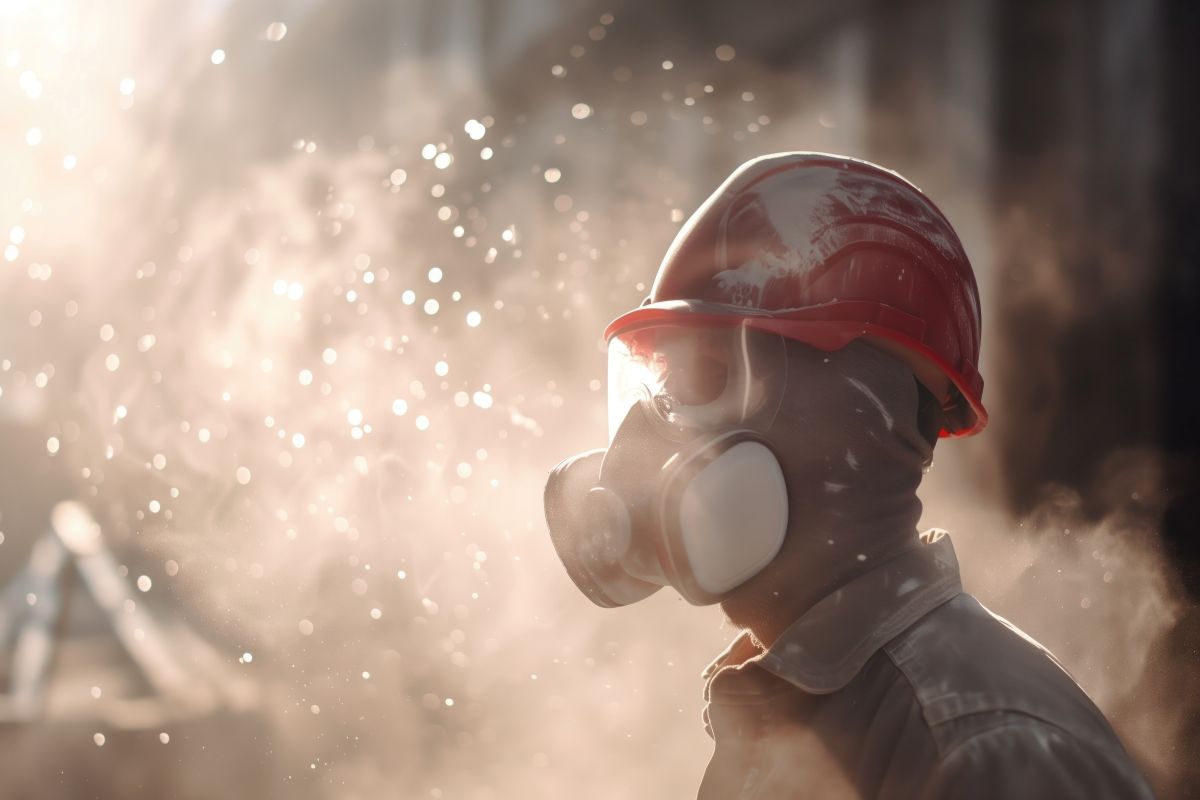
Client:
Quantity:
Size:
Application:
As Published in World Fertilizer
Dust explosions pose a significant risk in dry bulk processing industries, yet they are often underestimated. With catastrophic consequences that can include destruction of property, injury, and even loss of life, effectively controlling dust emissions is a necessity, not an option.
At the heart of this challenge lies proper material flow equipment, specifically dust-tight equipment. This equipment is essential for ensuring operational safety, minimizing environmental impact, and adhering to international regulations. This article explores the role of dust-tight equipment, the risks posed by dust accumulation, and how optimized equipment designs help mitigate dust explosions.
Understanding the Danger of Dust Explosions
Before diving into viable solutions, it is essential to first understand the root causes of the problem. Dust explosions are categorized as either primary or secondary, and each type has unique risks and consequences that industries must address.
- Primary dust explosions occur within confined spaces, such as equipment, silos, or processing machinery. These explosions happen when combustible dust is ignited within such enclosures. While dangerous, primary explosions are often managed with engineering controls, such as pressure relief systems that vent the explosion safely to the external environment, minimizing damage to equipment and injuries to personnel. However, even with these measures, the potential for escalation remains if dust is not properly controlled.
