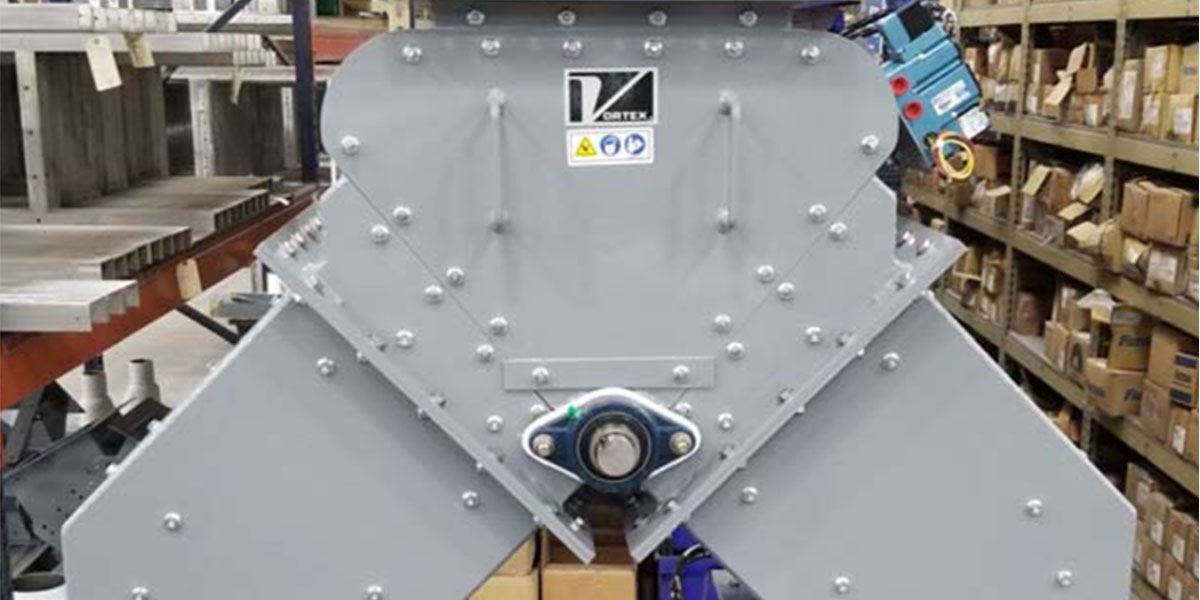
Client:
Quantity:
Size:
Application:
The maintenance of dry bulk handling systems can be a timely, costly, and messy endeavor. When designing dry bulk solid handling components used in these systems, many principles must be considered to address wear and abrasion to limit necessary maintenance, decrease production downtime, and extend the product’s service life.
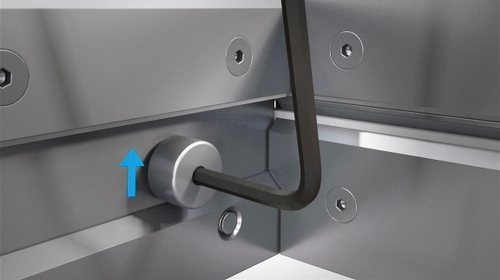
The implementation of components that can be maintained and repaired in-line provides a plethora of benefits to the consumer:
• More cost-effective to replace parts rather than the entire valve.
• Saves the company time and money by reducing downtime.
• No special equipment required.
Slide Gates
Slide gates are ideal for controlling dry bulk materials such as fly ash and potash in gravity flow and dilute or dense phase pneumatic conveying applications. Since slide gates are used to handle a wide range of materials around the world, manufacturers of slide gates are tasked with developing methods to extend the service life of these valves.
A well-manufactured slide gate should be strategically designed to allow for in-line maintenance and reducing the amount of downtime facilities must face to make repairs when needed. Slide gates can be designed for high cycle environments to not only prolong service life but to limit the amount of maintenance needed. The most effective way to limit maintenance requirements, is to implement strategies and features to limit wear.
