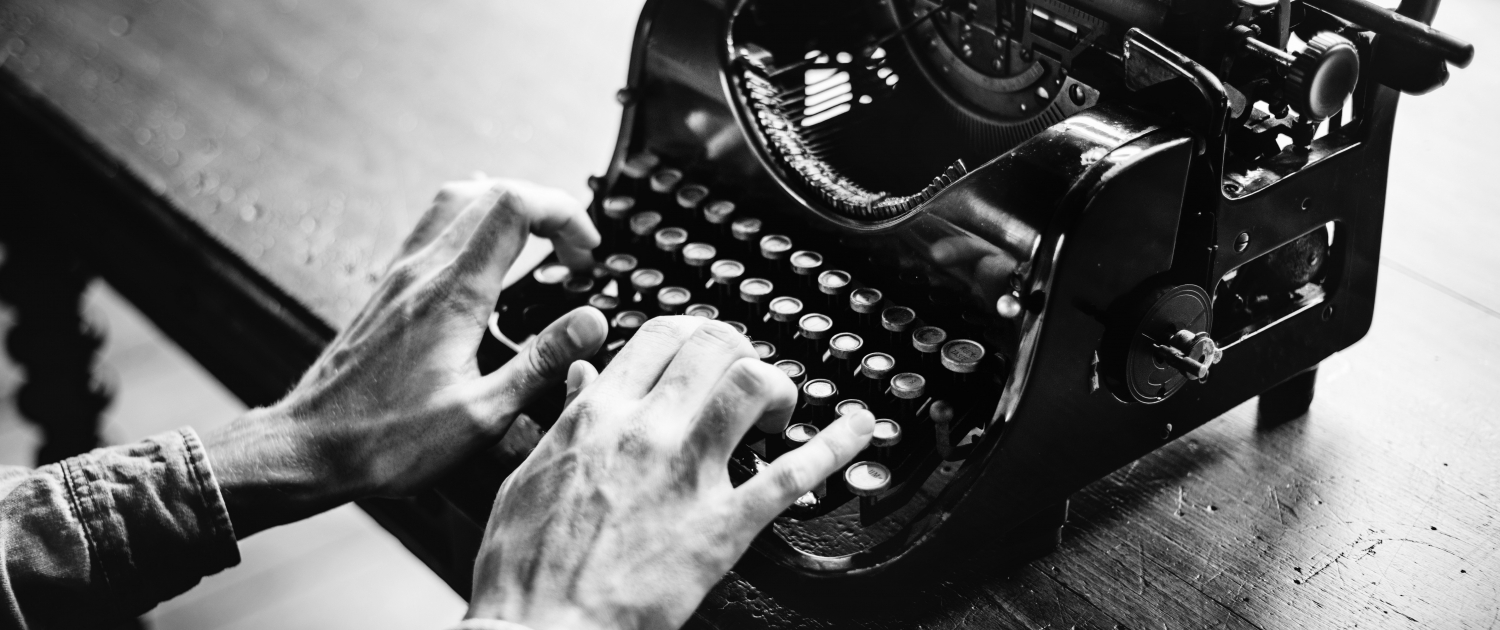
Client:
Quantity:
Size:
Application:
By Loren Neil Peterson
The bulk handling of flour as we know it today did not just happen. A few pioneers made it happen. There was a lot of hard work involved; some successes and a large number of failures.
Here is one man’s story:
Bulk Handling of Flour
Source: ADM Cincinnati – Wednesday, May 17, 1967
I wonder how many of us can remember when flour was packed around the clock, twenty-four hours, day and night. When few mills had the luxury of flour storage and day light packing. A good flour packer could pack out the small hold bin above his packer in 30 minutes and then spot for 30 minutes. I was a trucker during this era and well remember how I used to run back from the car with my hand truck so that I would not have to pick bags off the floor when the operator got ahead of me.
In 1942 this condition still existed with us and in 92% of all other mills in the USA. World War II was going on and conditions got worse as men were drafted into the army. Flour packers got very independent pushing for higher wages, and refusing to work nights. One day a flour packer walked into my office and demanded more money. He said that there were several big firms after him. Not having much choice I gave him the raise. As he was leaving I asked would you mind giving me the names of the big companies that were after you? No, he replied, they were the Power and Light Co., the Gas Company and the Water Works. They would like me to pay my bills.
That wasn’t really true but we did decide to do something about the situation. Our first step was to build bulk flour storage at all our mills with enough bin capacity to hold over a weekend and enough packing capacity to pack out in 5 eight hour days.