- Secondary dust explosions are far more hazardous and catastrophic. These occur when settled or accumulated dust inside a facility is disturbed and becomes airborne due to a primary explosion. The suspended dust cloud can then ignite, leading to a chain reaction of explosions that spread rapidly throughout the workplace. This widespread devastation can obliterate entire facilities and cause severe injuries or loss of life.
Combustible dust remains a serious threat in industrial environments, as demonstrated by both historic and recent disasters. The 2008 Imperial Sugar refinery explosion in Port Wentworth, Georgia, serves as a sobering example. Caused by an accumulation of sugar dust, the blast resulted in 14 deaths and 36 injuries. Investigators attributed the tragedy to poor housekeeping and ineffective dust control, declaring the incident entirely preventable.
Similarly, the 2010 Upper Big Branch Mine disaster in West Virginia was triggered by a coal dust explosion, claiming the lives of 29 miners. Investigations later revealed inadequate ventilation and blatant safety violations as primary factors behind the catastrophe.
In 2016, a dust explosion occurred in a fertilizer blending facility in China, caused by the ignition of fine dust particles during the mixing process. The explosion resulted in injuries and severe damage to the facility. This incident highlights the risks associated with handling fine, dry fertilizer materials.
More recently, on October 4, 2024, an explosion at the Hanford Grain Company in Hanford, California injured two workers. Preliminary findings suggest that highly flammable grain dust played a significant role in the incident.
These events underscore the ongoing dangers of combustible dust and highlight the urgent need for stringent safety protocols, proper housekeeping, and well-maintained equipment. By prioritizing proactive safety measures, industrial operations can prevent such avoidable tragedies and protect their workforce from harm.
The fertilizer industry is particularly vulnerable to dust explosions due to the fine particulate matter generated during production and handling. Like agriculture, food production (flour, starch, sugar, and spices), chemicals, plastics, metals, pharmaceuticals, and textiles, the fertilizer sector faces significant risks when dust builds up over time. These conditions can create the potential for catastrophic incidents if not effectively managed.
For companies in these industries, taking a proactive approach to controlling dust emissions is not just a regulatory requirement, it is a necessity for ensuring workplace safety. Utilizing dust tight equipment, implementing proper housekeeping practices, installing effective dust collection systems, and conducting regular risk assessments are critical steps toward mitigating the risk of both primary and secondary explosions. By addressing these hazards early and thoroughly, businesses can create safer working environments, protect their employees, and avoid the devastating consequences of a dust explosion.
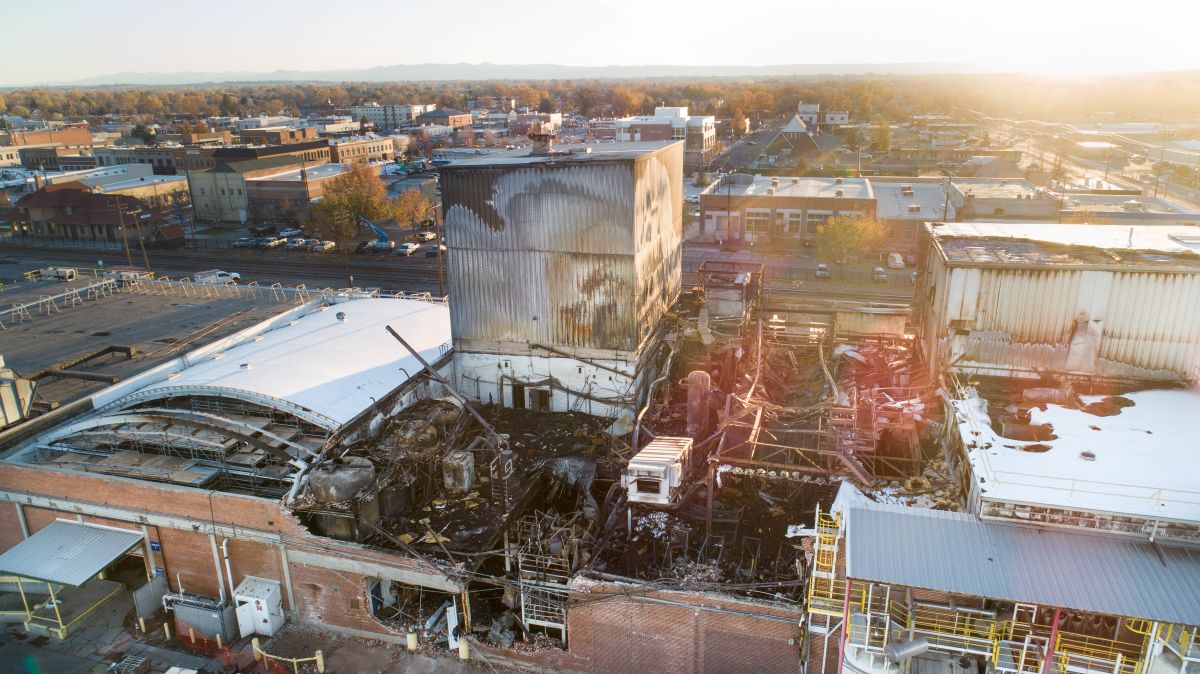
The Role of Dust-Tight Equipment in Dust Mitigation
Why is dust-tight equipment critical?
