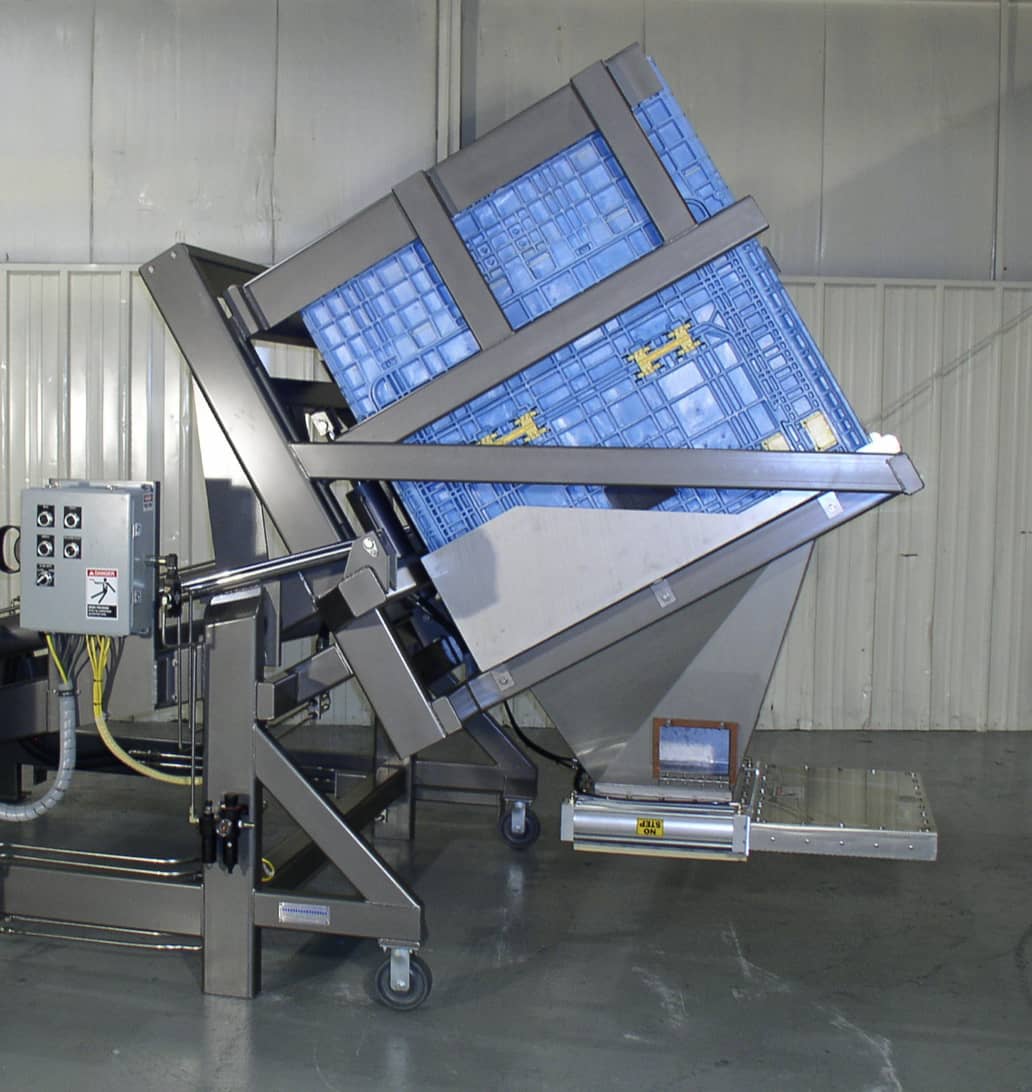
Client:
Material Transfer & Storage – Allegan, Michigan, USA
Quantity:
Size:
Application:
Containers filled with brownie and cake mixes are dumped into stationary hoppers. The hoppers feed packaging equipment. Gates were necessary beneath the dumper pour hoods.
