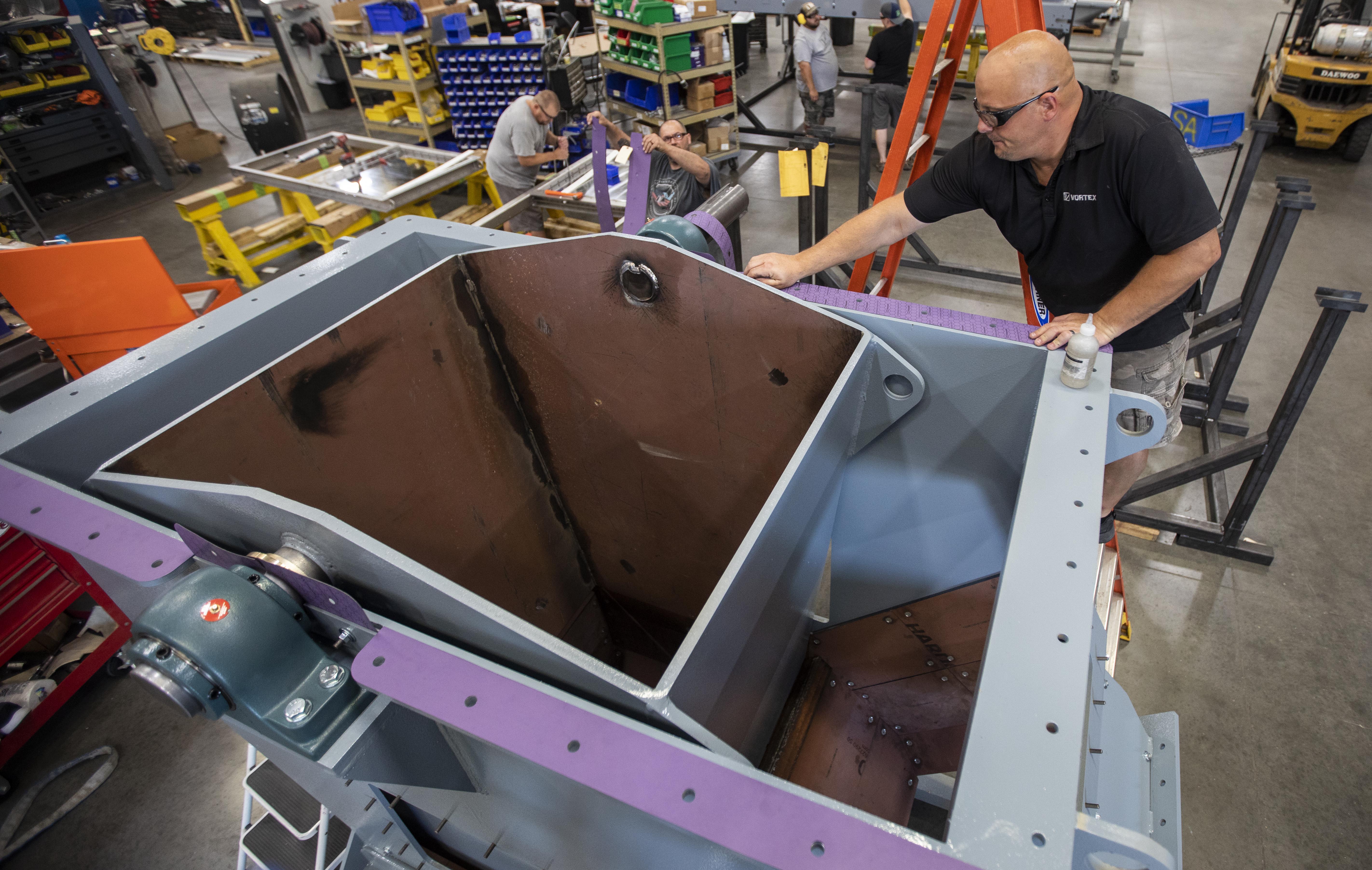
Client:
Quantity:
Size:
Application:
As featured in Dry Cargo International
by Kevin R. Peterson
Transporting clinker from the clinker cooler into storage silos can be an interesting proposition, writes Kevin R. Peterson – Vortex Global. Clinker is small in size, usually 3 to 25 millimeters in diameter. It typically has a Mohs hardness of 3.5 to 4. While it is not overly abrasive, handling large amounts of clinker can create major wear issues to equipment.
PROBLEMS WITH FLAPPER-STYLE DIVERTERS
Traditional flapper-style diverter valves are often considered for this type of application. Problems inherent with flapper diverters should be taken into account. Common problems with flapper diverters include:
- The blade typically rests on the interior housing. As material flows through the diverter, it gradually wears away the leading-edge blade seal as well as the leading edge of the blade itself. Eventually material flows into the outlet that is supposed to be sealed off.
