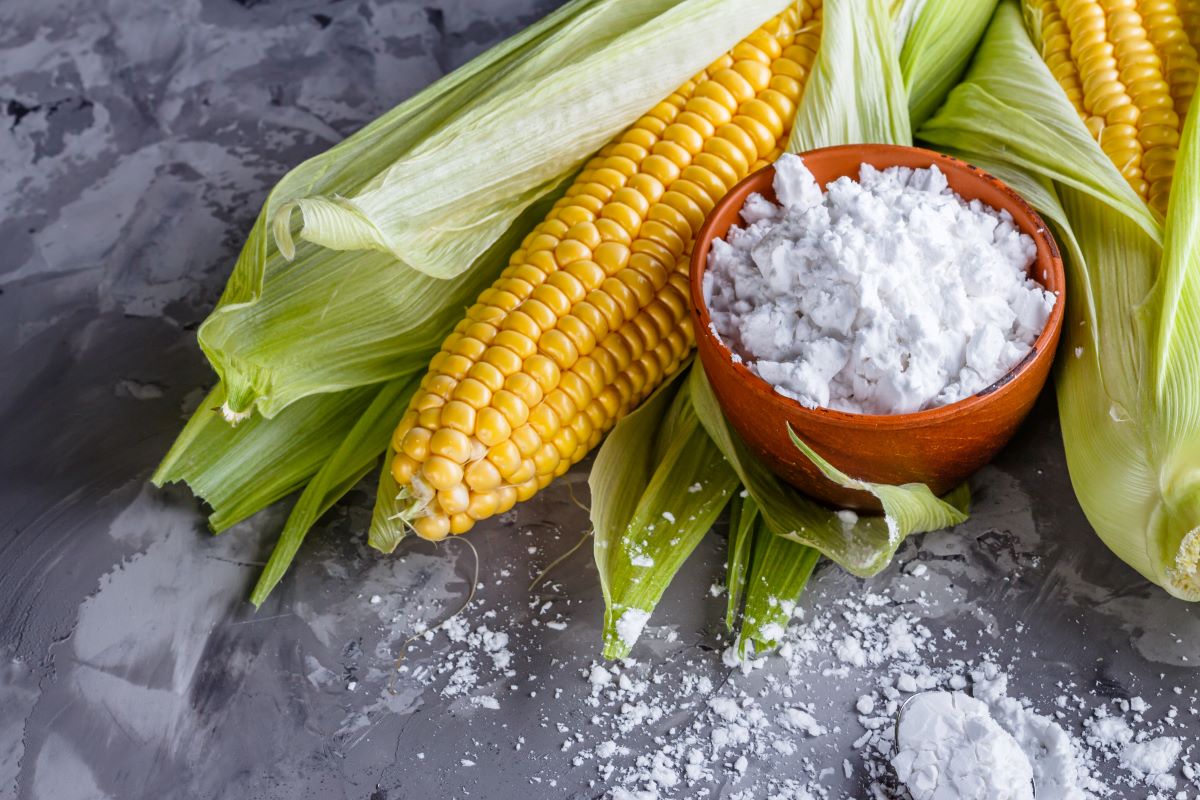
Client:
Quantity:
Size:
Application:
At this customer facility, starch manufacturing and handling—crucial for numerous food and beverage items—is getting an upgrade in precision and reliability. The starch production process commences with sourcing top-notch corn, subjecting it to a series of advanced refining methods. These steps involve milling to break down corn kernels and a separation process to isolate the starch. Post-separation, the starch undergoes further treatments, tailored based on the intended application, such as modification for enhanced performance in diverse settings. This manufacturers dedication to innovation shines through in how they customize starch properties to meet specific client requirements, be it for thickening, texturizing, or stabilizing products. This tailored strategy not only showcases the company's technical prowess but also its pivotal role in the food and beverage sector, continuously adapting to changing market demands.
