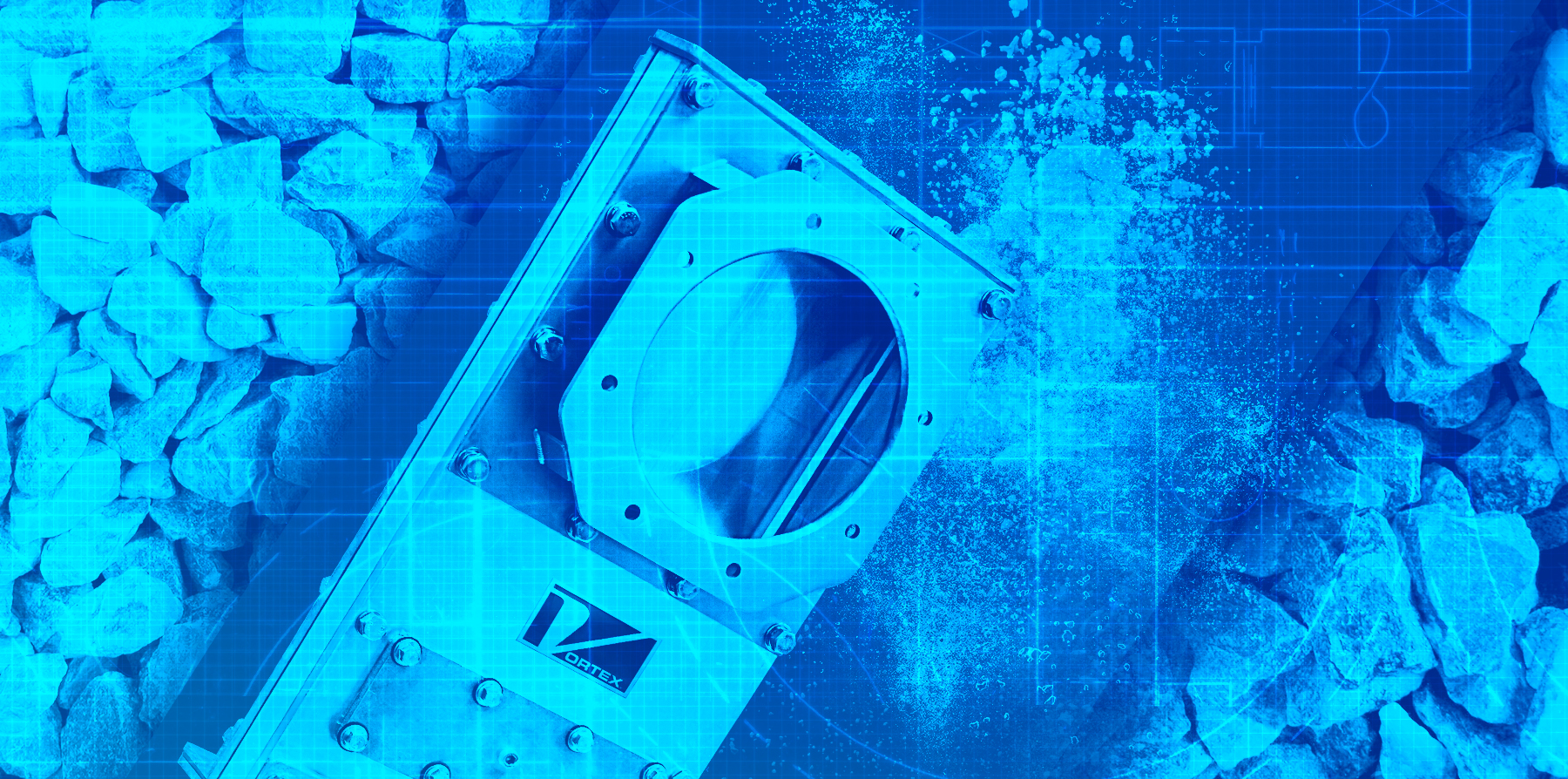
Client:
Quantity:
Size:
Application:
Limestone: What it is
Limestone is one of the most common natural forms of calcium carbonate (CaCO3). Calcium carbonate comprises more than four percent of the Earth’s crust, and is found worldwide.
Limestone is the sedimentation produced from millions of years of fossilization, consisting mostly of shells from small snails, shellfish and coral. Chemically, limestone and other forms of CaCO3 are identical. But in terms of purity, whiteness, thickness and homogeneity, limestone is quite different. It is among the most useful and versatile materials known to man.