Dust-tight equipment is essential in dry bulk systems to regulate material flow, prevent fugitive dust, and ensure smooth, efficient operations. Whether handling fertilizer, grain, sugar, cement, or metal powders, industrial processes rely on equipment such as valves, conveyors, etc. to transfer and process bulk materials safely. However, equipment failures—particularly in seals or structural integrity—can lead to significant safety and operational risks, allowing hazardous dust to escape into the environment.
Airborne dust is a serious hazard when exposed to ignition sources like static electricity, equipment sparks, or hot temperatures. Dust explosions are a well-known risk in industries handling fine particles, and even small leaks in faulty seals or compromised equipment can contribute to unsafe working conditions.
The root of the issue often lies in traditional equipment designs and materials. Many standard components, including valves and seals, were developed for liquids or gases, and are not optimized for abrasive dry particulates. Friction, impact, and wear from solid materials cause these components to degrade prematurely, leading to leaks and operational inefficiencies. Modern dust-tight equipment addresses these challenges through advanced engineering and materials.
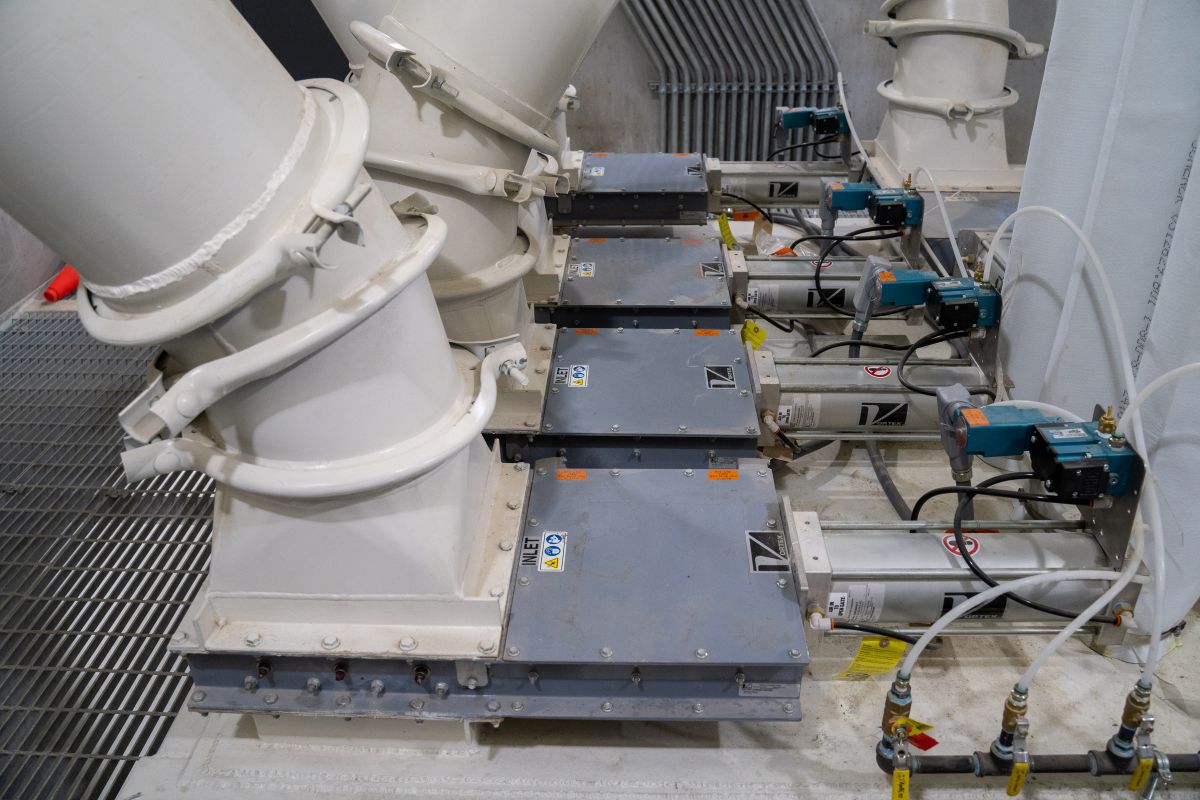
Features of Modern Dust-Tight Equipment
Dust-tight equipment is specifically designed to handle the unique challenges posed by dry bulk materials. With durable materials and precision design, these systems ensure both safety and efficiency in industrial operations. Key features of modern dust-tight equipment include:
- Durable Sealing Technology: High-performance equipment integrates seals made from abrasion-resistant composite materials that can withstand constant friction and impact from abrasive particles. These heavy-duty seals significantly reduce the risk of leaks and minimize maintenance needs.
