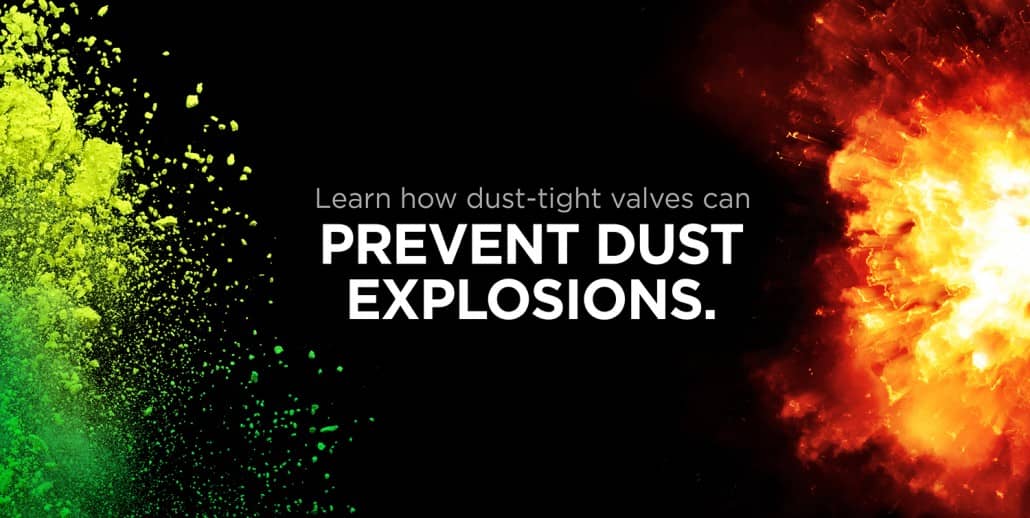
Client:
Quantity:
Size:
Application:
Is Your Plant Safe? Learn how to prevent dust related hazards.
One of the constant challenges a Plant Manager encounters in a dry bulk processing facility is reducing dust emissions from the internal system into the external environment. The source of dust leakage to atmosphere can come from a wide variety of equipment throughout the process; however, slide gates are often the main culprit.
The vast majority of process valves produced in the world are made for liquid and gas applications, where the seals are composed of EDPM, PTFE, Viton, or some type of elastomer. This type of seal design works great for fluids, but often fails to stand up to blast or frictional abrasion caused by dry particulate.
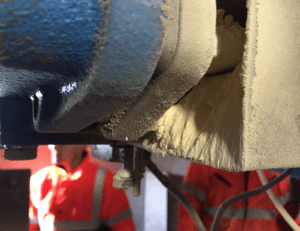
So why should processors be concerned about fugitive dust from a process valve? There are many reasons to minimize dust in a plant, but the most important is undoubtedly safety as it applies to dust explosions.
Dust explosions may be classified as being either “primary” or “secondary” in nature. Primary dust explosions may occur inside process equipment or similar enclosures, and are generally controlled by pressure relief through purpose-built ducting to the external atmosphere. Secondary dust explosions are the result of dust accumulation inside a building being disturbed and ignited by the primary explosion, resulting in a much more dangerous uncontrolled explosion inside the workplace. Historically, fatalities from dust explosions have largely been the result of secondary dust explosions.
On February 7, 2008, a huge explosion and fire occurred at a sugar refinery northwest of Savannah, Georgia, causing 14 deaths and injuring 38 others, including 14 with serious and life-threatening burns. The explosion was fueled by massive accumulations of combustible sugar dust throughout the packaging building,
It is just not sugar dust that can fuel an explosion. There is a long list of industries vulnerable to the hazard of dust explosions including, but not limited to, agriculture, chemicals, food (such as candy, spice, starch, flour and feed), grain, fertilizer, tobacco, plastics, wood, forest, paper, pulp, rubber, furniture, textiles, pesticides, pharmaceuticals, tire and rubber manufacturers, dyes, coal, metal processing (such as aluminum, chromium, iron, magnesium and zinc), recycling operations and coal. Given this long list of vulnerable industries combined with the difficulty in identifying a combustible dust threat, OSHA suggests completing an in-depth dust hazard assessment covering the following areas:
- Materials which may be combustible
- Processes which utilize any combustible dust
- Open and especially hidden areas where dust may collect
- Opportunities which may cause dust to become airborne
- Any source of ignition
The key to the hazard assessment is correctly identifying whether or not the dust is indeed combustible. The National Fire Protection Association (NFPA) 654: Standard for the Prevention of Fire and Dust Explosions from the Manufacturing, Processing and Handling of Combustible Particulate Solids and NFPA 454: Standard for Combustible Metals, Metal Powders and Metal Dusts both define combustible dust as “any finely divided solid material that is 420 microns or smaller in diameter and presents a fire or explosion hazard when dispersed and ignited in air.” Other variables to consider, in addition to particle size, are how the dust will be dispersed, what kind of ventilation is available, air currents, sources of ignition, and the presence of physical barriers to either provide dust confinement or which provide separation of work processes.
The European Union has implemented more robust standards as it applies to environments with potentially explosive dust present. The standard is referred to as ATEX, which is derived from the French title of the 2014/34/EU directive: Appareils destinés à être utilisés en ATmosphères EXplosibles.
Like NEC standards, ATEX requires certification for different levels of hazardous dust environments on all electrical equipment and devices. One of the more significant differences between NEC and ATEX is that ATEX requires all mechanical equipment with moving parts to also carry certification. The chart below outlines the how ATEX and NEC standards inter-relate as it applies to area classifications regarding combustable dust environments.
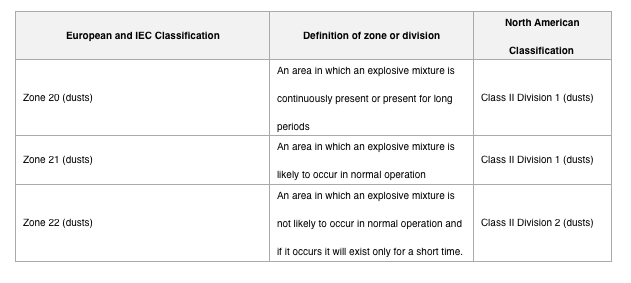
As a global supplier, Vortex adheres to NEC, IECEx, ATEX, and other international standards as it applies to minimizing the dangers of combustible dust. Though there are no U.S. regulations in place that covers certification of mechanical devices, Vortex maintains certification on its valve products to cover ATEX zones 22, 21, and 20. Each product is tested and examined to ensure the physical valve cannot create a source of ignition to combustable dusts or gases.
If you are looking for a valve product that gives you piece of mind, a return on investment, and is backed by “know how” experience, then Vortex is the right supplier for you. Global dry bulk processors such as Nestle, Kraft Foods, P&G, Dow, DuPont, Owens Corning, Cargill, ADM, Monsanto, Exxon, Shell, Omya, Sabic, PPG, Linde, BASF, and many others rely on Vortex to deliver efficient and safe solutions for their processes.