Key Features
Live loaded, wear compensating hard polymer pressure plate seals
Shimming system for in-line maintenance
Optional Special Service Inlet minimizes material contact with the seals
Displacement area as an alternative to packing materials into an end seal
Positive seal of materials/dust-tight seal across the blade and to atmosphere
Mechanically self-cleans its seals on the opening stroke, if actuated to full-open
No pinch points or exposed moving point for safety
No internal cavities to prevent wedging, lodging & spoilage
Narrow profile for limited space applications
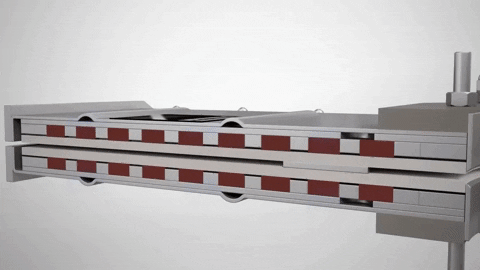
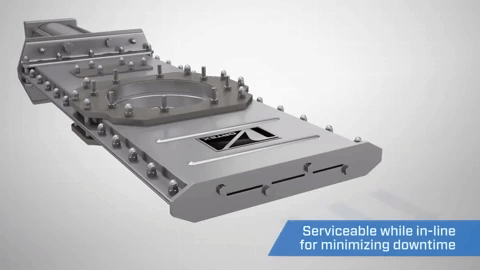
in-line maintenance
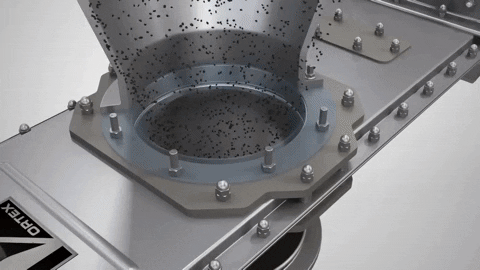
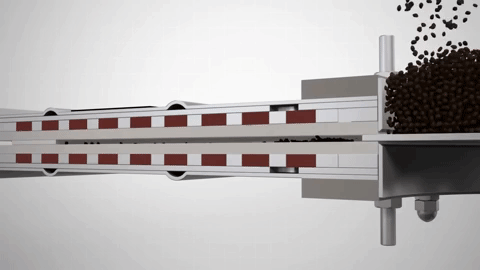
Tech Specs
Model No.
GRXX
Conveyance Type
Gravity flow & dilute phase pneumatic conveying applications. Can handle differential pressures up to 15 psig | 1 barg | 0.1 MPa, depending on gate size. Can be used in pressure or vacuum systems.
Materials Handled
Non-abrasive to moderately abrasive powders, pellets and granules. Modifications available for handling corrosive materials and/or for wash-down.
Standard Sizes
2 – 16 in | 50 mm – 400 mm
Inlet & Outlets
Available in round sizes.
Overall Height
2 – 3 in | 50 – 75 mm
Weight
10 – 225 lb | 5 – 100 kg
Flange Options
Standard stud bolt pattern, thru-bolt pipe connection, ANSI #125/150, DIN PN10
Custom flanges are available
Material Temperatures
180° F | 80° C for standard gate, with modifications that allow up to 400° F | 205° C
Body/Frame Options
Aluminum, 304 stainless steel, painted carbon steel
Material Contact Options
304 or 316L stainless steel
Pressure Plate Options
Nylon, PET, UHMW-PE, glass-filled PTFE, molybdenum disulphide-impregnated nylon
Load Seal Options
Natural rubber and/or silicone rubber
Drive/Actuation
Double-acting air cylinder, hand wheel/crank, chain wheel, electric actuator
Position Confirmation
Magnetic reed, proximity or mechanical limit switches, and/or clear bonnet cover for visual indication
Other Options
Sealed body air purge (Only available on traditional Orifice Gate)
Special Service inlet
Compliance
ATEX Zone 20 (internal), ATEX Zone 21 (external), FDA
Modifications
G
CS Body/S4 or S6 Contact: Offered in 2” thru 14”. All actuator options are available. Traditional and over-sized cylinder option are available up to 5” size. The valve body is carbon steel and bore matches standard 11 Ga. (0.120 Wall) tubing. 3/8” thick Carbon Steel out flanges and 304SS sleeve inserts. Bonnet access covers, Power Plate, and End Plate are Carbon Steel construction. All fasteners are zinc plated and there are NO acorn nuts. (Valve designed for indoor service).