- Reinforced Structural Integrity: Dust-tight equipment, such as reinforced valves and conveyors are built to endure demanding industrial environments. Robust housings and components maintain consistent performance even with abrasive/corrosive materials like fertilizer, cement, silica, or metal powders.
- Precision Manufacturing: The best equipment is engineered with extremely tight tolerances to prevent dust from escaping through gaps or misalignments. This precision improves overall durability and reliability, reducing downtime caused by leaks or mechanical failures.
- Ignition Prevention: Dust-tight equipment often includes ATEX-rated valves and components designed to prevent sparking during operation. Non-sparking materials and mechanisms are employed to eliminate ignition risks, ensuring maximum safety in environments where dust explosions are a major concern.
- Integrated Dust Collection Systems: Many modern systems incorporate dust collection technologies to capture escaped particulates. This ensures cleaner air quality, safer workspaces, and compliance with safety standards.
- Improved Efficiency: By maintaining strong seals and containing materials effectively, dust-tight equipment reduces the need for cleanup, maintenance, and system downtime. This translates into long-term cost savings and streamlines operations.
- Compliance with Industry Standards: Advanced equipment can be designed to meet strict regulations, including OSHA air quality standards and ATEX standards for dust explosion prevention. Businesses can ensure legal compliance while safeguarding workers and facilities.
Dust-tight equipment offers significant advancement for industries handling dry bulk materials. By addressing the limitations of traditional designs and mitigating risks associated with dust leakage, these systems improve operational safety, efficiency, and reliability. For any industry working with fine particulates, investing in modern dust-tight components is a critical step toward ensuring productivity, safety, and regulatory compliance.