The manual hose change process in material handling, particularly in extensive operations like those at this customer facility, poses several challenges affecting efficiency and safety. A primary concern is the time-intensive nature of manual changes, significantly slowing down production rates. Each change involves halting machinery, manually disconnecting and reconnecting hoses, and restarting operations—an error-prone process with potential delays. Moreover, the physical toll on workers conducting these manual exchanges is substantial, raising concerns about workplace ergonomics and employee well-being. There's also an increased risk of cross-contamination during material handling, as remnants from prior uses may mix if hoses aren't thoroughly cleaned between changes. This risk presents a serious hurdle in maintaining the high-quality standards vital in food and beverage manufacturing. Consequently, the need for automated, advanced systems to streamline material handling, reduce downtime, and uphold strict hygiene standards is evident.
Given the challenges outlined, the Vortex Multi-port Diverter emerged as the ideal solution, directly addressing issues linked to the manual hose change process. Its design facilitates smooth transitions between materials or production lines sans the need to halt machinery or engage in labor-intensive hose changes. This not only drastically minimizes downtime but also streamlines operations, boosting productivity and efficiency. The Vortex Multi-port Diverter enhances workplace safety and employee welfare by automating material switching, lessening physical strain, and reducing injury risks tied to manual tasks. Its automated system not only guarantees a safer work environment but also enhances employee contentment and operational efficiency. Discover more about the Vortex Multi-port Diverter or reach out to us today!
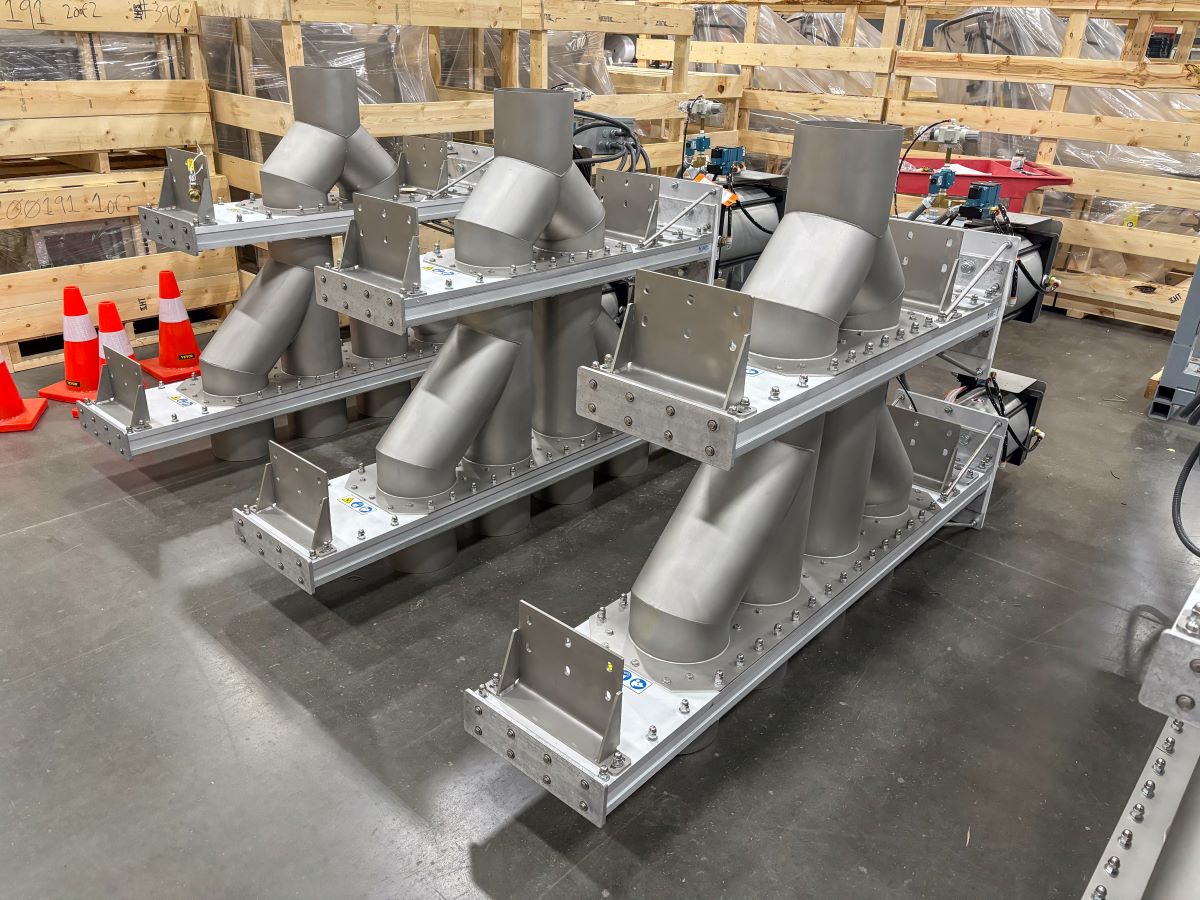
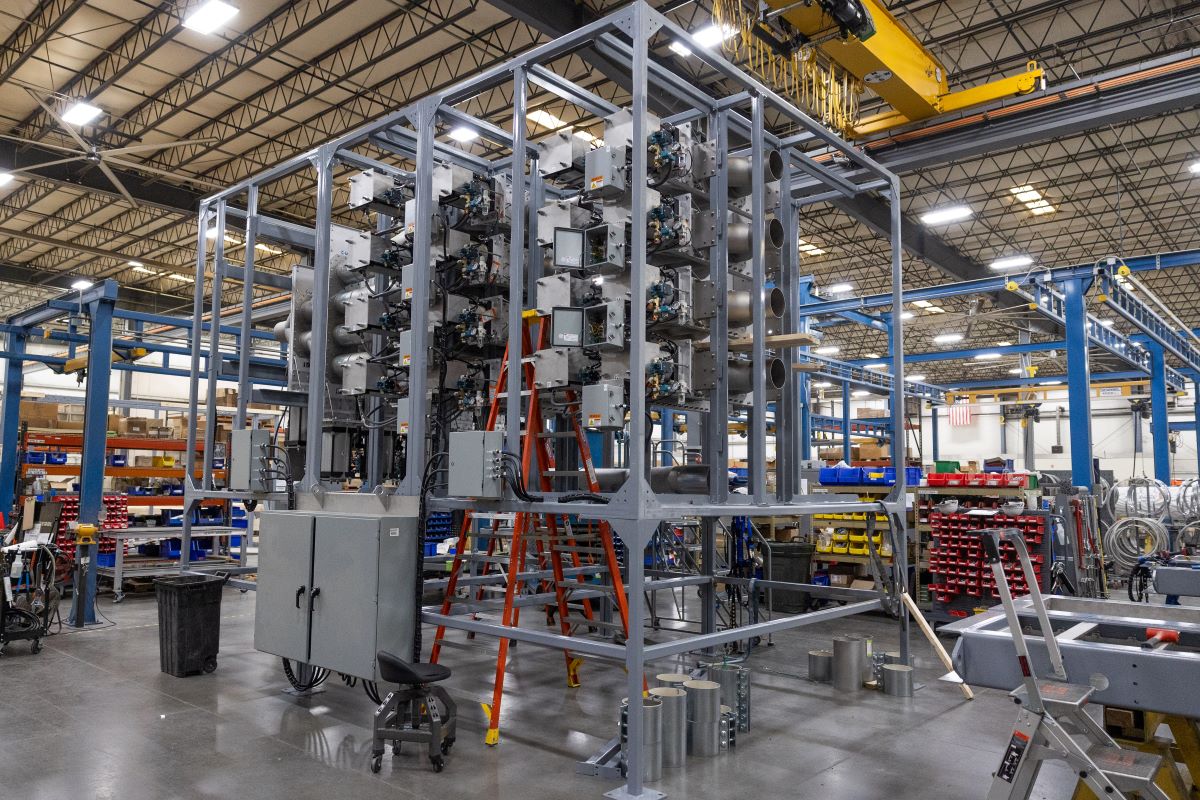
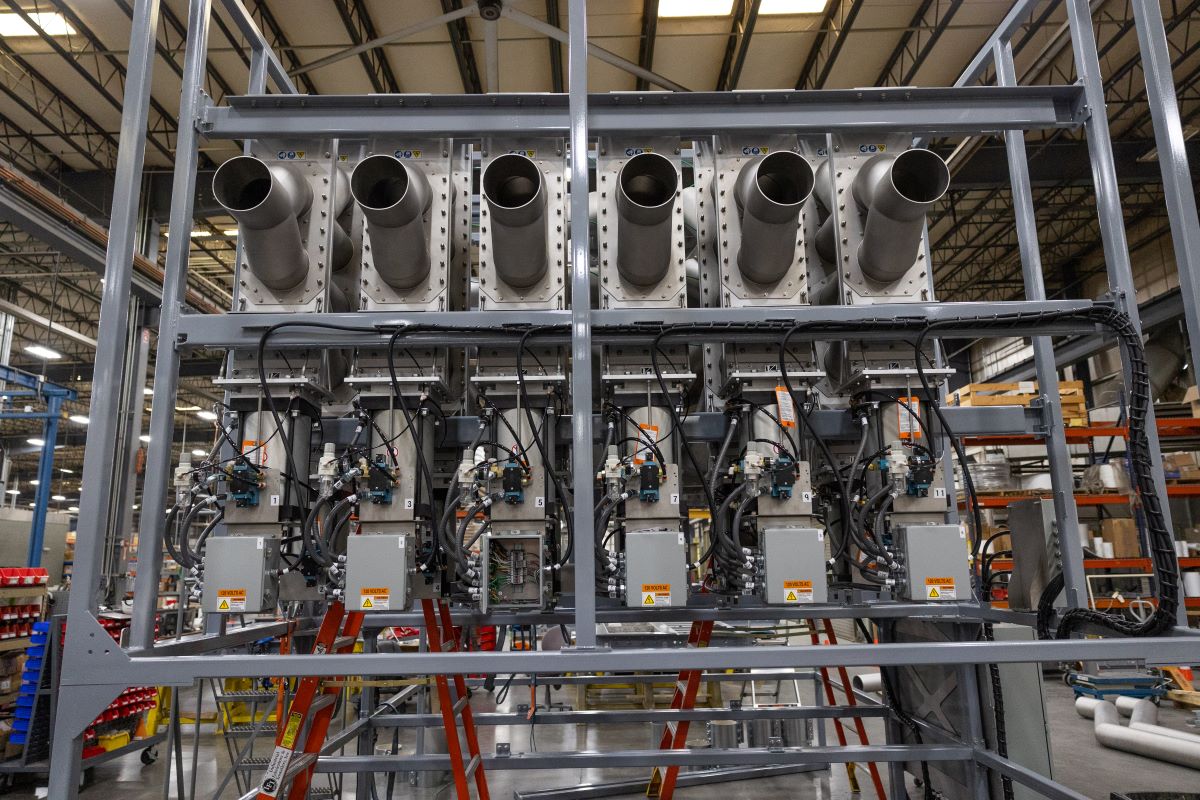
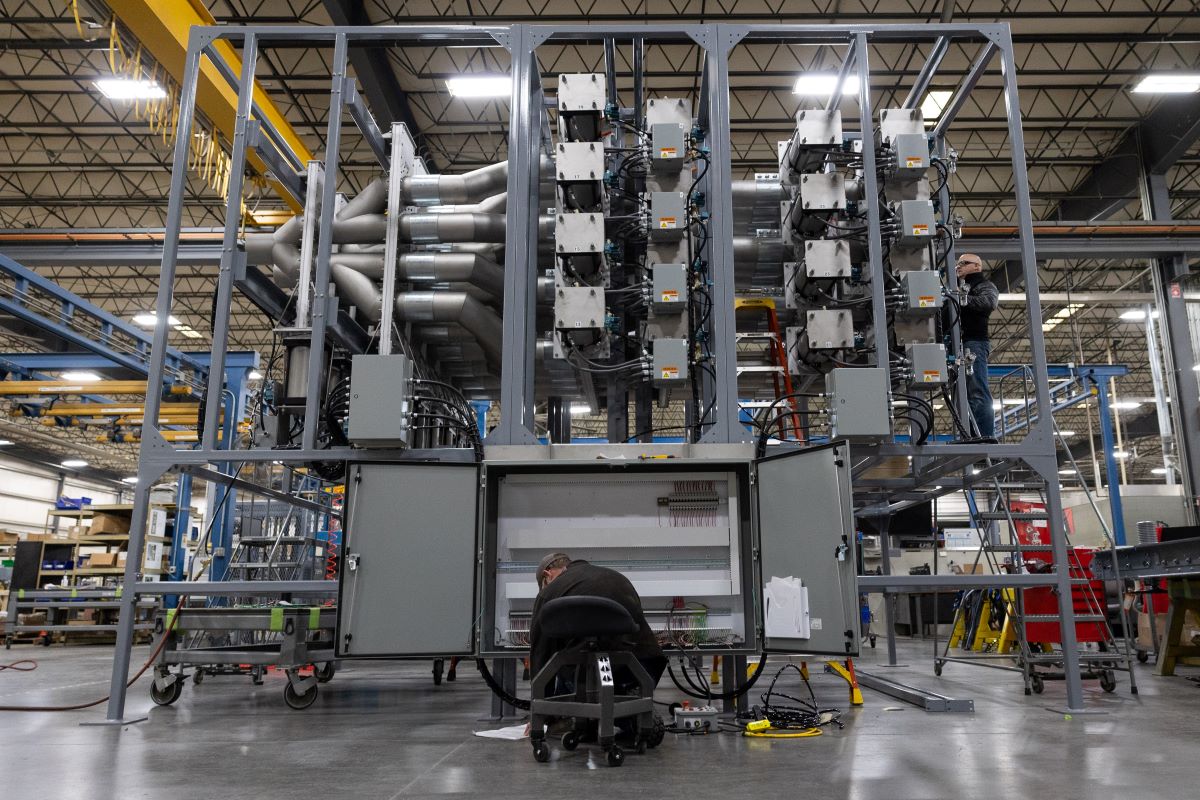
