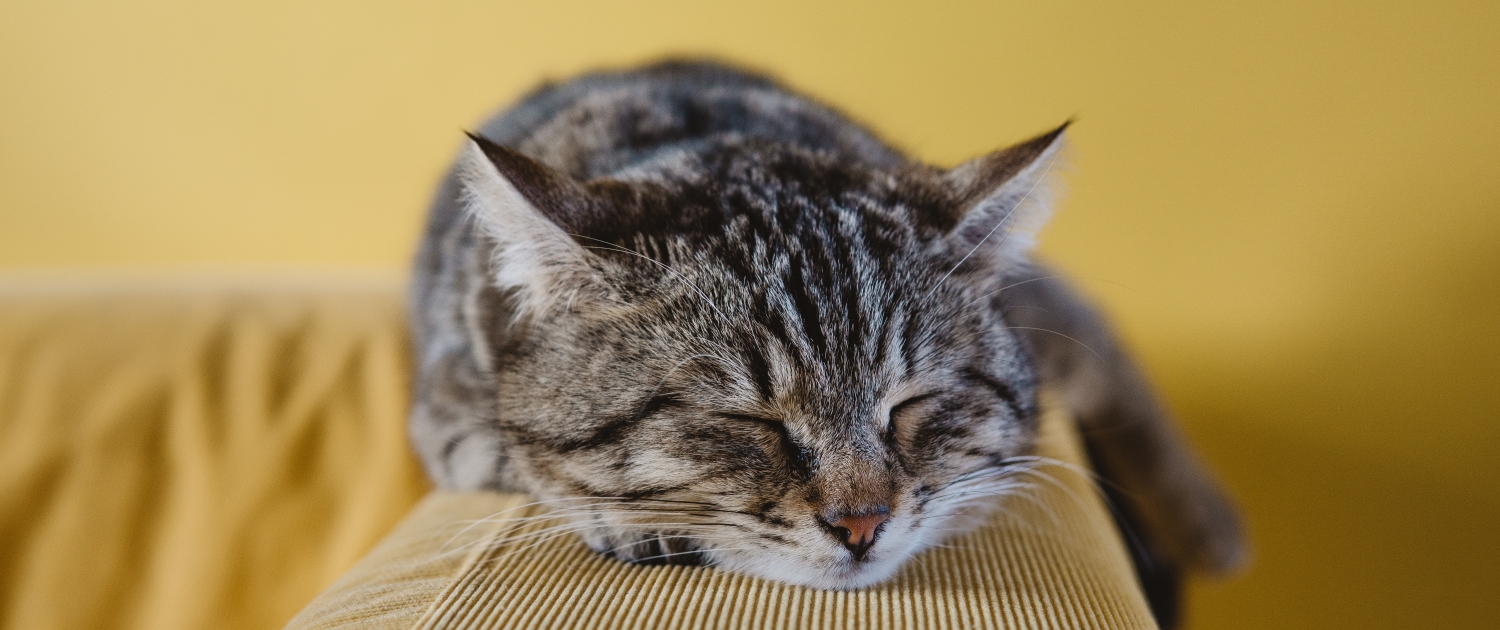
Client:
Quantity:
Size:
Application:
Features:
- Diverter body constructed from 6061-T6 aluminum.
- Blades, material contact areas & round inlet/outlet transitions constructed from 304 stainless steel.
- Blades are electropolished to handle sticky materials & accommodate wash-down.
- Outlet legs offset 60° from center.
- Removable access panels constructed from 1/4 in | 6 mm thickness Lexan polycarbonate.
- Oversized, double-acting air cylinder actuator. Air cylinder is equipped with a magnetic piston, to be used with magnetic reed switches for gate position indication.
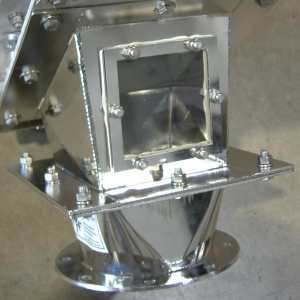
Results:
This client became acquainted with Vortex equipment three years prior to this request. Their successes with the Vortex Orifice Gate led them to consult their local Vortex representative about a new valve-related problem they were having.
As mentioned, the client previously used a flap diverter. They liked the idea of using a Vortex Seal Tite Diverter as a direct replacement using similar equipment. In particular, they enjoyed the Seal Tite Diverter’s removable access panel, which allows interior inspection and/or maintenance to be performed while the valve remains in-line. However, after researching the Vortex Gravity Vee Diverter, they were attracted to its dual-blade design with independent controls. This allows materials to be routed toward both destinations simultaneously, either destination independently, or both closed for a positive material shut-off. The ability to divert independently or simultaneously offered greater flexibility for their process. Previously, the client had a slide gate above the flap diverter so that the flap could be shifted without closing through a flowing column of material. Because the Gravity Vee Diverter can provide that same positive material shut-off, it would eliminate the need for an additional gate above.
Because of the material’s stickiness, the client was still attracted to the clean-in-place feature and hoped the two diverter design concepts could be merged.
Engineers from the client’s plant visited the Vortex facility. The two engineering teams collaborated and imagined a design with removable access panels on both outlet legs. The polycarbonate removable access panels allow for quick visual inspection and easy interior access, if clean-out becomes necessary.