H
AL Body & Outflange/AL Contact: Bore matches standard 11 Ga. (0.120 Wall) tubing. Out Flanges and sleeve insert is 6061-T6 Aluminum Construction. All fasteners are 18-8 SS.
F
AL Body & Outflange/S4 or S6 Contact: Bore matches standard 11 Ga. (0.120 Wall) tubing. 3/8” thick Out Flanges and sleeve inserts are 304SS construction. All fasteners are 18-8 SS. *Must choose material contact.
J
SS Body & Outflange/S4 or S6 Contact: Bore matches standard 11 Ga. (0.120 Wall) tubing. 3/8” thick Out Flanges and sleeve inserts are 304SS construction. All fasteners are 18-8 SS. *Must choose material contact.
HT3
250°F-300°F (121°C-149°C) HIGH TEMPERATURE SERVICE: Replace standard natural rubber Load Seal and Void Filler on back of Pressure Plate with silicone rubber only (remove void filler).
HT4
400°F-450°F (204°C-232°C) HIGH TEMPERATURE SERVICE: Replace standard Pressure Plate, Shim Spacer and Load Seals with 25% Glass-filled Teflon Pressure Plate, Shim Spacer and Silicone Load Seals (Void Filler is removed). Replace standard Air Cylinder with Viton seal Air Cylinder. Replace standard SBR Flange Gaskets with 3/16” silicone sponge Flange Gaskets. This option is NOT food grade.
WS1
WATER WASHDOWN / STICKY MATERIALS: Replace Nylon6/6 Pressure Plates and Spacer Shim with PET Pressure Plates and Delrin or Acetron GP Spacer Shim. Replace standard Slide Blade with electropolished Slide Blade.
*Additional modifications available based on applications.
Options
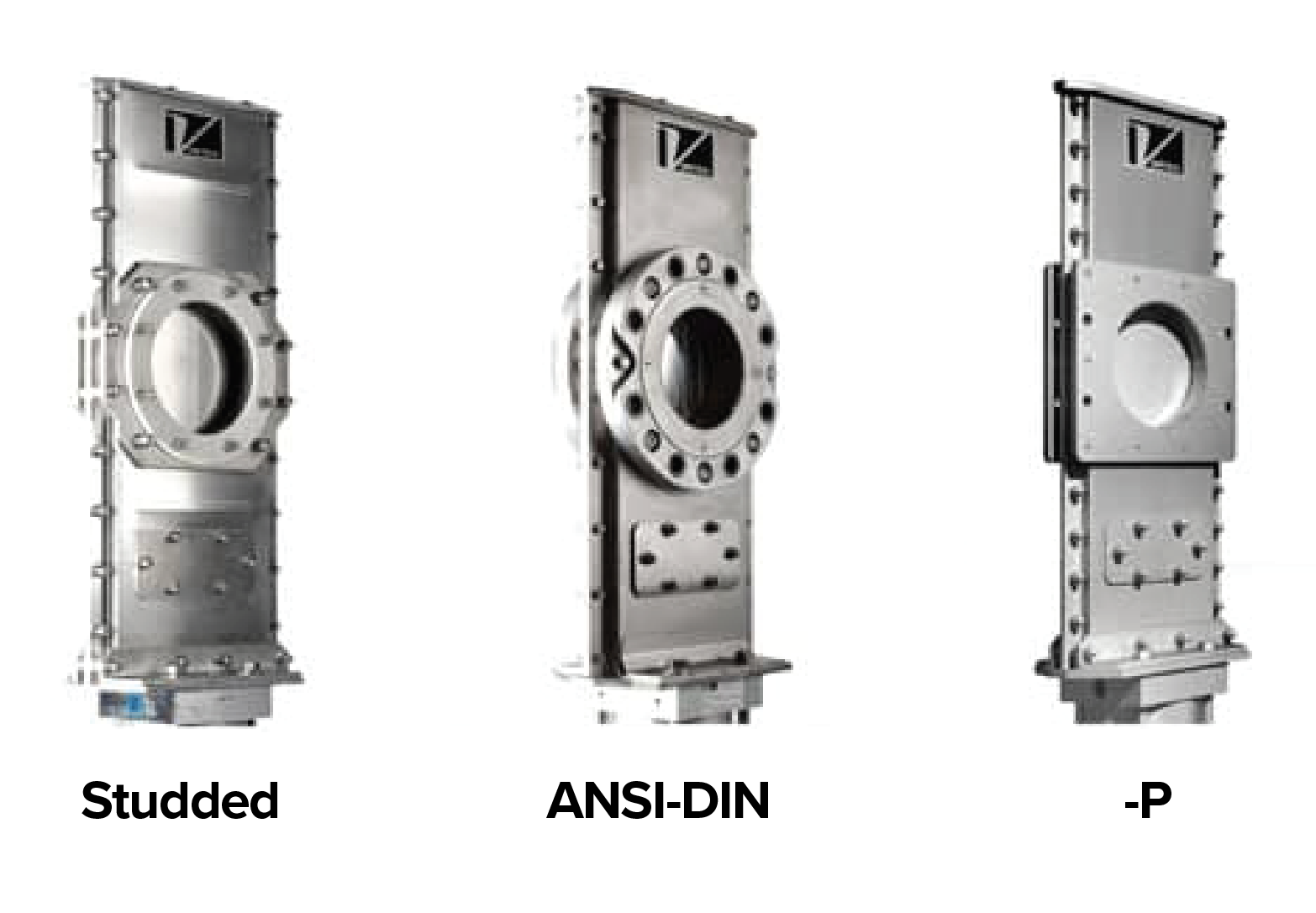
Power of Comparison
Vortex Orifice Gates vs. Alternatives
• Many alternative slide gates and butterfly valves rely on soft rubber seals which are directly exposed to the material flow stream. These seals rapidly erode or tear away in service. Others rely on bonnet packing, which can relax and allow material packing in the seals. These deficiencies promote leakage of materials and dusts past the gate and to atmosphere, in addition to actuation issues and several other maintenance concerns. The Vortex® Orifice Gate™addresses these issues by incorporating "live loaded" hard polymer pressure plate seals. Hard polymer provides greater wear resistance and longer service life than alternative sealing materials. The hard polymer seals are "live loaded" with compressed rubber backing to ensure even as the polymer experiences frictional wear from many actuations over time, the rubber load seals continuously force the polymer seals against the sliding blade. The seals are also shielded from the material flow stream, to protect them from abrasion. This design maintains the gate's positive seal of materials/dust-tight seal with infrequent maintenance intervention.
