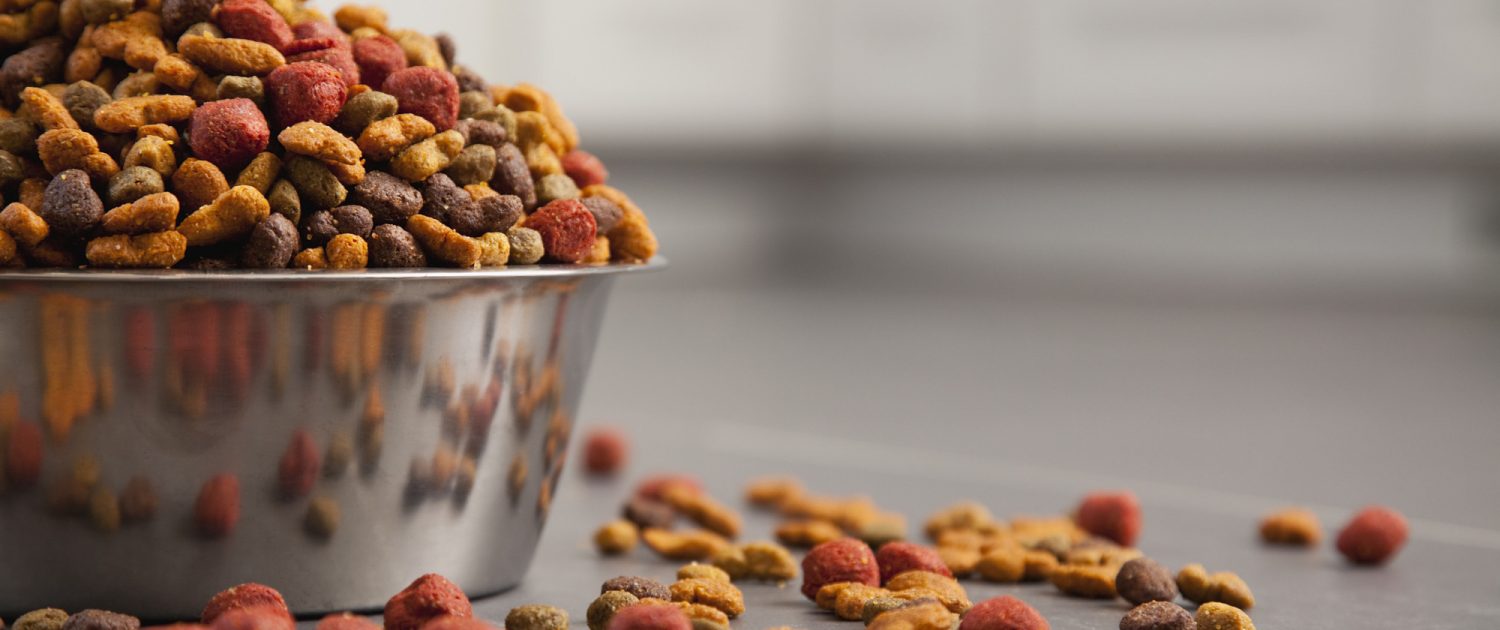
Client:
Quantity:
Size:
Application:
Features:
- Straight leg diverting design.
- Diverter body constructed from 304 stainless steel with 32 Roughness Average (RA) finish.
- Blade constructed from 304 stainless steel with 32 RA finish.
- Material contact constructed from electropolished 304 stainless steel.
- Continuous welds throughout the diverter.
- Standard removable front access door, with a second access door along the diverter’s straight leg.
- Locking mechanism for the secondary access door, for safety protocol.
Result:
In order to meet evolving sanitary demands from customers and the Food & Drug Administration (FDA), this global pet food company sourced five Vortex Seal Tite Diverters for use in one of its production facilities. All five diverters were built using a two-way, straight leg design. They were also built with a square inlet and outlets to match the client’s pre-existing footprint.
The client specified 32 RA finish, electropolishing, and continuous welds throughout the diverter to ensure a smooth path of travel for material flow (Figure I). All three of these processes lessen the surface rigidity of raw stainless steel. In doing so, material particles and dusts have less opportunity to collect in ridges along the steel’s surface. These methods further reduce the likelihood of in-line contamination and spoilage.
