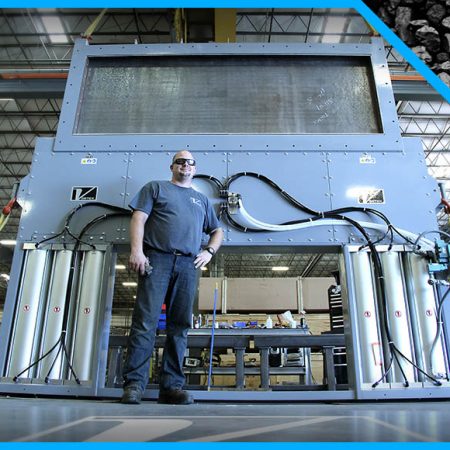
Client:
Quantity:
Size:
Application:
Since the company's founding in 1977, Vortex has taken pride in creating unique, standardized valve designs. In addition, Vortex works with customers on a case-to-case basis to customize valve designs, in order to best fit their specific applications. Applying in-depth knowledge of dry bulk solids, Vortex engineers assess material characteristics and application parameters to develop solutions per customer requests.
The Vortex Titan Series is engineered to handle heavy-duty situations - especially those where excessive abrasion and wear, extreme valve size, or especially harsh environments are to be considered.
Due to the abrasiveness of materials and the large-scale nature of many coal operations, Vortex Titan Series gates and diverters are often called upon and modified to better service customer applications.
Titan Lined Diverter
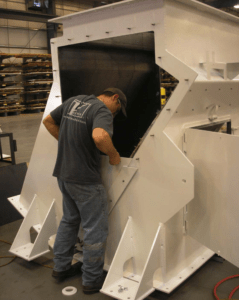
In 2008, Vortex was contacted by a US engineering company to assist on a project for a coal-fired energy plant. The plant’s operations involved drying lignite coal, in order to increase its value as a power plant fuel. This process is critical because by reducing the moisture and ash content present in coal, less coal is required to conduct a similar amount of electricity, thus resulting in fewer ash emissions.
The project supported a plant expansion that required flapper-style diverter valves of differing sizes, designed to handle coal ranging in size from 8” (200 mm) lumps to coal dust. In this particular application, 18 diverter valves with channel sizes ranging from 6” x 6” (150 mm x 150 mm) – 36” x 54” (915 mm x 1,370 mm) were required.
In one large, pre-existing flapper diverter used to handle incoming coal, the plant had installed replaceable polymer liners to reduce wear on the diverter, compensating for the volumes being handled and the abrasive qualities of coal. However, every 18 months, the system’s operations were halted so that the diverter could be taken out of line to replace worn liners. The replacement process involved detaching the diverter from its in-line position, maneuvering a crane to remove the diverter from line, moving the diverter into an area where it could be safely accessed for maintenance, making necessary liner replacements, then utilizing the crane to reinstall the diverter in-line. As you can imagine, this created expensive down-time in the company’s manufacturing processes.
As a solution to these accessibility issues, Vortex engineered a large Titan Lined Diverter (TLD) to feature a front access panel, which can be easily removed to allow inspections, maintenance, or liner replacements while the valve remains in-line.
To reduce wear on the diverter blade, the Vortex design allows the leading edge of the blade to fully actuate into a chamber across the valve, leaving the blade’s edge out of the material flow stream. While providing the further benefit of a positive shut-off in the material flow stream, this design feature prolongs the useful life of a diverter and leads to significant reductions in maintenance costs.
Vortex TLDs may be constructed of abrasion-resistant steel to address heavy-duty and abrasive applications, and can be equipped with replaceable liners constructed of highly durable materials, such as abrasion-resistant steel, polyethylene terephthalate (PET) polymer, or ceramic.
By transitioning from the traditional flapper diverter design to the Vortex TLD, the coal plant determined that in just three years, the cost savings associated with maintenance alone would replenish the purchase price of the Vortex valve in its entirety.
The math is simple: Have expensive down-time to replace a valve’s liners twice in three years, or replace the current system with a valve that is more reliable, more accessible, and more durable – for the same price?
The company installed its Titan Lined Diverter in 2009, and it continues to offer dependable service to this day.
Titan Maintenance Gate
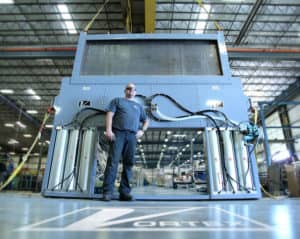
In 2012, a second US engineering company requested solutions for the handling of 2” (50 mm) minus bituminous coal in a coal-fired energy plant. This particular plant is responsible for pulverizing coal into a fine powder, so that it can become furnace fuel.
The customer requested a slide gate be situated between a surge bin and a posimetric feeder, to ensure the uninterrupted flow of material as it moves through the system. Once coal reaches the posimetric feeder, the flow of material is metered into a crusher to reduce the size of coal. The particles then proceed toward a grinder, which further refines the coal to its desired final state.
For this application, the appropriate solution was a custom-engineered Vortex Maintenance Gate. This valve allows the coal-fired energy plant to leave the Maintenance Gate open at all times, while also providing a mechanical solution to efficiently close the valve and create a positive shut-off in material flow when system maintenance is necessary.
The slide gate’s blade is constructed of 450 BNH abrasion-resistant steel, has a thickness of 1.25” (30 mm), and features a beveled leading edge. In total, the slide gate weighs approximately 1,400 lbs (635 kgs). The gate’s blade is supported by rollers, and is directed using blade guides for smooth actuation.
Vortex Maintenance Gates also possess compression-loaded polymer seals to discourage migration of fine material into the gate’s bonnet area when it is in the open position. Tension bars were installed in this application to allow for seal adjustments as future wear begins to impact the valve. The bars are accessed through removable bonnet covers, allowing adjustments to be made without removing the gate from line.
This particular application is pneumatically actuated, so that sufficient force can be applied to allow the valve’s blade to close through a standing column of bituminous coal, should a system issue occur. To equip for this, the Maintenance Gate employs six air cylinders, each 8” (200 mm) in diameter. These cylinders require 80 psig (5 barg) of forced air in order to stroke the blade closed. Upon installation, the pneumatic air cylinders can now create a combined force of more than 24,000 lbs (10,885 kgs).
Because a building support column limited the area where the gate was to be installed, Vortex engineered the rear of the Maintenance Gate to include an open area, with three air cylinders installed on either side. As a result, the gate could then be “wrapped around” the column, solving the issue of installation interference.
In Closing
These testimonials and many others serve as proof that no matter the scope or size of an application, Vortex engineers will listen to customer needs and develop the right solutions for meeting even the most demanding applications.
World Coal – March 2017