Bonnet seals are important to hinder material migration into the bonnet area. Otherwise, gate actuation issues, as well as dusting into the atmosphere, can occur. In the production of cement, high silica concentrations pose many environmental and occupational health hazards.
In applications where abrasive materials are being handled, wear-compensating bonnet seals can be constructed from hard polymer and compressed rubber backing. As the polymer experiences frictional wear from multiple actuations over time, the compressed rubber load seals continuously force the polymer seal against the sliding blade. This ensures a consistent seal with limited maintenance intervention, even as the hard polymer seals experience wear overtime.
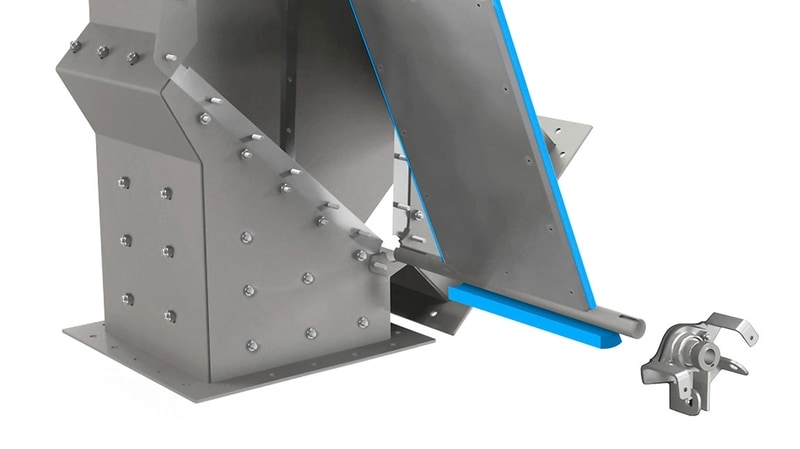
Bonnet seals will lose their compression load after many cycles and, therefore, must be replaced. The Vortex Titan Slide Gate is designed so that the bonnet seals can be easily replaced while the gate remains in-line. Using simple tools, the slot covers can be removed, and new bonnet seals can be driven into the milled access slots, as the worn bonnet seals are simultaneously ejected out the other side of the gate.
The Titan Slide Gate is also equipped with replaceable abrasion-resistant liners at the gate's inlet. The purpose of abrasion-resistant liners is to protect the gate's inlet, blade, rollers and side seals from abrasive wear caused by the material flow stream. For added durability, the gate's rollers are constructed from hardened steel rather than the industry-standard polymer rollers. The rollers are also cam-adjustable for in-line maintenance.
Diverter Valves
Diverter valves are commonly used to converge two (or more) lines of cement mixing material into one. They can also be used to separate one line of material into several. Often used to handle heavy-duty materials, diverters must be designed to address the abrasive nature of these materials. By addressing these concerns when sourcing a diverter, downtime and maintenance can be kept to a minimum.
Many bucket diverters and flap diverters are designed with thin elastomer seals adhered to the blade’s perimeter. These seals are constantly exposed to the material flow stream. Because most diverter designs do not provide the necessary protection for the internal seals, they often erode or tear away in service, deeming them ineffective.
Bucket seals constructed from a full sheet of thick rubber, sandwiched between the bucket blade and a metal plate can extend service life. Diverters can be designed so that the leading edge of the blade enters a recessed area, to protect the seals from the material flow stream. Because of these considerations, the diverter provides a positive seal across the opposite leg(s). This prevents material leakage, cross-contamination, and dusting past the blade, into the opposite leg(s).