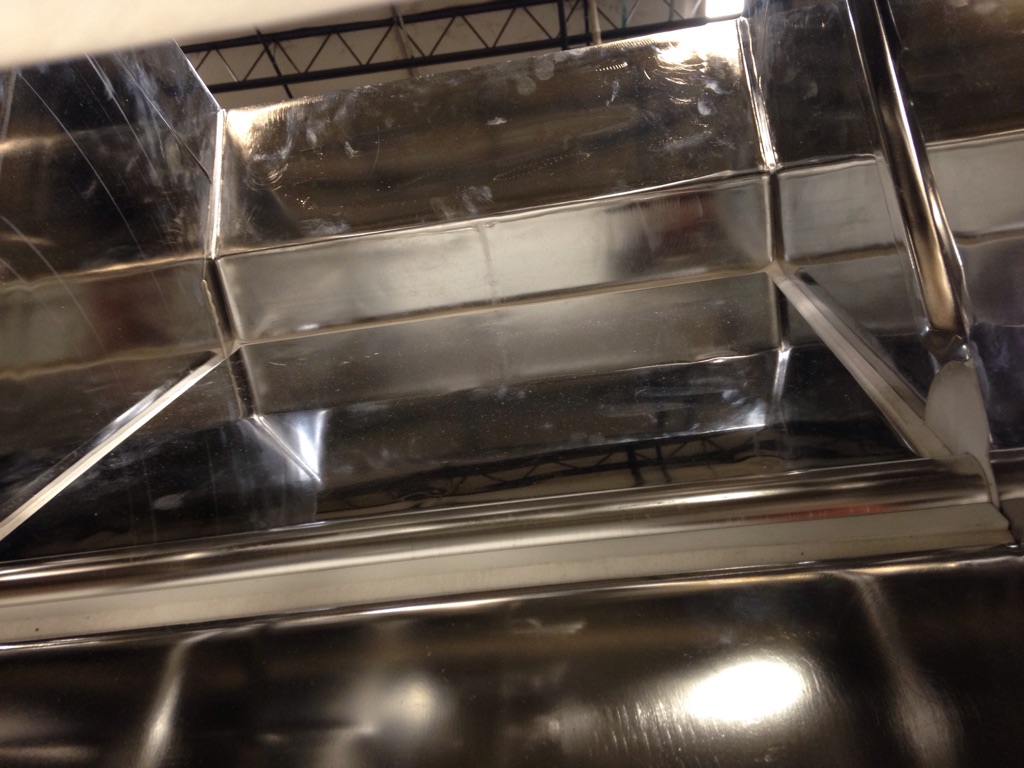
Typically, Vortex Seal Tite Diverters feature only one removable access door at the front of the diverter. In this case, the customer specified a second access door be made along the diverter’s straight leg, in addition to the diverter’s standard removable front access door (Figure II). For safety purposes, the secondary access door also has a locking mechanism that disables the diverter if the door is open. These features allow better access to the diverter’s internal, so that frequent wash-downs can be accommodated and further ease can be brought to in-line maintenance.
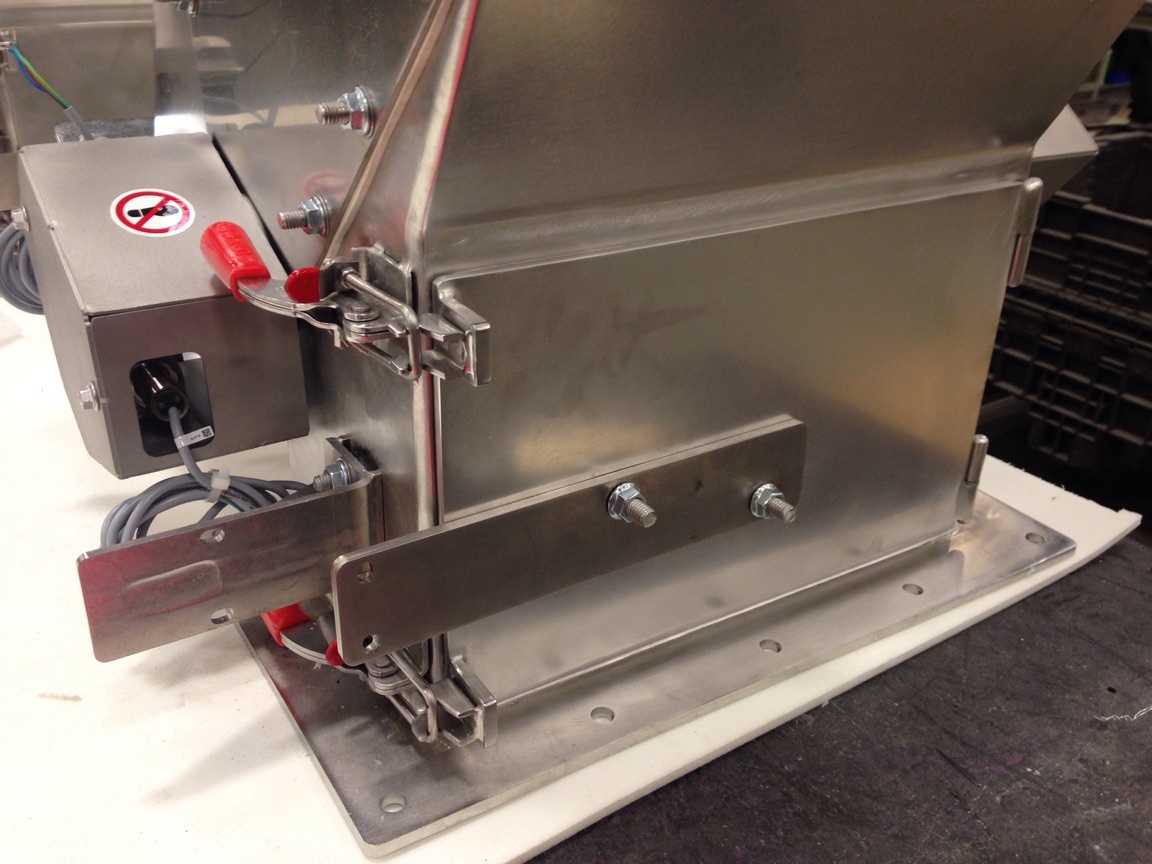
To meet FDA guidelines, integral seal bars were welded inside the diverter (Figure III). As a standard, seal bars are bolted inside the diverter, rather than welded. When bolted, small crevasses remain between the seal bar and the diverter body, leaving areas where material particles and dusts can collect and spoil. The purpose of integral seal bars is to solder these crevasses closed, as a technique to eliminate areas where materials can collect.