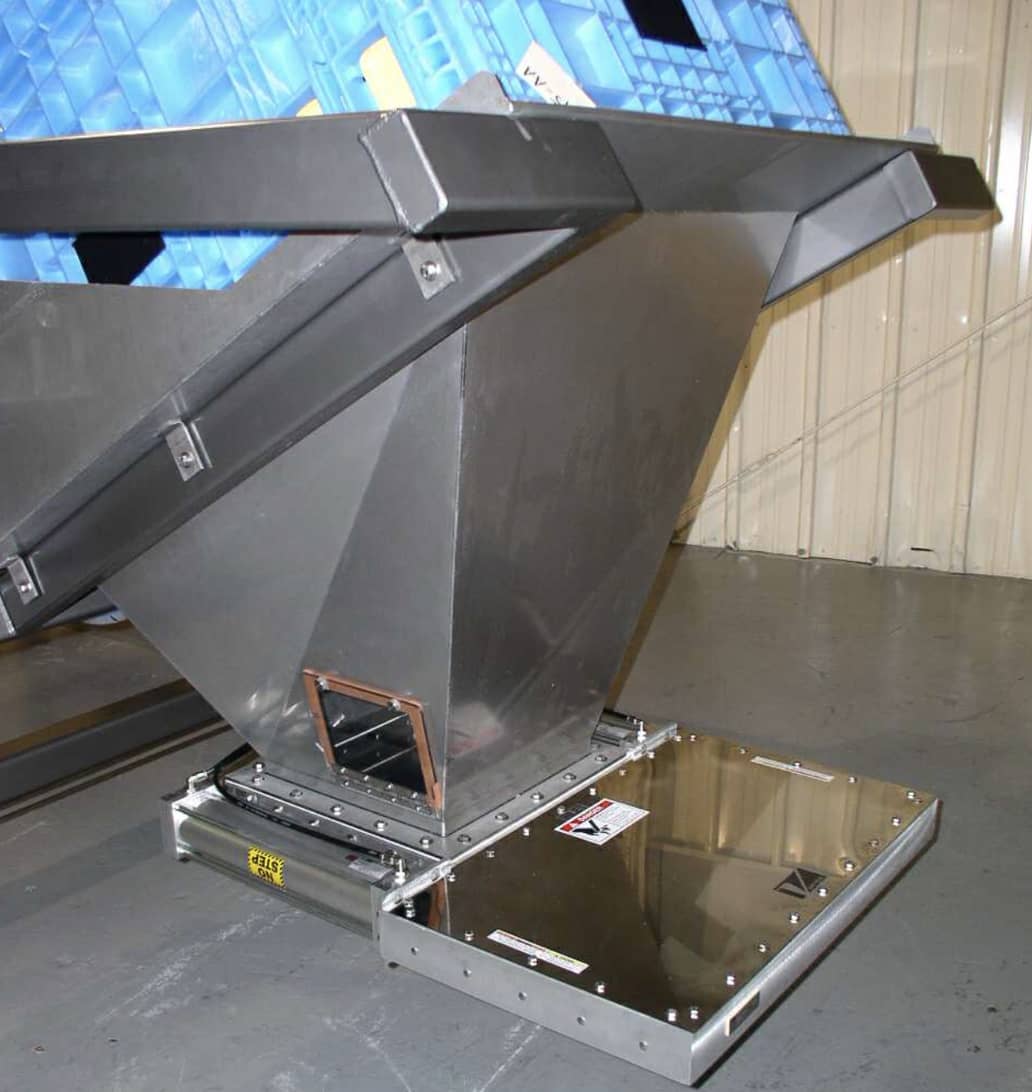
Features:
- A dual cylinder design was specified because it provides a shorter overall gate length and its weight is centered at the discharge.
Challenge:
The client was seeking replacement equipment. The existing equipment leaked materials between the container, the dumper pour hood and the pour hood's discharge valve. This resulted in product waste and clean-up. A forklift was used to load materials into the dumper, which was slow and increased cycle times.
Results:
The Roller Gate was chosen due to its narrow profile, positive material shut-off and dust-tight seal. Since installing the dumpers, the client now has a cleaner operation with no product waste. The unit's floor-level loading also greatly reduces cycle times.