local delivery. It is a cost effective way to move and store material closer to the targeted destination. No longer is a manufacturer locked in on having to ship material from a single point of origin to different locations. Transload storage locations can be set up to allow manufacturers to address potential markets from numerous points of origin. In doing so, manufacturers can broaden their customer base or more effectively service larger customers.
Opening up the option of manufacturing to supply multiple points of origin creates efficiencies at the main manufacturing facility. As new points of origin are targeted and established, stepped expansions may be made at the main facility to accommodate the increased demand - rather than considering the enormous cost of new manufacturing plants. Companies invest in transload facilities to satisfy product demand in a certain area and hopefully create a profit. To be profitable, the facility must offer not only a quality product, but also a quick loading time and address individual personal safety expected by the truck drivers that pick up material at the facility. These items become major considerations.
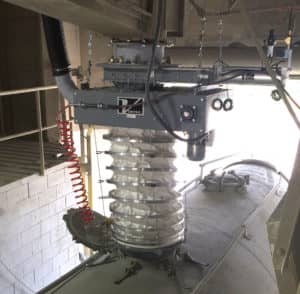
For many reasons, the one piece of equipment that comes under the most scrutiny at the facility is the piece of equipment that deposits cement into the truck – the loading spout.
Loading spouts were created to address many factors involved in the loading process. First and foremost, the telescoping ability of the spout allows placement directly into an open container. The telescoping ability addresses the fact that truck heights vary.
Spouts are available with positioners that allow movement through a single or a dual direction. This option further addresses the ability to position the spout directly into truck container hatches. Proper positioning establishes an optimal material flow pattern through the spout, minimises wear, and creates favourable spout life cycle costs. Additionally, the combination of the spout's telescoping and positioning ability creates labour savings costs in not having to hire employees to perform these tasks.
In earlier days, cement was conveyed through an open spout or sock directly into the truck. Clouds of dust were formed in the loading bay as airborne contaminates create potential hazards including skin allergies, eyesight problems, lung disease, and accidents associated with slipping or falling from dust accumulation on floors, walkways or ladder rungs.
Because of the hazards associated with the handling of dry cement, facility operators are required to maintain clean loading areas where potential exposure to dust may create issues for employees, contract workers, or truck drivers who are present at the facility. An advantage of the telescoping loading spout is its ability to trap and remove dust particles before they escape and become airborne.
The loading spout addresses many of the safety and environmental issues present at transload facilities. A fabric outer sleeve encompasses the retractable loading cones. A vacuum is set up within the sleeve. Fugitive dust created in the loading process is transported through the spout to a central dust collector.
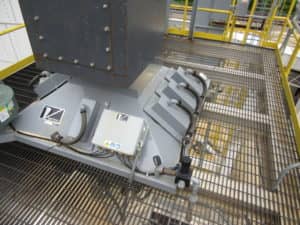
Integral dust filters were eventually designed to capture fugitive dust emitted during loading instead of getting rid of it. The product is deposited back into the material flow during the loading process. This filtration system aids in preventing material waste and greatly increases overall profitability.
The time it takes to load individual trucks at transload facilities is an important factor. Loading a cement truck requires three stops: safely accessing and opening the top hatches, spotting the truck and loading the cement, and safely accessing and closing the top hatches. Customers always like to see their drivers turn as many loads as possible during their shift. Larger, more efficient loading spouts offer faster loading times to accommodate more loads per day. Faster loading offers cost efficiency for the companies hauling the loads as well as for the facility itself.
Many newer facilities now offer local clients 24-hour access to the facility with pre-approved key cards. This service allows loading when facility personnel are off duty. Inside the loading bay, the driver utilises a computer screen that allows him to load a pre-determined amount of dry cement. It also allows the drivers to utilise a spout positioner for direct loading of cement into the truck when the driver is not perfectly parked. Twenty-four hour access extends the hours of operation and is another cost efficiency for both customers and the facility.
Facility managers realise the importance of their loading spout and how it can easily bring joy or irritation to them. Not only do they address the above-mentioned safety, profitability, and loading issues, they must consider costs relating to equipment maintenance and downtime.
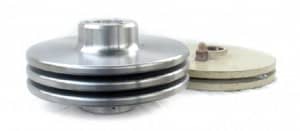
Vortex understands reliability issues relating to retractable loading spouts, offering two spout features specifically suitable for transload facility managers. Vortex's proprietary 4-cable lifting design provides maximum stability and more lifting torque compared with standard two- or three-cable systems used on standard loading spouts. Should one cable of a two- or three-cable spout break from wear or premature trucker pull away, it is unusable until repair is made. Should one cable on the Vortex 4-cable spout break, the spout is still operational while waiting for repairs. Vortex's three-piece, CNC-machined pulleys feature rounded edges and precision cable grooves that significantly reduce cable wear and backlashing as the spout extends and retracts.
Maintenance personnel that have experienced cable fry and failure will relate to the fact that continual cable repair creates tremendous downtime and maintenance cost issues, as well as upset truckers waiting for repairs to be made before they can load product.
Utilising a loading spout that promotes employee and driver safety, that adds to a facility's profitability, and does not constantly create maintenance and loading issues is extremely important for a transload facility. Equipment dependability and reliability are key components for facility operators who are responsible for creating and maintaining the overall success of their operation. Manufacturers like Vortex are important resources for these facilities.