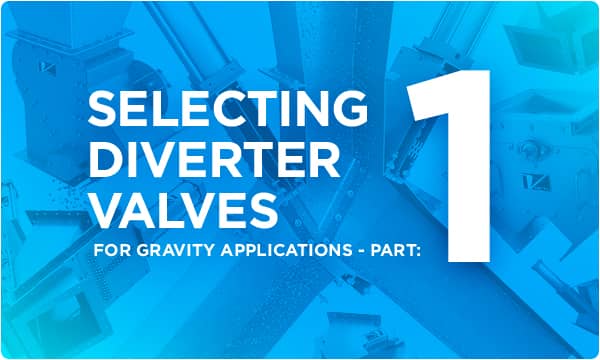
Client:
Quantity:
Size:
Application:
When you browse through Vortex’s product catalogue, you may notice a wide variety of standard and engineered diverters for gravity flow applications. This is not by accident or due to the fact that we love to design multiple products that achieve the same result! This article covers the differences between multiple diverters and address factors that impact selection, based on application.
To be clear about the term “gravity flow," Vortex defines it as an application where air pressure or vacuum is not used to assist material conveyance. The primary factor that drives the selection of a gravity diverter is the particle size and/or abrasiveness of the material handled. Another driving factor is the bore size of the valve required.
Vortex manufactures six types of diverters that are suitable for handling material in gravity flow:
- Seal Tite Diverter
- Gravity Vee Diverter
- Flex Tube Diverter
- Aggregate Diverter
- Titan Lined Diverter
- Pivoting Chute Diverter
As a three part series, this initial article will cover the Seal Tite and Gravity Vee Diverters.
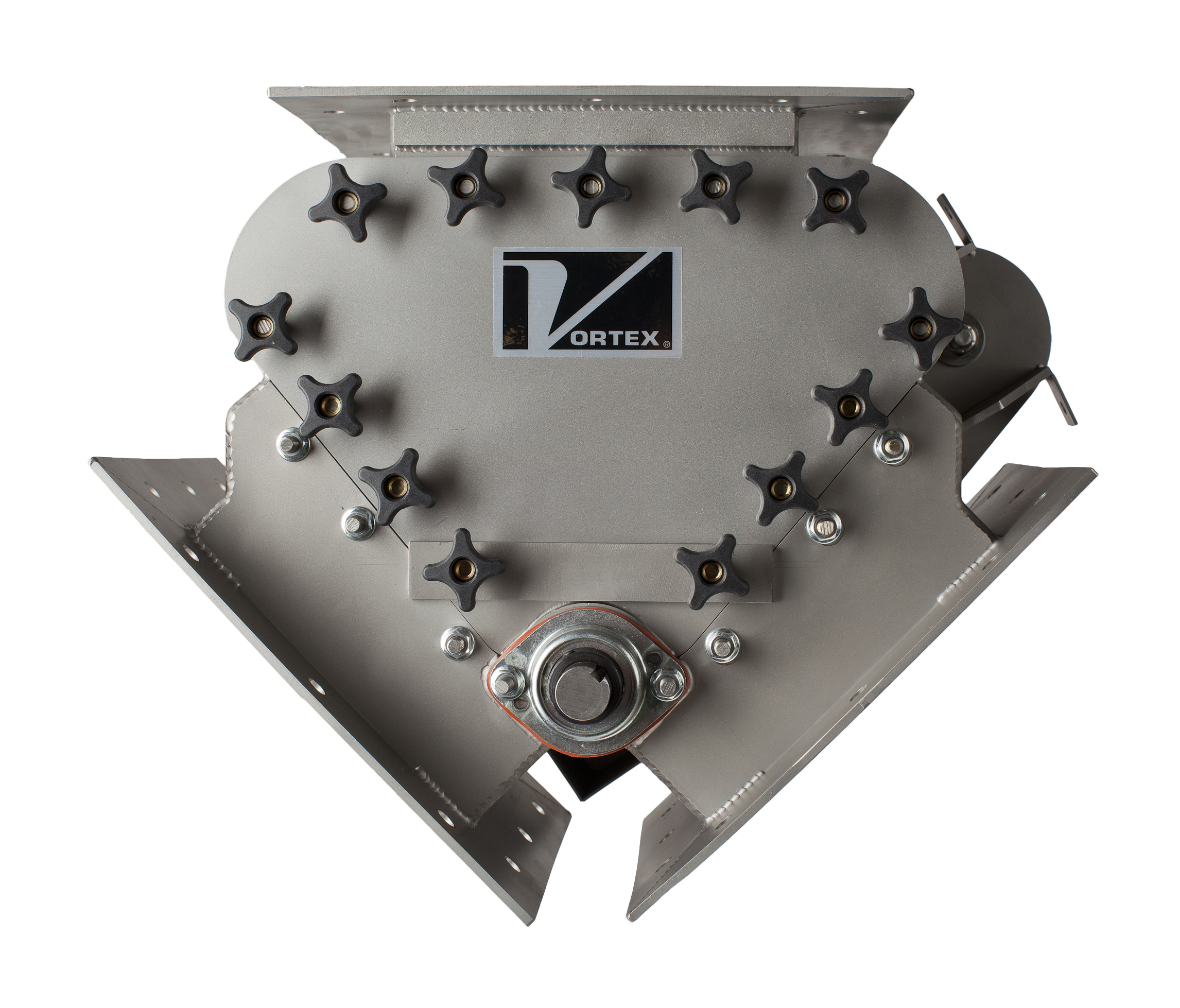
Seal Tite Diverter
Seal Tite diverter differentiates itself from a traditional “flap type” diverter, which is the most common diverter in the industry for use in gravity applications. It utilizes an interior, angled blade that diverts the flow of material