• Many alternative slide gates and butterfly valves have open cavities where materials can wedge and prevent positive material shut-off. Wedging can also create seal wear and material degradation, and can cause a gate to seize and bind. Wedged materials also create risk for cross-contamination and spoilage. To prevent wedging and ensure positive gate closure, the Orifice Gate’s sliding blade is designed to mechanically clear materials away from the sealing surfaces with each opening stroke. This ensures migrant materials are forced back out of theseals and are discharged into the process line, rather than packing in the seals and causing actuation issues.
• Many alternative slide gates allow metal-on-metal sliding, which creates galling. This causes agate to seize and bind, and can create foreign metal fragment contamination. The Orifice Gate's hard polymer seals eliminate metal-on-metal contact to resolve each of these concerns.
• A butterfly valve's rotating disc is directly exposed to the material flow steam, which creates wear to the disc itself. The exposed disc also disrupts convey line pressures and obstructs material flow as they pass through the valve, which can cause line plugs and other maintenance concerns. To resolve these issues, the Orifice Gate’s sliding blade is machined with an unobstructed, full-bore orifice that maintains convey line pressures and allows unrestricted material movement.
• If the pressure plate seals have partially worn and the compression load is lessened, slight dusting may be present through the weep holes at the front of the gate. With this maintenance indication, the Orifice Gate's shimming system can be utilized to restore the gate's dust-tight seal. Unlike alternative valves, which require spare parts be kept on-hand for seal maintenance, the Orifice Gate requires removal of parts. By simply loosening the nuts along the lateral aspectsof the gate, shim(s) can be removed from each side and the nuts retightened to restore the pressure plate seals' compression load. This maintenance process can be performed while thegate remains in-line, and can be repeated several times before the shims and pressure plate seals must be replaced.
• The Orifice Gate is designed with several replaceable parts, including actuator, sliding blade, clevis, pressure plate seals and shims, among others. If maintained and operated as recommended, these should be the gate's only wear parts. In several cases, this has allowed an Orifice Gate to remain in service for many years –and sometimes, even decades.