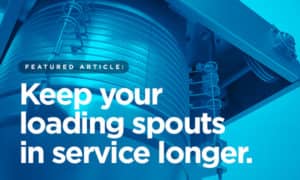
Client:
Quantity:
Size:
Application:
Purchasing a loading spout can be a huge investment for your company. The last thing you want is to worry about is replacing it in three to five years because of wear and tear. Selecting a quality spout with the correct parameters for your applications can prolong the life of your spout for decades. Here are four suggestions you can do to save unnecessary wear to your loading spouts.
Material Stream
First, check the angle of the head chute and trajectory of the product. The product stream should be entering the loading spout at the point it becomes vertical. This will ensure the product passes through the spout in a straight and steady stream. The only point the material should have any internal contact with the spout is at the bottom of the inner cone. If the loading trajectory is misaligned, the material will hit the upper sides of the cones and bounce down the spout creating premature wear and future maintenance issues.
Further, it may advisable to correct the trajectory of the material using sacrificial impact surfaces, rather than geometry, to attain vertical flow. Using the free-flow trajectory of the material not only results in a very large headchute, the vertical velocity of the material at the entrance to the spout can be very high, resulting in accelerated abrasive wear at the first cone. Impact plates placed in close proximity to the head pulley can gain control of the flow stream immediately after leaving the conveyor, and can be made of highly abrasion resistant materials like chromium carbide, wear plates marketed under various trade names (Hardox®, Astralloy, etc.), or elastomers that stand up to impact by particles, such as urethane, neoprene, or natural rubber.
Spout Positioning
If you are having to move the spout numerous times to match the inlet of a truck or other container, the best way to do this is to accessorize your spout with a positioner. The spout positioner consists of a support pan and a traversing hopper that aligns the spout on a single or a double axis so you don’t have to move the spout or the container. Using a positioner eliminates the chance of an angled chute or misaligned outer sleeve rings, which can result in the outer sleeve contacting the inner cones, tearing the fabric or catching the support rings and bending them. A spout that does not hang vertically will also result in abrasion to the sides of the cones as the material flows through them. Chances of damage due to handling are greatly reduced as well, since there is no reason for the operator to manipulate the spout into the desired position.
Materials of Construction
Another option is to upgrade the construction material of your loading spout. For coarse, abrasive, heavy material (like mineral ore) using abrasion resistant steels such as AR400, Hardox, or using bonded ceramics for the internal cones will help minimize wear on the contact areas of the loading spout. Upgrading the material will add weight and cost to a standard loading spout model, but it will prolong the life of the equipment, ultimately saving time and money.
The outer sleeve can also be upgraded to a neoprene coated polyester or nylon for more durability. The sleeve material choice should be reviewed in light of the service conditions as well: extreme cold will have a detrimental effect on certain polymer coatings, as will extremely hot products flowing through the spout. While reviewing the sleeve material, take a look at the dust collection specifications: while it is important to extract enough air to control fugitive dust, more is not always better. Overpowering the spout with excessive air withdrawal, leading to high static pressure differential with the ambient conditions, will cause the sleeve to collapse, pulling the support rings together, which has the effect of lifting the spout. If enough lift is generated, the spout will break vacuum and fall back in place—repeatedly. If the vacuum is not broken, and the static pressure continues to rise, the rings will collapse further, eventually distorting permanently and requiring replacement.
Maintain, Maintain, Maintain
Like any other piece of equipment, a loading spout will fail to perform the intended function without proper, regular maintenance. Periodic inspection of the wear points to maintain the spout will keep it functioning for many years. Check the inner stacking cones for pits, misalignments, and shavings, as well as damage to the support cables or straps. Make sure that the outer sleeve is not torn or ripped from contact with the stacking cones. Lift cables should be inspected for abrasion and fatigue due to contact with the various parts of the drive system. Additionally, control devices such as limit switches, probes, cable reels, and others, require regular inspection to insure the integrity of electrical connections, adjustments, and mounting fasteners.
What Else Should You Do?
Contact an experienced manufacturer willing to design and manufacture an engineered spout for your needs. Doing so will save you time and money.