This eased the packing man power pressure and gave us confidence in our ultimate goal, to promote bulk handling at bakeries and eliminate all packers. I am referring to our bakery mills of course. Selling bakeries on the idea of bulk handling presented many problems. I will first present the problem and then show you our answers to those problems.
Bins
Problem number one pertained to bulk bins. Most bakeries did not have space for the conventional vertical bins either in their plant or on their property. The average construction contractor knew very little about the handling of flour and in order to protect himself, charged exorbitant fees for bin construction. We were quite aware that unless this problem was solved our whole idea was dead, the milling industry would never reap the benefit from bulk handling to its fullest extent. Even though the savings were pointed out, bakeries as a whole were not interested in going bulk, mostly because of high investment cost.
Transportation
The second problem was the transportation of flour. Only 20% of all the bakeries were located on a rail siding. This meant that most of the bulk flour would have to be trucked. We must either have flour mills, or bulk flour terminals, located within a 200 mile trucking range of all bakeries we wished to serve. We elected to go the bulk flour terminal route and locate rivers where ever possible. To speed up progress we used any suitable building. We built flour terminals in railroad round houses, liquor storage warehouses, oil pumping stations and built a number of new slip form structures. Each site had its own challenge. Bulk flour barges had to be designed and built. There were not enough airslide cars in service to take care of the present demand let alone our flour terminals. For sanitary reasons we were not satisfied with the screw bottom bulk truck then on the market.
Transferring Flour
The third problem was the transferring of flour from the bulk vehicle to bins. It could be done mechanically or by air. We were experimenting with pneumatics both positive and negative pressure.
Econo-Flo
It did not take us long to realize that if we were ever going to see our dream come true in our life time, we would have to help our customers get into bulk handling, so we set up a department known as, Econo-Flo, as a service to our customers. This was to be a non-profit organization. That turned out to be the understatement of the year. We forgot to figure in the countless trips we would make to bakeries to teach them how to operate their bulk system.
Then there were other problems. We could find no one that had any ideas on building a usable bulk flour barge. As far as we could find out, we were the only people in the U.S., or in the world for that matter, that ever attempted to transport an edible commodity for human consumption, bulk in a barge. Econo-Flo would have to design and build bulk barges. We would have to have bulk cars for supplying terminals not located on the rivers. We decided to convert standard box cars to sanitary bulk containers and device some practical means of dumping them. We proposed to build our bulk trucks on the same principal. They would at least be easier to clean than screws in a trough.
Econo-Flo Firsts
During our development years we believe we originated some firsts. Econo-Flo was the first to design an airlock feeder that would pass between the rail and hopper of an airslide car to unload it.
The first to develop and use a sanitary wing type feeder under vertical storage as it is known today.
The first to use a belt, 40’ long, as a live bottom horizontal bin feeder.
The first to dump bulk flour out of a standard box car.
The first to empty flat bottom bins 20’ in diameter and leave only 5 to 10# residue on the bin floor.
The first to transport bulk flour in a river barge with equal sanitation standards of bulk rail cars.
We helped hundreds of bakeries get into bulk and by 1958 had reached our goal in one mill and eliminated all packing.
By the early '60s, we had sparked so many firms into the bulk equipment business that it was no longer necessary for us to help the bakeries. We were then 100% bulk.
I would like to give due credit to two independent firms, Salina Manufacturing Co., and Jarvis Construction Co., who devoted much time and effort in helping us develop and build many of those projects. They now have taken over bulk handling where we left off.
Trout Bakery
Our first bakery project was in 1953. On a consultant basis we helped design and direct the construction of a 4 bin vertical flour storage with a total capacity of 2000 CWTS. The interesting part of this installation was the savings to our customer. The bakery was quoted $100,000 by a building contractor for this bulk system and he actually got it built under our direction for about $8,000.
Carrying the Torch
In 1967 at the time of writing, Vortex co-founder Loren Neil Peterson was an engineer at Salina Manufacturing Co. and played a significant role in these projects. His work concentrated on developing innovative solutions for pneumatically conveying flour and other dry bulk powders. In 1977, he left Salina Manufacturing Co. to pursue a pneumatic conveying concept he invented. He was joined by his son-in-law, Lee Young. Though the conveying system was a failure, during their inventing, they developed a slide gate that was well-designed for handling dry solids. Instead, that gate – now named the Orifice Gate – was brought to market, patented, and received a Vaaler Award for its immediate, significant impact in the chemical industry. This is the early history to what Vortex has become today.