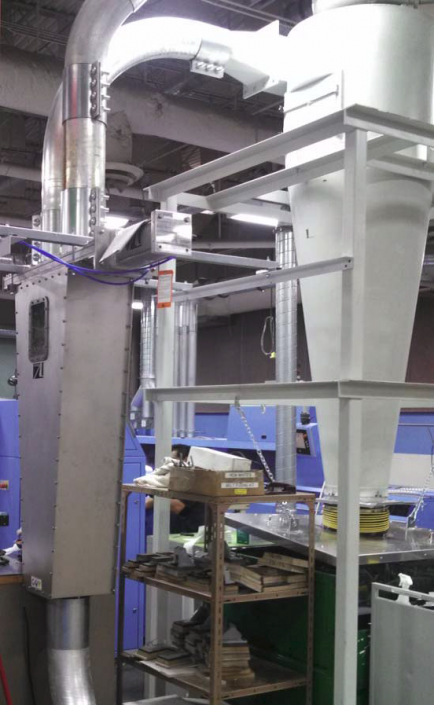
Client:
Quantity:
Size:
Application:
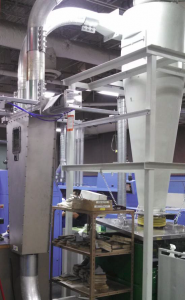
Material Characteristics:
- Paper strips: Lightweight & can be conveyed long distances through a dedicated line.
- Spine pieces: Heavier & can only be conveyed short distance.
Features:
- Two-way diverting design.
- Diverter body & housing constructed from aluminum.
- Blade, flexible hose & other material contact areas constructed from 304 stainless steel.
- Inlet & outlet weldments constructed from carbon steel.
- Removable access panel/viewing panel constructed from clear polycarbonate.
- Double-acting air cylinder actuator equipped with a magnetic piston, to be used with magnetic reed switches for gate position indication.
Results:
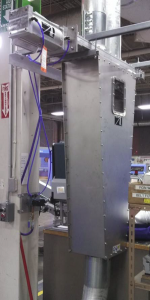
The bookmaking process requires individual sheets of paper be stitched into a spine and cover. The resulting stack of paper is then trimmed so that all pages are perfectly aligned with each other. The paper trimmings must then be collected for disposal or recycling.
For this printing company, when conveying material away from the trimmer, each trimming type (paper or spine) poses unique issues. When considering the material characteristics, a diverter valve was needed to direct spine pieces toward a nearby receiver, or paper strips toward a bailer located further away. However, many diverter valves have complications when handling strips of material. The strips often collect in various areas of the diverter, causing it to seize up and not work properly.
In the client's previous process, a direct line transferred paper strips toward the bailer; however, the spine pieces were removed from the trimmer by hand. The time spent hand-picking spine pieces added considerable downtime and lagged the entire trimming process.
A Vortex Flex Tube Diverter was recommended to address all the issues inherent with this application. The smooth, unobstructed actuation between ports eliminates any pockets where material can lodge or become trapped. To divert the trimming types toward their proper destination, an operator simply uses a toggle-switch, located between the trimmer and the diverter valve. A viewing panel allows the operator to see which trimming type is being conveyed through the diverter at all times.
Hand-picking spine pieces from the trimmer is no longer an issue.