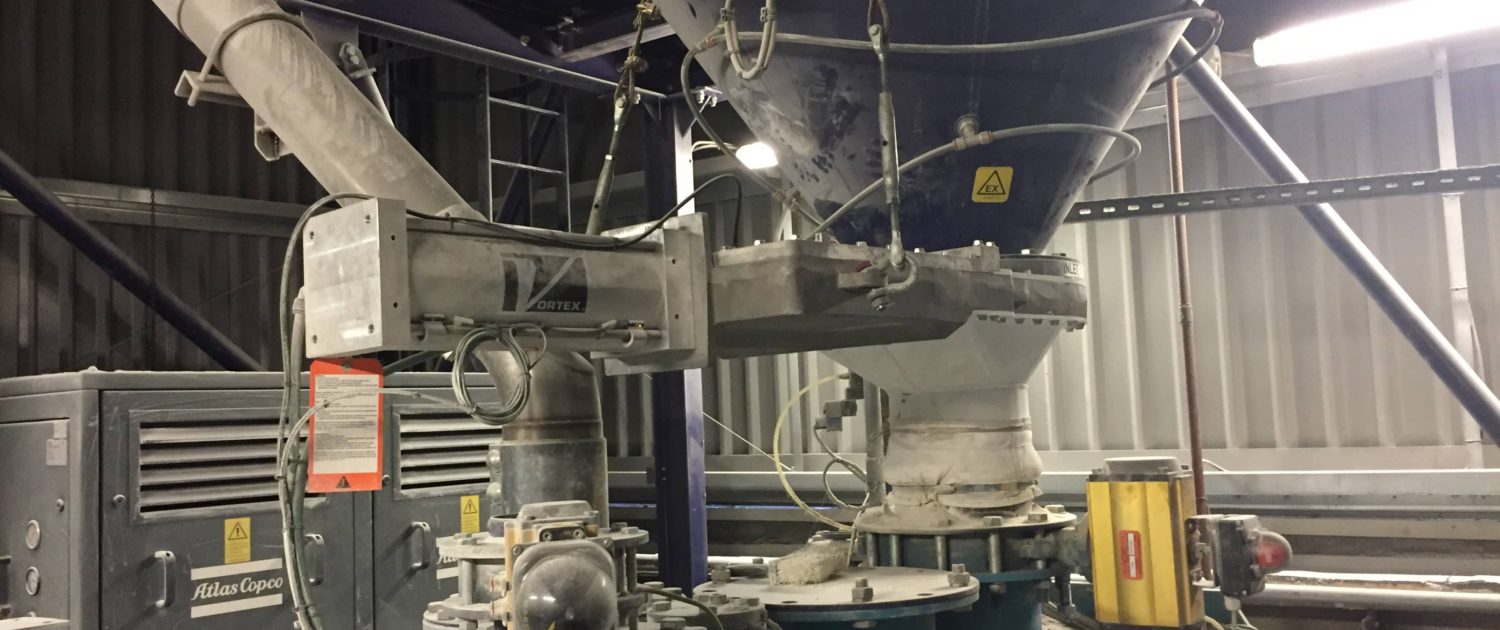
Client:
BASF – Redditch, UK
Quantity:
Size:
Application:
The manufacturing process includes bulk storage, batch weighing and pneumatic transfer of a large variety of ingredients to a large vacuum receiving hopper. From here, materials are discharged to a mixer then discharged to a high speed packing process.
Challenge: BASF had experienced problems with the existing butterfly valve on the outlet of their vacuum batch receiving hopper. Some of the coarse materials – typically quartz and flintag – are very abrasive, with sharp, jagged edges and a high bulk density. The butterfly valve blade was unable to open against a head load of high density compacted material.
Solution: Vortex HDPV2 Gate
Features:
- Pneumatically actuated.
- Designed to address higher-pressure applications up to 75 psig | 5 barg, depending on gate size.
- Rising blade design provides a positive material shut-off by means of a seal on the inlet of the valve. This eliminates the issues related to material packing, causing abrasion to an end seal. The seal is also protected from abrasion as materials from through the valve.
- Designed to seal fine materials in high aeration or pressure environments. This made the HDPV2 Gate an ideal solution at the vacuum receiving hopper, where local aeration was present to assist material discharge.
Results: BASF have been pleased with the valves performance and plan to specify Vortex valves and components for future applications.