- Changing the position of the blade to divert material to the opposite leg requires that the flow of material be stopped prior to the position change. This is rarely observed and creates material build-up, wear, and maintenance issues.
- Even though the clinker is originating from a ‘cooler’, the higher temperatures of the clinker precludes the use of any type of polymer or rubber blade sealing material. In the absence of a perimeter blade seal, material will eventually wear its way around the blade to create leakage.
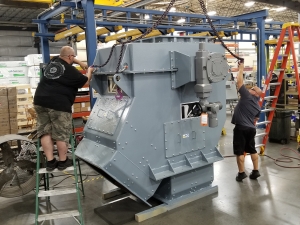
PIVOTING CHUTE DIVERTER
A preferred diverter style for applications handling clinker is the Vortex Global Pivoting Chute Diverter. The Pivoting Chute Diverter houses an independent chute within a diverter body. It offers features that are not available with the flapper-type diverter. These features include:
- The Pivoting Chute Diverter does not use a flapper to cover the off leg. There are no internal seals meaning seal wear and higher temperatures are not an issue.
- Flow of material through the diverter is unobstructed. The internal chute conveys material directly to the desired bin.
- The diverter can be shifted on a flowing column of material (shift on-the-fly). Stopping material flow prior to redirecting flow to the opposite leg is not required.
Most Pivoting Chute Diverters contain a removable, side access panel that allows for in-line inspection and maintenance without having to remove the diverter from place. Larger size diverters feature a top-mounted, drop-in chute due to the size and weight of the internal chute.
CLINKER CASE STUDY
When an Australian cement company was considering an upgrade to its facility, it realized issues would need to be addressed — especially with the diverter valve that would be required to direct clinker from the clinker cooler into two storage bins.
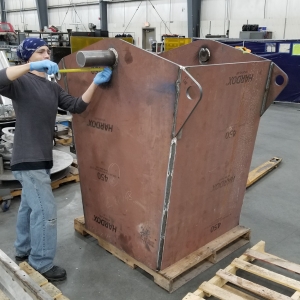
Company engineers performed an Internet search for valve manufacturers who worked with the cement industry. Upon examination of the Vortex Global website, the engineers were intrigued with what they found and sent an email to Vortex that began ‘To Whom it May Concern’. Upon receipt of the email, sales staff from Vortex Global’s UK office contacted the Vortex representative group in Australia, the Brolton Group, and, together, they began communicating with the cement company regarding their needs. Vortex Global manufactures slide gates, diverter valves, and telescoping loading spouts for dry bulk material handling. The company has been in business for over 40 years and works with all industries. Rather than marketing an off-the-shelf product, Vortex Global offers numerous modifications to standard products that address temperature, environment, material handled, etc… In doing so, customers receive a product that is reliable and offers superior performance. Additionally, Vortex has an Engineering Solutions division for bespoke projects that require distinctive considerations such as this project.
In discussing the project, the cement company had major concerns:
- The temperature of the clinker entering the diverter would be 300°C.
- The required flow rate would be 500tph (tonnes per hour).
- Ideally, the company was seeking a ‘more robust’ type of diverter that offered easy access to the internals for inspection and future maintenance.
Vortex evaluated the merits of the Pivoting Chute Diverter for this application. The company quickly agreed that the Pivoting Chute would address all its major concerns:
- Since there are no rubber or polymer blade seals to contend with, temperature would not be an issue. Additionally, the carbon steel exterior housing would be painted with a ‘high temperature’ paint.
- The diverter would be sized to handle the required material flow rate.
- Interior ‘wetted parts’ would be constructed of abrasion-resistant steel. Exterior access panels would be added for periodic inspection.
The final design featured an electric actuated diverter with a straight leg design and a 45° off leg. The diverter is 2,540mm tall with 900mm square inlets and outlets. The 1,524mm-tall interior chute is constructed of 19mm abrasive-resistant steel (400BHN). The body is constructed of 13mm carbon steel. The entire unit weighs 4,990kg. The Vortex Pivoting Chute Diverter was a perfect match for the customer’s application.
ABOUT THE AUTHOR
Now in his 25th year with the company, Kevin R. Peterson is the Business Development Director for Vortex Global. A board member of the Industrial Minerals Association of North America, Kevin travels extensively to meet with customers and customer prospects. He has created and shared hundreds of case studies and written numerous articles that share the successes Vortex products have experienced with industries that handle and process dry bulk material.