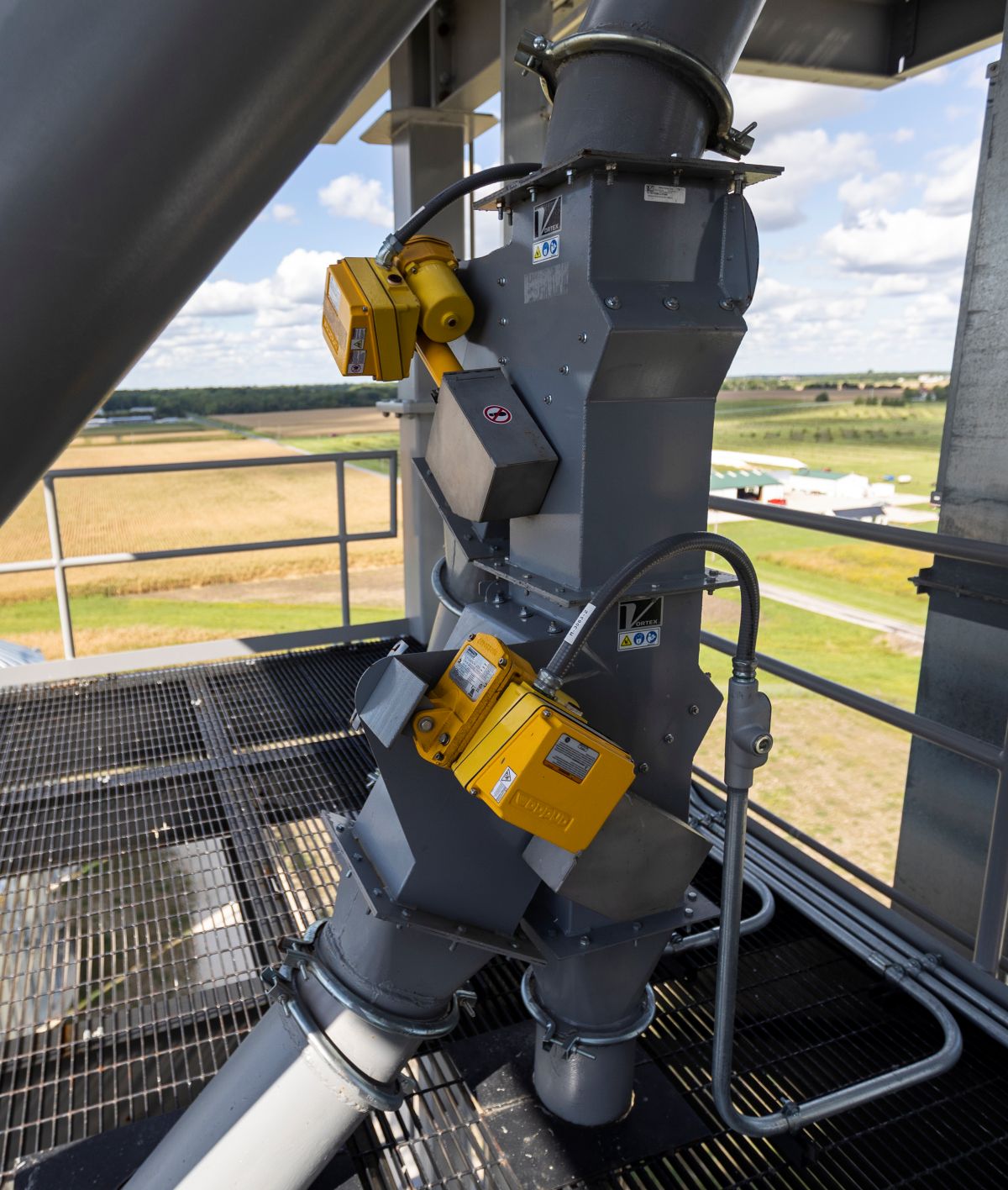
International Safety Standards and Certifications
Safety standards are essential in regulating environments prone to explosive dust, ensuring the safety of workers and facilities worldwide. Different countries and regions enforce specific standards to address these hazards. Three prominent systems govern these industries:
1. NFPA Standards (United States)
The National Fire Protection Association (NFPA) establishes guidelines to prevent fires and dust explosions in workplaces where combustible dust is present. Key standards, such as NFPA 654 and NFPA 484, outline safety practices for industries handling potentially hazardous materials.
According to NFPA, dust particles smaller than 420 microns are considered hazardous, as they can ignite when dispersed in air under the right conditions. Critical safety practices include conducting regular dust hazard analyses (DHAs) to identify and assess potential risks. Facilities must address these risks through improved equipment design, proper housekeeping, ventilation systems, and operational controls that minimize ignition sources.
2. NEC Standards (United States)
The National Electrical Code (NEC), maintained by the NFPA, provides guidelines for electrical installations in hazardous environments, including areas with explosive dust. NEC Articles 500-506 define hazardous locations and classify them into Classes, Divisions, and Groups based on the type of material and the likelihood of the hazard being present.