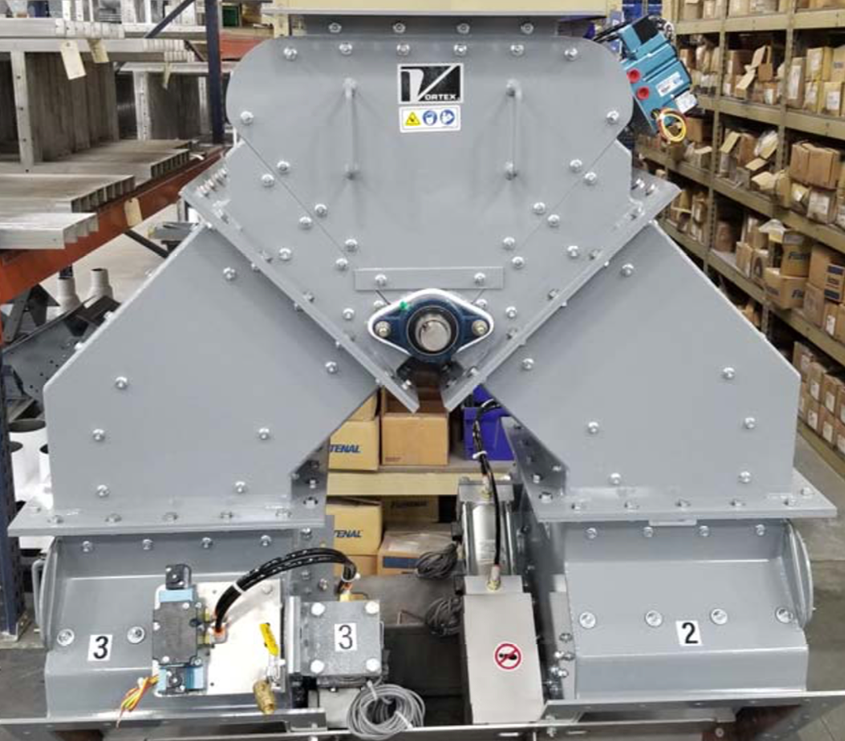
Equipping diverters with replaceable abrasion-resistant liners throughout can also address concerns of handling abrasive materials. The purpose of abrasion-resistant liners is to protect the diverter's material contact areas and other internal mechanisms from wear caused by the material flow stream. Liners can be constructed from durable metal materials, including 400 Brinell Hardness Number (BHN) abrasion-resistant steel and chromium carbide. For return-on-investment purposes, abrasion-resistant liners are critical because they are the difference between heavy-duty materials abrading upon replaceable parts, or full diverter replacement because materials have abraded holes through the body of the valve.
In applications where cross-contamination is not a concern, diverters such as the Vortex Aggregate Diverter can be equipped with rock box liners – also known as honeycomb liners – along the bucket blade and outlet chutes. The rock box design allows abrasive, dry materials to accumulate in gridded areas so that as materials flow through the diverter, particles abrade upon themselves, rather than abrading upon the diverter's material contact areas.
Many diverters are not designed to be maintained while in-line. Instead, the entire diverter must be removed from service, which results in significant downtime and expensive diverter rebuild or replacement. The Vortex Aggregate Diverter, Pivoting Chute Diverter and Titan Lined Diverter are all designed with are movable access panel, which allows interior inspection and/or maintenance to be performed while the valve remains in-line. These diverters are also designed with wetted parts that can be removed and replaced through the removable access panel. This accelerates the maintenance process and prolongs a diverter's service life.
Loading Spouts
Loading spouts provide fast and steady material flow during the loading of dry bulk solid materials such as cement in open and/or enclosed loading into trucks, railcars, or stockpiles. When equipped with proper components, a loading system can be designed to capture fugitive dust, prevent material waste and ensure plant and environmental safety. Like slide gates and diverter valves, loading systems are under an immense amount of pressure by the materials they handle.
Most loading spouts are designed with a two- or three-cable design. Should one cable of a two- or three-cable spout break from wear or premature trucker pull away, it is inoperable until repair is made. Vortex Global’s four-cable lifting design provides maximum stability and more lifting torque compared with standard loading spouts. Should one cable on the Vortex four-cable spout break, the spout is still operational while waiting for repairs.
All Vortex spouts are equipped with a CNC-machined pulley. To eliminate cable fraying, a loading spout can be equipped with an additional CNC-machined three-piece pulley with rounded edges and precision cable grooves. This design prevents cable failure and other costly downtime for cable repair.
