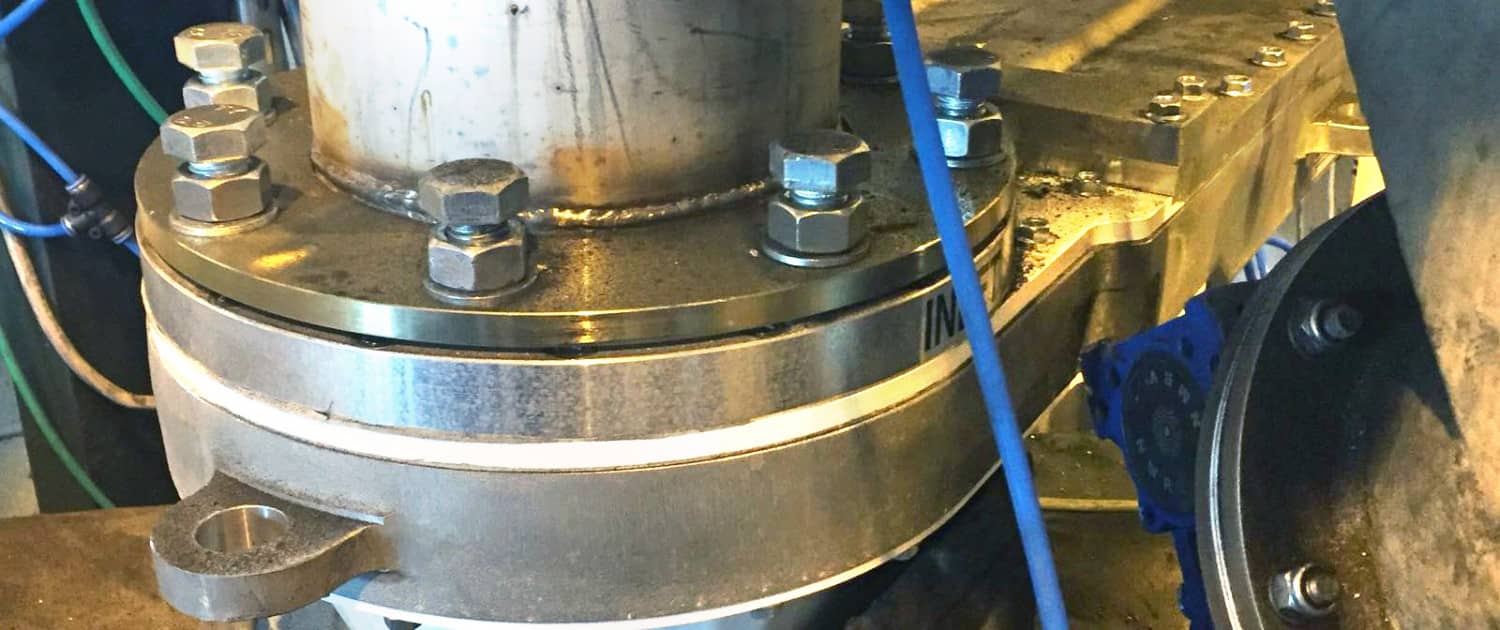
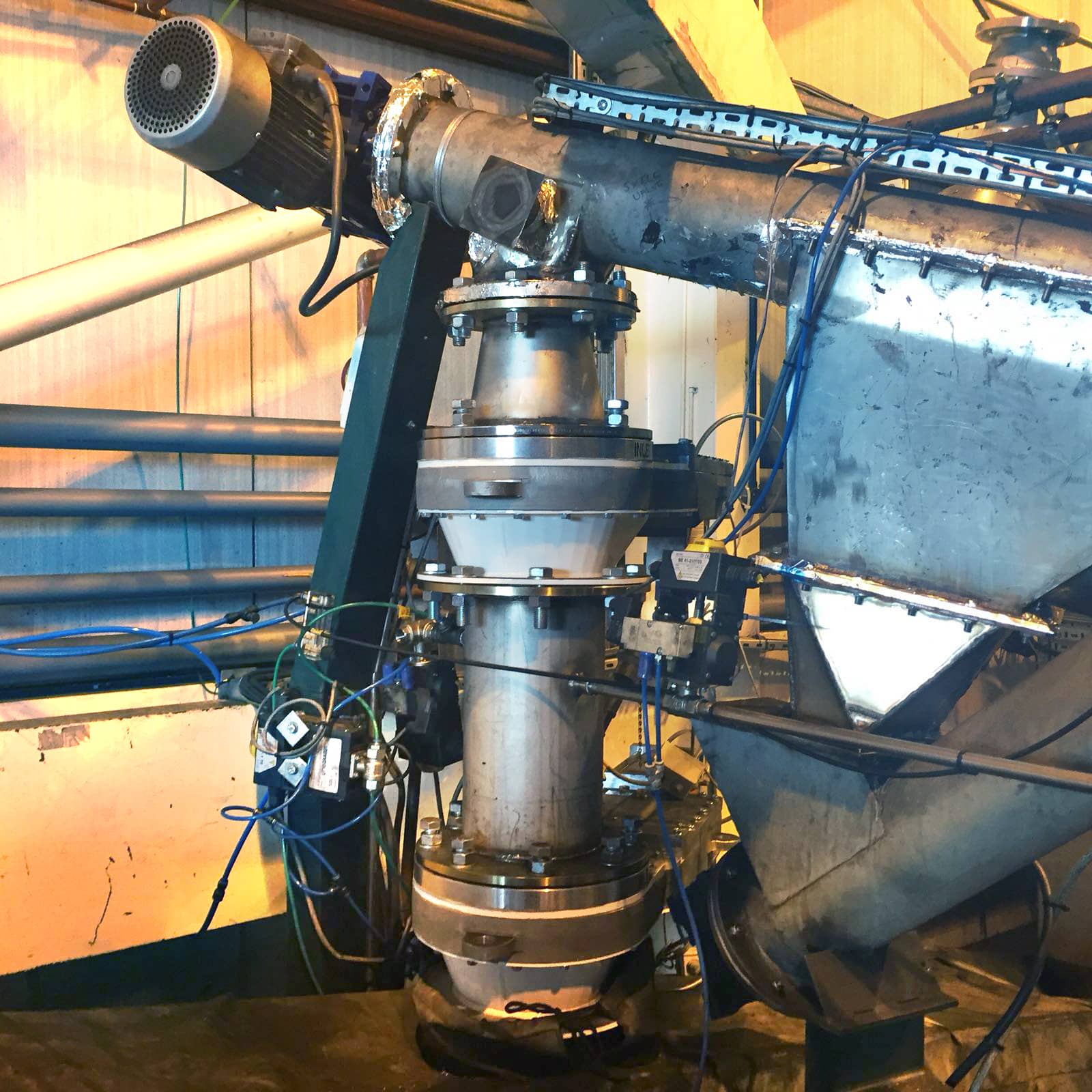
Advances in material science have led to the creation of high performance materials that offer significant benefits to both brands and consumers alike. Once these products have served their purpose, the challenge is to handle them responsibly; this is the case of plastic aluminum laminate packaging.
Enval Ltd. was created in 2006 to answer this environmental challenge. By 2010 Enval had constructed a pilot plant that used the process of microwave induced pyrolysis and created the world’s first solution for recycling plastic aluminum laminates. After the creation of the Enval consortium, the first commercial demonstration plant for the Enval process was built.
Pyrolysis is a process in which an organic material, such as paper or plastic, is heated in the absence of oxygen. In the case of the Enval process, the energy to heat up material is supplied by microwaves generators powered by electricity. The high temperature from the microwave-induced pyrolysis causes the molecules of plastic to break down so that the material degrades without combustion or incineration. During the process, aluminum foil remains undamaged and can be recovered in its solid form, clean and ready for reprocessing.
As part of the process, Enval had to source a vacuum tight double-dump valve arrangement suitable for handling the hot aluminum foil produced from the microwave process.
The valves and the seals had to be suitable for continuous high working temperatures of 150°C | 300°F. Vortex’s seals are designed for 204°C | 400°F continuous use. It also had to be full bore to maintain material flow and robust enough for high cycle frequency with up to 1,900 cycles per day.
The Vortex HDPV2 Gate was determined to be the ideal solution for this application. The 200 mm | 8 in diameter valves were suitable for full vacuum and for pressures up to 5 bar | 75 psig. The pneumatically actuated HDPV2 cast aluminum body valves were complete with stainless steel blades and contact parts.
The top valve was complete with a self-contained air reservoir so that if the plant suffered a loss of compressed air, the valve could still fail safe to the closed position.
Designed to address higher-pressure applications up to 5 bar | 75 psig depending on size, the Vortex HDPV2 sets itself apart from traditional industry slide gates. The rising blade design provides positive material shut-off by means of an O-ring seal on the inlet of the valve. This design feature eliminates the issues related to packing of material causing abrasion to the end seal.