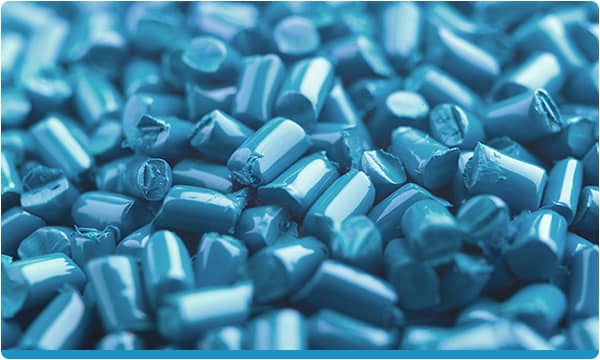
Client:
Food-grade plastic bags and packaging producer
Quantity:
Size:
Size: 8 in | 205 mm
Application:
Divert hot, sticky plastic pellets from a receiving hopper into either of two process lines.
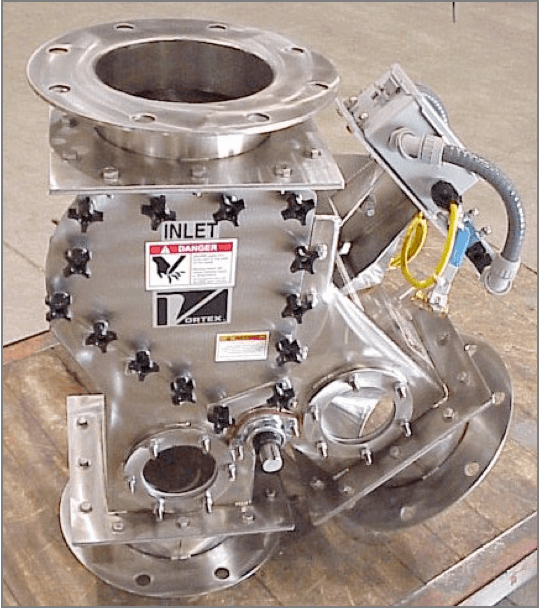
Features:
- Designed with food-grade Viton rubber vane seals.
- Florisant 207 shaft seals were used to accommodate the 450° – 500° F | 230° – 260° C temperatures present.
- Custom viewports at each outlet leg. Through these, maintenance personnel make regular checks during the day to see if a sticky build up is occurring inside the diverter. Once buildup occurs, the viewport is removable so that the diverter's interior can be cleaned. Cleaning of one outlet leg can be performed while pellets continue to transfer through the opposite outlet leg. Because of this, there is virtually no downtime once production begins.
- Removable access panel at the front of the valve allows interior access for blade and seal maintenance or replacement, or for a more thorough clean-in-place procedure.
Results:
The client was in search of a solution for a problematic application. Diverters previously utilized were problematic in the fact that they had to be removed from service and cleaned frequently. Downtime was a major expense.
After reviewing the application, The Vortex engineering team determined a Seal Tite Diverter could be modified, engineered and manufactured to meet many application criteria, in order to provide the best solution to the client's needs.
The client credits Vortex for making their operation much more efficient and profitable. Easy access and cleanliness made the Seal Tite Diverter a problem solver for this manufacturing process.