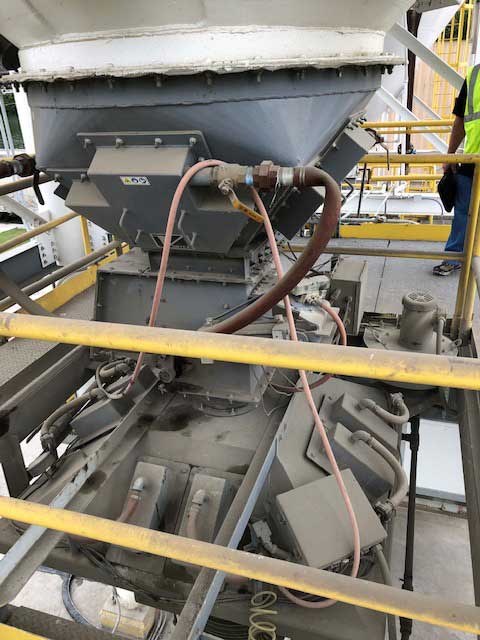
Many traditional spouts utilize eyebolts to guide the sleeve support rings during spout extension/retraction. The primary disadvantage to eyebolts is their maintainability. If either the lifting cables or the outer sleeve must be replaced, eyebolts must either be removed from the sleeve or physically distorted (opened) to free the sleeve from the lifting cables.
To resolve this maintainability issue, a spout can incorporate four spiral-shaped cable guides along the circumference of each outer support ring. The primary advantage of spiral guides over eyebolts is that the lifting cables and/or the outer sleeve can be removed without having to manipulate the spiral guides. The lifting cables can be extracted from the spiral guides while the guides remain connected to the sleeve support rings.
Loading Positioners are used in conjunction with standard volume loading spouts to facilitate and speed up the loading of open or enclosed trucks and railcars at loadout stations. Internally vented spout positioners allow for dust control during the loading process. While the hopper and spout remain attached to the positioner, hopper seal replacement can be easily performed to limit downtime.
Spout filtration systems engineered to capture the fugitive dust emitted from the spouts and deposit it back into the material flow during the loading process, eliminating material loss. These filtration systems are more cost-effective than central dust collection systems and offer in-line maintenance features. Magnehelic® pressure gauges provide differential pressure readings. When high differential pressure is indicated, filter cartridge maintenance or replacement is needed. Filtration systems that feature hinged panels secured by a handled, stationary clamping mechanism to accelerate the inspection and maintenance processes, and for interior access without tools.
Case Study: Titan Lined Multiport Diverter Handling Sand and Cement
A cement mix packager sourced a Vortex Multiport Diverter comprised of three, two-way Vortex Titan Lined Diverters in their system. This unique multiport arrangement allows material to be delivered from a single source to any of four destinations – one destination at a time. The diverter outlets are 14” (356mm).
Features:
Two Vortex Titan Lined Diverters are connected by fabricated chutes to create a four-way multiport diverter. The diverters and the chutes are manufactured with replaceable, abrasion resistant, interior steel liners (400 BHN) to address the abrasive qualities of the materials being handled by the customer. These features are designed to extend the service life of the diverter.
Each diverter contains an exterior access port that allows inspection or maintenance of the diverter without having to remove it from service and limiting downtime. Unlike alternative flap diverters, the Vortex Titan Lined Diverter features a removable access panel that can be removed using simple tools. In abrasive applications, this is an especially beneficial feature to be able to replace blades or liners quickly and easily without having to take the valve out of service to return it to the manufacturer for maintenance.
Case Study: Titan Slide Gate to Handle Cement-Based Mortar Mix
Four Vortex Titan Slide Gates were sourced by a cement manufacturer to handle cement-based mortar mix in their process. These gates feature 10” (254mm) round outlets. The gates will be utilized to convey the mortar mix to a bagging operation once it has been blended.