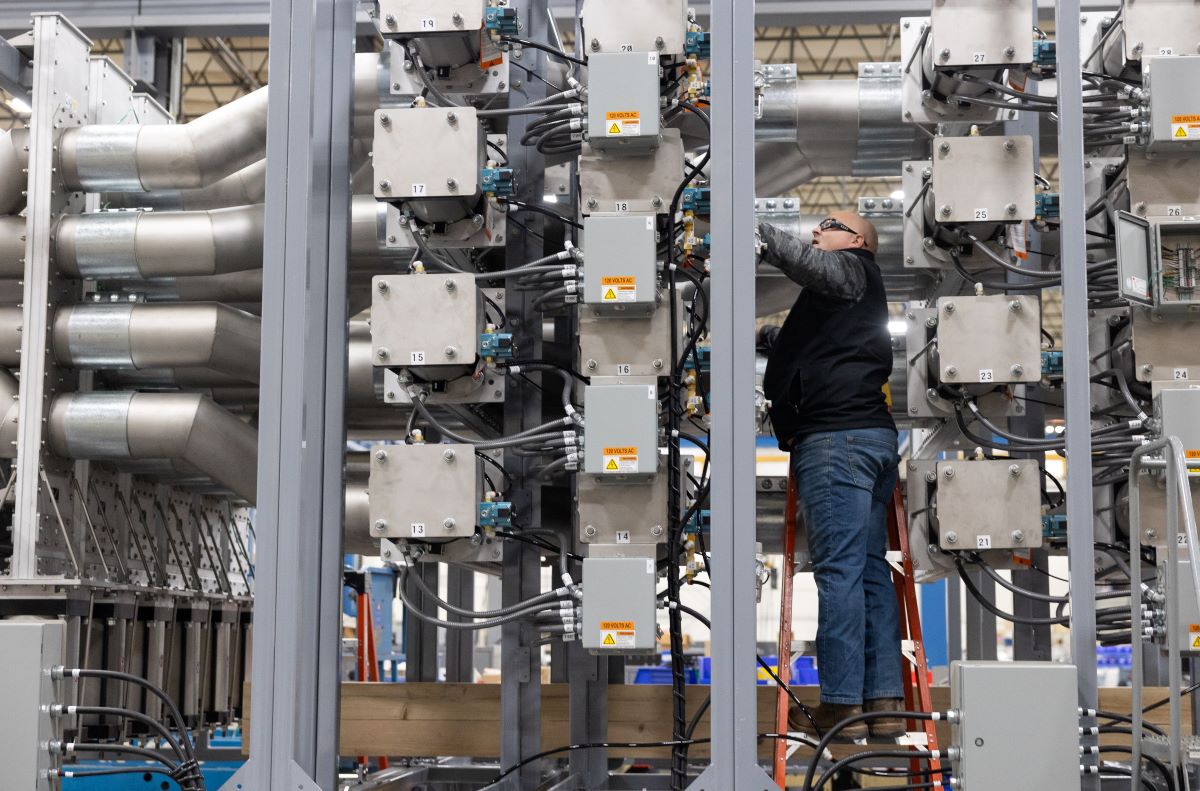
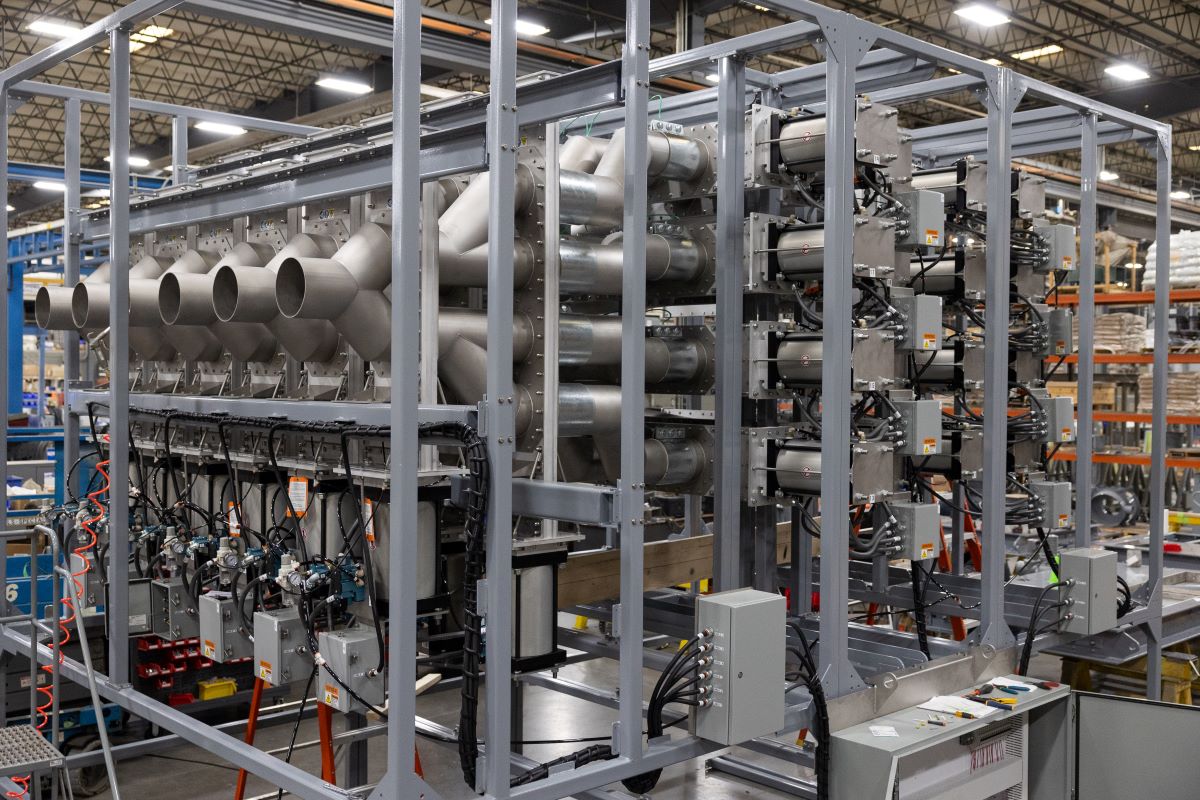
Technical Breakdown of the Equipment:
MULTIPORT DIVERTER, (6) SOURCE TO (4) SIMULTANEOUS DESTINATIONS INCLUDING STAND, COUPLERS, AND INSTALLATION OF DIVERTERS INTO STAND, CONSISTING OF:
Qty. (4) 3-WAY WYE LINE DIVERTERS, - MULTIPORT MOUNTED. WITH 10” BORE CYLINDER FOR 60 PSI SUPPLY PRESSURE.
Qty. (4) 4-WAY WYE LINE DIVERTERS, - MULTIPORT MOUNTED. DIVERTER TO BE MOUNTED HORIZONTAL WITH 10" BORE CYLINDER FOR 60 PSI SUPPLY PRESSURE.
