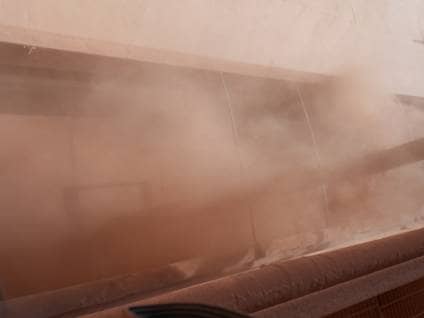
Client:
Quantity:
Size:
Application:
Grain elevator sock. Drop-down sleeve. Spigot. Flexible bellow. Telescopic chute. Loading spout. There’s lots of words in different regions of the world to describe a long cylinder to load material from one place to another location via gravity. But what is the difference between a loading sock and a loading spout?
The Loading Sock
If your budget is tight, a loading sock is the perfect solution until you can upgrade your plant equipment with something a little more robust. Most loading socks are often made in a 6-8″|150-200mm diameter. The actual sock is a cylindrical tube of fabric sewn to be tapered much like that of a windsock, and can be made by a local tarp maker from canvas or polyurethane fabric. For support, the sock is then secured to a rigid steel piping. The loading sock is flexible and can easily hang down over the hatch of a semi-tank or railcar as well as the tops of open trucks and gondola type rail cars.
Material is fed into the top of the sock and then by gravity, falls into the transport vessel below. To guide the sock, you move it manually and in some cases, may have to physically hold it in place while the grain or powder falls to its destination. The free fall of material will most likely create fugitive dust when loading this way.
Once you have dumped the material, the sock is rolled up and secured to prevent additional material falling out, and to prevent contamination of the interior due to unwanted pests. The time and labor to seal the sock after each use can consume as much time and labor as loading the material into the railcar.
The Loading Spout
Installing a loading spout in your bulk handling system can contain the flow of material into a more confined area, thus reducing the radius of debris and dust. Unlike the one layer of a loading sock, a loading spout actually possesses three layers to help contain dust emissions:
1. Internal Stacking Cones – Layer one is a series of internal stacking cones that can be constructed from materials like AR steel or polymer.
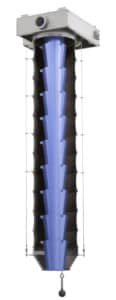
2. Fabric Outer Sleeve – Layer two is a fabric sleeve that encloses the cones keeping the dust inside the system.
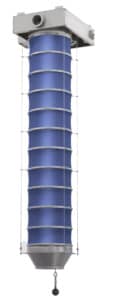
3. Neoprene Rubber Skirt – Layer three is a neoprene rubber skirt located at the bottom of the spout. Typically used in open loading applications, the skirt rests on top of the stockpile where the material flows.
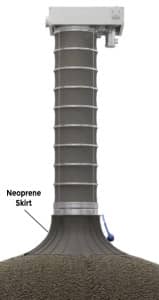
To fully control dust emissions during the loadout process, a fourth layer can be added. Loading spouts can be equipped with an in-line filtration system or integrated into an already existing dust filtration system. Using all four of these layers will drastically reduce dust emissions in comparison to using a sock.
Another benefit of a loading spout is the automation ability. A spout can be automated with a level-sensing probe to control the flow of material. When the spout is lowered into a railcar or stockpile, the slide gate at the top of the spout automatically opens. As the pile grows larger, the probe signals the spout to raises automatically to keep a consistent flow. Once the pile reaches a predetermined height, the automation closes the slide gate stopping the flow of material. This eliminates human error and wasted material costs due to overfilling.
Loading spouts can also be fitted with single and dual-axis positioners. This becomes useful when trucks, railcars, and vessels don’t always line up in the exact same place. When loading enclosed trucks or railcars, this process can be automated utilizing the hatch opening. The automated positioner can find the hatch and line up the spout accordingly.
The convenience of having a loading spout with automated controls, a dust filtration system, and the flexibility to move will come at a higher cost when compared to a loading sock. But if you consider safer working conditions, a reduction in plant cleaning costs, and a decrease in material waste, the ROI for a loading spout can easily outweigh the higher upfront costs in a short period of time.