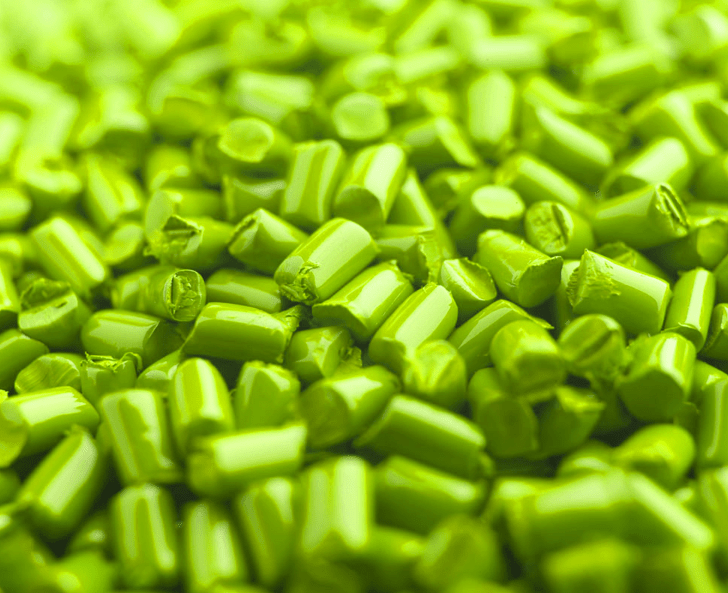
Client:
Quantity:
Size:
Application:
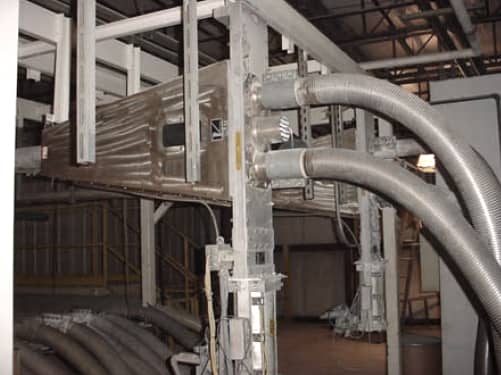
Features:
- Three-way diverting design.
Challenge: Replace an existing hose manifold station. The station is labor intensive, creates off spec product when employees make mistakes in manually switching the conveying lines, and produces material spills when employees do not secure the hose connections properly.
Results:
The diverters are used as convergers. Each diverter supplies material from two dedicated silos to an extruder. The middle inlet of each diverter is used as a material purge port to aid in clearing the line for certain materials handled.
The Vortex Flex Tube Diverter automates the transfer of material from the silos to the extruders. Hose switching errors that used to cause cross-contamination of material and material spills have been eliminated. Through use of the Flex Tube Diverter, the plant enhanced their material processing options, production lines run more efficiently, and off spec material was greatly reduced. Hose switching personnel are now used more efficiently within the facility.
The valves were installed in May of 2002. Several years later, they are performing exceptionally well.