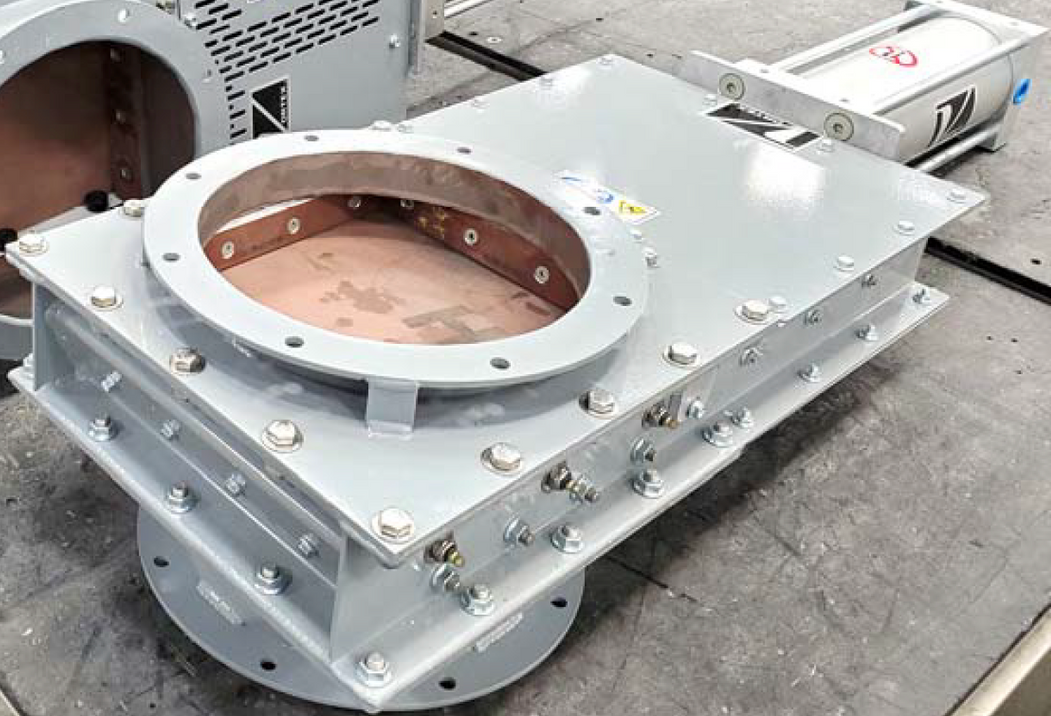
Features:
The Vortex Titan Slide Gate is designed to handle abrasive materials in gravity-fed applications. To combat wear, the gates contain abrasion resistant steel blades and liners.
Replaceable bonnet seals make in-line maintenance possible. Because of the fineness of the product handled, the gates were manufactured with a special polymer end seal. Over time, if the gate starts to leak dust, a new end seal can be tapped into the end slot, ejecting the old seal out the other end without having to take the valve out of service.
Round-to-square inlet flanges and square-to-round outlet transitions were installed to match the shape of the customer’s conveying line.
Case Study: Vortex Loading Spout, Filtration System and Aero Bin-Bottom Assist Cement Terminal
Following complaints from neighboring businesses regarding dust exposure, a cement terminal contacted Vortex to assist in developing a dust-free loading system.
Features:
This loading system utilizes three products from the Vortex line of Loading Solutions - a Vortex Loading Spout with a vertical travel distance of 14” (355mm), a Vortex In-Line Filtration System and a Vortex Aero Bin-Bottom. The telescoping loading spout features a self-sealing discharge cone that contains dust when the spout is inactive. The aero bin-bottom creates less head room and offers a cost-effective discharge of material at a much smaller angle of repose.
The in-line filtration system traps dust created during loading and re-introduces it back into the load. Panels are hinged and secured by a handled, stationary clamping mechanism to accelerate the inspection and maintenance processes, and for interior access without tools.
Conclusion
When designing a system for the handling of dry bulk solid materials, maintenance will be inevitable over the course of the systems’ lifetime. Sourcing products that are designed to address abrasion/wear concerns, require little maintenance, and can be maintained while in-line without having to disrupt your process can save valuable time and money.