For combustible dust environments, NEC specifies Class II locations, further divided into Division 1 (where hazardous dust is likely, during normal operation) and Division 2 (where it may only be present under abnormal conditions). Proper selection and installation of electrical equipment certified for these classifications are critical to reducing ignition risks.
3. ATEX Directive (European Union)
The ATEX directive (2014/34/EU) lays out stringent safety requirements for equipment used in explosive dust atmospheres across the European Union. This directive is unique in its comprehensive focus, as it not only applies to electrical equipment but also to mechanical components, such as valves with moving parts, ensuring they meet dust-ignition protection standards.
The ATEX system divides hazardous dust areas into three zones—20, 21, and 22—based on the frequency and duration of explosive dust presence. Each zone requires specific levels of protection and compliance. Manufacturers must ensure that equipment used in these zones meets the required safety standards to prevent accidents and maintain operational safety.
Vortex Adheres to International Standards
As a global leader in dry bulk handling equipment, Vortex Global prioritizes safety by designing dust-tight equipment capable of meeting the highest international standards. Their equipment can be designed for use in ATEX Zones 20, 21, and 22 and can be fitted with controls rated for a variety of NEC requirements, ensuring comprehensive compliance with both U.S. and European safety regulations.
Vortex's forward-thinking approach includes equipment options that utilize advanced materials and engineering techniques to minimize ignition risks while maintaining peak operational efficiency. By aligning with NEC and ATEX standards, Vortex helps industries safely handle combustible materials, providing reliable solutions for hazardous environments. This commitment to safety and compliance makes Vortex a trusted partner in industries worldwide.
Dust Explosion Prevention Strategies
Preventing dust explosions requires a multi-faceted approach, combining equipment upgrades with workplace policies. Below are actionable steps companies can take to reduce risks effectively.
1. Conduct a Dust Hazard Analysis
Perform an in-depth assessment to identify dust explosion vulnerabilities. Here are the key areas to examine during this analysis:
- Identify materials with combustible properties.
- Locate areas prone to dust build-up, including hidden spaces.
- Ensure proper containment for processes generating airborne dust.
- Evaluate potential ignition sources in the facility.
- Assess ventilation systems’ capability to control dust dispersion.
2. Invest in Dust Collection Systems
Complement dust-tight components with an efficient dust collection system. Cyclone separators, baghouses, or electrostatic precipitators effectively reduce airborne particulates in manufacturing facilities.
3. Upgrade Valve Systems
Consider replacing outdated equipment with models engineered to be dust-tight to the atmosphere. Opt for smart systems that provide remote monitoring and feedback on equipment integrity.
4. Implement Regular Maintenance Schedules
Inspect and clean surfaces, equipment, and collection systems frequently. Proper maintenance prevents dust accumulation and ensures consistent valve performance.
Shaping the Future of Dust Safety
Dust explosions remain a persistent challenge for industries worldwide, but advancements in dust control systems and equipment bring tremendous progress. By prioritizing equipment innovations and adhering to international safety standards, companies can mitigate the devastating risks associated with fugitive dust.
Whether you are upgrading an existing plant or building a new facility, Vortex’s dust-tight components offer peace of mind. They are not just reliable, they are engineered with safety at their core, ensuring that you stay ahead of risks and industry challenges.
Why Vortex is Your Trusted Partner for Dust-Tight Solutions
When it comes to ensuring workplace safety and operational reliability, Vortex is the go-to name for global dry bulk processors. Here is why:
- Unmatched Expertise: With decades of industry experience, Vortex delivers tailored designs catering to differing bulk material characteristics. Offering an extensive range of Slide Gates, Diverter Valves, Loading Solutions, Aerated Conveying, Iris Valves, & Angel Hair Traps and a full staff of in house engineers offering complete custom options to fit your application.
- Comprehensive Certifications: Vortex equipment and controls can be designed to meet ATEX, IECEx, and NEC standards, ensuring compliance across international markets.
- Proven Performance: From food production to mining, Vortex equipment excels in demanding applications, boasting exceptional durability and efficiency.
Protect your facility, your employees, and the environment. Contact a Vortex specialist today to find the right equipment solution for your operations.