
Client:
Quantity:
Size:
Application:

Nobody has to tell you that having a clean working environment is important. Material leakage into the factory’s atmosphere raises issues with health, safety, environmental, and explosion hazards. Plant profitability also suffers as material on the floor is considered waste. In your processing system, don’t let slide gate valves be the source of your material leakage problems.
Vortex makes gates that are designed to keep your factory clean. It comes from Vortex’s patented Sealing Technology™ that has evolved over the past 35 years and used by processing facilities all over the world. From foods to minerals and plastics to textiles, keeping your factory free of material dusting caused by leaking valves is a major priority for Vortex.
The fundamental difference between Vortex’s designs from your typical slide or knife gate is quite simple: Vortex valves are designed for handling DRY materials. Many valves used in dry bulk processing utilise soft elastomers to create the seal between the internal process and the factory atmosphere. When handling dry materials, these valves suffer from major sealing problems as material wears through the seals on every actuation.
Slide gates with elastomer seals have been used for years in dry bulk handling applications. They are often simple and affordable products that over a short period of time can provide a solution. All slide gate seals are exposed to either blast abrasion as product flows through it or frictional abrasion during each open and close cycle. Any seal mechanism in a slide gate must stand up to the constant wear and tear by the dry material handled. If the seals and seats are made of any type of Teflon, PTFE, Buna-N, or rubber based elastomer, the valve is highly susceptible to frequent leakage and shorter maintenance cycles.
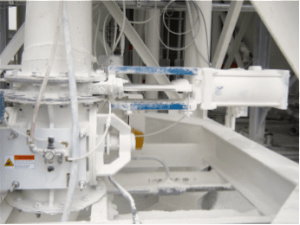
Vortex valves are equipped with Vortex’s Sealing Technology™ to combat the issues of ordinary slide gates. For starters, Vortex uses hard polymer for their seals instead of soft elastomer. Nylon, PET, or other hard polymers are more suited for dry materials because of its durability and ability to hold a long-lasting seal over high cycle rates. Vortex’s hard polymer seals have a strategically placed compressed rubber backing that decompress as the polymer wears, in other words, the seals are “wear compensating”. This applies constant force against the blade creating a positive seal of fine dust and powders and keeping your factory clean with minimal maintenance over time.
Vortex utilises a wide range of seals for food grade applications, as well as, other parameters, such as; high/low temperature, chemical compatibility, abrasion resistance, and functionality. Our experienced Technical Application Team is dedicated to ensuring every seal is compatible with your process.