Limestone is a biogenic rock that is more compacted, compared to other forms of CaCO3. As it is used for industrial purposes, CaCO3 is extracted by mining or quarrying. To produce limestone, CaCO3 is crushed and processed into powder form as ground calcium carbonate (GCC). Depending on size and other material properties, limestone powder has many industrial and pharmaceutical applications.
Limestone and other forms of CaCO3 are demanded worldwide by many industries. It is used:
- In paper production because it has high brightness and light scattering characteristics, and because it is an inexpensive filler to make bright, smooth, opaque paper.
- As an extender in paint production. Paints can consist of as much as 30% CACO3, by weight.
- As a filler in adhesives and sealants.
- As an effective dietary calcium supplement, antacid, phosphate binder or base material for medicinal tablets.
- As an additive in baking powder, toothpaste, dry dessert mixes, dough and wine.
- In agriculture and in the production of animal feed.
- To treat water and wastes.
- As an ingredient of cement.
- In the glass and steel production processes.
- As a neutralizer in water and soil.
Information courtesy of Industrial Minerals Association – North America (IMA-NA).
Case Study: Gates & Airlocks Handling Limestone
In 2016, a limestone processor in the northern United States consulted Vortex to discuss a processing need.
The Application
In this client’s process, finished limestone is stored in a silo. From there, materials are discharged into three-way chutework and routed toward three different destinations:
- Destination #1: Through Rotary Airlock #1, to be pneumatically conveyed to Packaging Line #1;
- Destination #2: Through a loadout spout, used to fill open trucks; or
- Destination #3: Through Rotary Airlock #2, to be pneumatically conveyed to Packaging Line #2.
Three-way chutework is used to route materials toward each of these destinations.
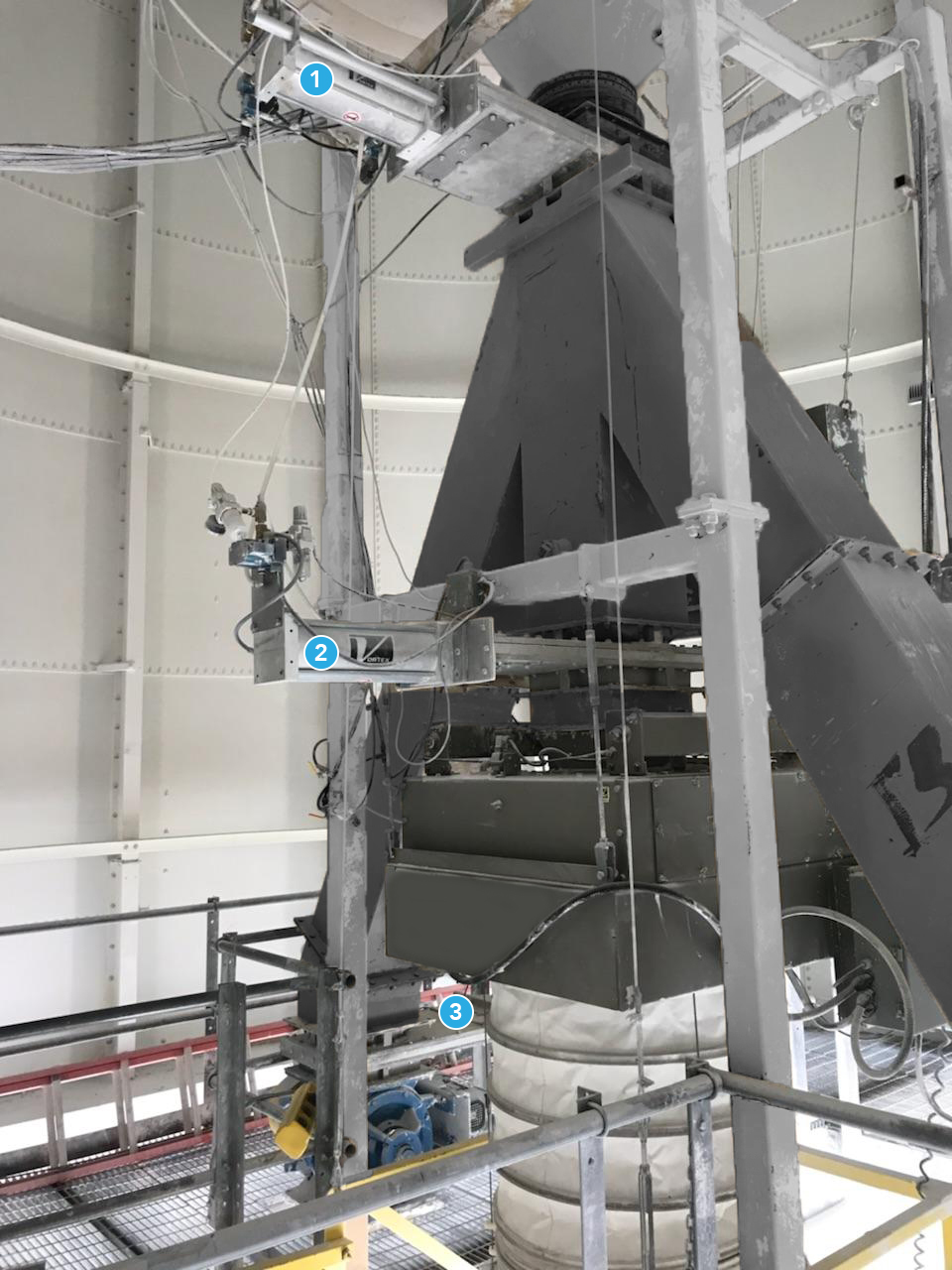
Below the silo, a slide gate is used as a flow control valve so not to flood the system.