from one source to two destinations. The Seal Tite diverter can be used for a wide range of nonabrasive to moderately abrasive materials with particle sizes as small as 50 to 75 microns. It is ideal for plastic, food, chemical, and agricultural applications that require a dust tight seal to minimize cross-contamination.
Vortex’s Seal Tite Diverter is engineered to channel the flow of material away from the leading edge of the flapper vane. This feature is critical to maintain seal integrity and inhibit material leakage across the closed legs of the valve. While other flapper diverters may leak past the vane shaft and trap material underneath, the two-way Seal Tite includes live-loaded, polymer shaft seals to eliminate this problem. The two-way Seal Tite also comes with a removable access port for easy inspection of the valve’s internal components or for easy replacement of the seals and blade without removing it from the conveying line.
Compared to other diverter configurations, the Seal Tite can be built in very large sizes. Vortex’s standards go up to 750 mm | 30 in, but have been engineered to over 1500 mm | 60 in bores sizes.
Gravity Vee Diverter
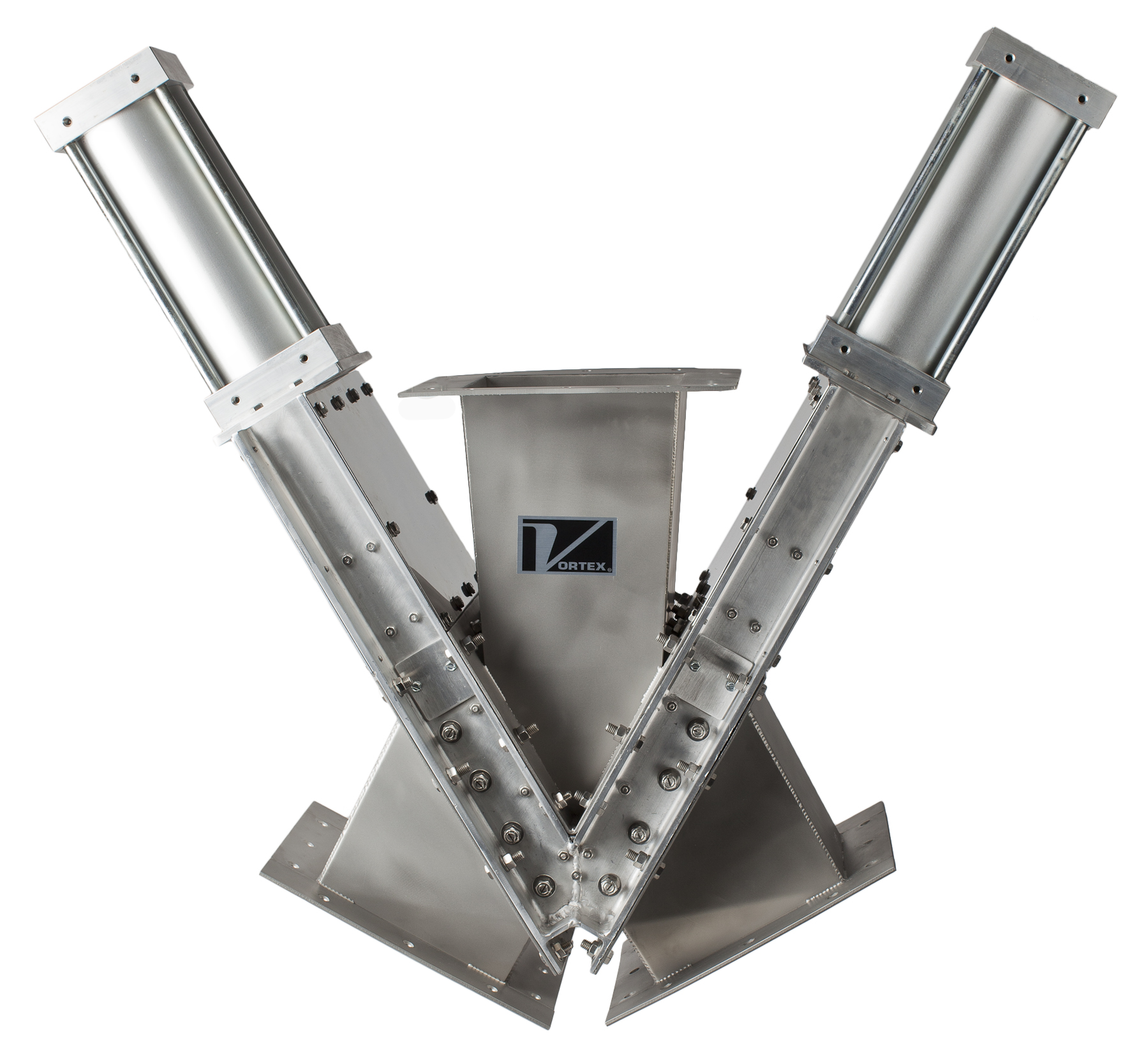
The Gravity Vee Diverter is a unique design that offers several advantages and capabilities that “flap type” diverters do not. For example, the Seal Tite Diverter can direct flow in one direction versus another, but cannot shut off flow or allow material to be diverted in two directions simultaneously. The Gravity Vee’s design provides more versatility and reduces the need for an additional “shut off” gate above it.
The Gravity Vee incorporates two Vortex Roller Gates that are welded together at an angle. This allows the operator to divert material in one or two directions and completely stop flow when required. If positioning controls are incorporated in the actuation package, the Gravity Vee can effectively control the flow rate through either leg simultaneously.
Another advantage of the Gravity Vee is its sealing capability. For finer powders and dusts, the diverter can seal materials with particle sizes down to 10 micron and can adequately contain low pressure nitrogen blankets within the system with the appropriate modifications.
From a maintenance perspective, the Gravity Vee is easily maintenanced in service. The hard polymer bonnet seals are replaceable via two lateral access ports, allowing a maintenance professional to install a new seal from the side of each gate. Actuators are also easily replaced without removing the valve from service, as the modular design allows easy access to the connections to the piston rod and blade.
Size is somewhat a limiting factor for the Gravity Vee Diverter. The footprint of the diverter often makes in impractical to fit into areas with limited space. Vortex’s standard size range goes up to 600 mm | 24 in bore sizes.