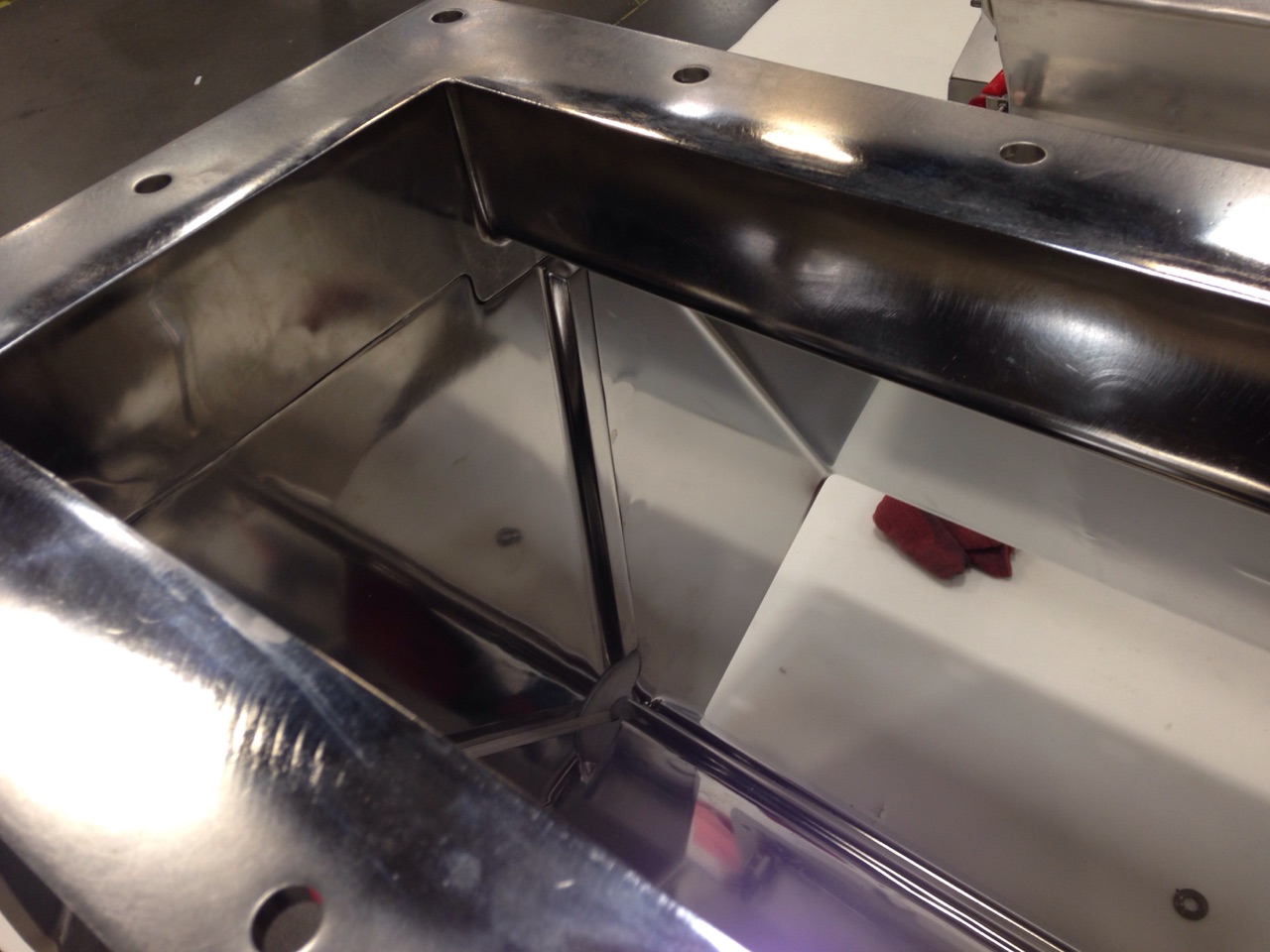
All five diverters were installed in May 2017. Since then, the client has been so satisfied with the diverters’ operations that orders for additional units have been approved. If units from the second order prove to be equally satisfying, the client plans to source similarly designed Vortex Seal Tite Diverters for use in all of their production facilities. The client’s reason for doing so is to create uniformity in their production processes.