Above each airlock, a slide gate is used as a process gate to introduce materials into the rotary airlock. The rotary airlock feeds a pneumatic convey line, where limestone powder is conveyed by positive pressure at 7 – 9 psi | 0.5 – 0.6 bar.
Above the loadout spout, a slide gate is used to prevent truck overfill.
For added capacity, the client has replicated this system for a total of:
- 3 storage silos;
- 3 three-way chutes;
- 6 rotary airlocks;
- 6 pneumatic convey lines;
- 3 loadout spouts; and
- 12 slide gates.
Prior to this project, the client was using slide gates supplied by another manufacturer. Those gates were in service for 2 ½ years – and throughout, had constant issues with poor sealing and material leakage. A solution was needed to resolve these issues.
The Solution
In order to seal against pneumatic pressures originating in the convey line below, Vortex recommended its Clear Action Gate be installed above each rotary airlock. Because aeration is also used in the silo to fluidize materials, Vortex further recommended its Clear Action Gate be installed at the silo discharge and above the loadout spout.
At their advice, this limestone processor sourced twelve 14 in | 355 mm Vortex Clear Action Gates.
Addressing Material Migration & Packing in the Gate Seals
All twelve gates are equipped with a Special Service Inlet & an air purge assembly.
A Special Service Inlet acts as a funnel to direct material flow through the center of a gate’s opening. It is designed to create a slight void between the blade, seals and the material flow stream. This creates a “dead pocket” that allows residual materials remaining at the leading edge of the blade to fall away into the process line below, prior to the blade entering its end seal. By preventing material packing upon gate closure, a Special Service Inlet provides a better seal of materials and dusts, extends seal service life, and reduces maintenance frequency/spare part requirements.
In order for the air purge assembly to be effective, the gate bodies are sealed with solid aluminum covers and gasketed with silicone rubber. A purge port is tapped into the upper bonnet area so that differential pressure can be introduced, in order to prevent fine materials from migrating past the seals and collecting in the body of the valve. Otherwise, material packing and actuation issues can occur.
Controlling Flow Out of a Silo
Three of the Clear Action Gates – the gate below each silo – were equipped with an Infinite Variable Positioning (IVP) Assembly. The purpose of positioning assemblies is to control and maintain volumetric flow rates. This improves process accuracy with more precise batchweight calculations and reduced fill times between workstations.
Unlike other positioning assemblies, the IVP allows total control of variable positioning on both the opening and closing strokes. It uses a linear output transducer to relay blade position feedback along the entire stroke of the blade. This client opted to automate their IVP assemblies using a programmable logic controller (PLC). Because the assembly is automated, the blade can be actuated in highly accurate increments of +/- 2%.
Results
It took this client less than two months to realize a significant improvement in the efficiency of their loadout and packaging processes. Today, this client operates more than 20 Vortex Clear Action Gates – all of which are running smoothly and without error.
For the future, this limestone processor plans to replace other equipment in their facility with Vortex components.
“This application is a great example of the versatility of Vortex Clear Action Gates,” explained Shawn Opat, director of regional sales at Vortex. “In this system alone, the Clear Action Gate proves its ability to seal against pressures originating below, its ability to be used at the silo discharge, its ability to be used as a process gate at the loadout station, and a configuration of Clear Action Gates which creates a diverting solution.
“It was a pleasure to work alongside this client through their processing issues. We look forward to providing them with additional solutions in the future.”