Qty. (6) 4-WAY WYE LINE DIVERTERS, – MULTIPORT MOUNTED. DIVERTER TO BE MOUNTED VERTICAL WITH 10" BORE CYLINDER FOR 60 PSI SUPPLY PRESSURE.
Qty. (1) - SET OF INTERCONNECTING, 8" SCHEDULE 10 304 STAINLESS STEEL PIPING
Qty. (56) - COUPLING
Qty. (14) - AIR CONTROLS, - SET UP FOR 10" BORE AIR CYLINDER WITH 72" AIR CONTROL LEADS.
Qty. (56) - MAG REED SWITCHES, - MAG REED SWITCH, SET UP FOR 10" BORE AIR CYLINDER.
Qty. (1) - BALL VALVE
Qty. (14) - AIR PURGES, - MOUNTED ON DIVERTER. PLUMBED TO UPPER AND LOWER PORTION OF 3 WAY OR 4 WAY DIVERTER. TO INCLUDES SOLENOID FOR TURNING AIR PURGE ON AND OFF.
Qty. (14) - PREWIRED TERMINAL BOXES, - SET UP FOR CLASS II, DIV II. INCLUDES WIRING OF AIR PURGE ASSEMBLY.
MULTI-PORT DIVERTER CONSISTS OF 3 ASSEMBLED MODULES.
THERE ARE ELECTRICAL CONNECTION PANELS ON EACH MODULE.
SUB-PANEL #1 IS MOUNTED ON MODULE A. THE GATE PREWIRED TERMINAL BOXES OF DIVERTERS 1 THRU 4 ARE WIRED IN TO THIS PANEL, WHICH CONSISTS OF A NEMA 4 PAINTED STEEL ENCLOSURE, BACK PANEL, NUMBERED TERMINAL STRIP AND WIRE DUCT FOR WIRE MANAGEMENT.
THE MAIN PANEL IS MOUNTED ON MODULE B. THE GATE PREWIRED TERMINAL BOXES OF DIVERTERS 5 THOUGH 8 ARE WIRED IN TO THIS PANEL, AS WELL AS THE SUB-PANELS ARE WIRED IN, SPACE IS ALLOWED FOR CUSTOMER ALLEN BRADLEY REMOTE I/O INCLUDING POWER SUPPLY, 10 SLOT RACK, FUSED I/O TERMINAL MODULES WITH CABLES. THIS PANEL CONSISTS OF A NEMA 4 PAINTED STEEL ENCLOSURE, BACK PANEL, DIN RAIL FOR CUSTOMER COMPONENT MOUNTING, CIRCUIT BREAKERS, NUMBERED TERMINAL STRIPS AND WIRE DUCT FOR WIRE MANAGEMENT.
SUB-PANEL #2 IS MOUNTED ON MODULE C. THE GATE PREWIRED TERMINAL BOXES OF DIVERTERS 9 THRU 14 ARE WIRED IN TO THIS PANEL, WHICH CONSISTS OF A NEMA 4 PAINTED STEEL ENCLOSURE, BACK PANEL, NUMBERED TERMINAL STRIP AND WIRE DUCT FOR WIRE MANAGEMENT.
TO BE GROUNDED AND BONDED PER CUSTOMER SPECIFICATIONS. MODULE SECTIONS TO BE BONDED TOGETHER. EACH DIVERTER TO BE BONDED TOGETHER AND GROUNDED TO FRAME. CONVEY TUBES TO BE GROUNDED TO THE FRAME AT THE BEGINNING AND END OF EACH FLOW PATH. ONE GROUNDING LUG TO BE PROVIDED ON MODULE C PER CUSTOMER REQUESTED LOCATION.
ELECTRICAL DRAWINGS INCLUDING SCHEMATICS AND PANEL LAYOUTS AND SUPPORTING DOCUMENTATION IS INCLUDED.
MAIN PANEL AND SUB-PANELS TO BE WIRED TOGETHER FOR TESTING OF MULTI-PORT, WIRING BETWEEN MAIN AND SUB-PANELS TO BE DISCONNECTED AT ONE END TO FACILITATE SHIPPING.
Qty. (1) - PAINTED CARBON STEEL STAND, MATCHING CUSTOMER LAYOUT, INCLUDING ENGINEERING / WELDING / SHOP LABOR